Machine shops can be dangerous places, but a combination of planning, housekeeping and the proper safety equipment reduces the risk of injuries, audits and lost time.
When you look at a machine tool, it can be easy to forget how mind-bogglingly terrifying it can be. Hundreds of thousands of pounds of high-powered machinery designed to drill, cut, scrape, ream or otherwise violently remove metal from workpieces in the form of chips. The reason it’s easy to forget that is because of the rigorous and constantly updated safety regulations that govern how machines are built. Obviously, machinists have a healthy respect for their machines, but no matter how careful a shop is, accidents happen. However, steps can be taken to prevent them.
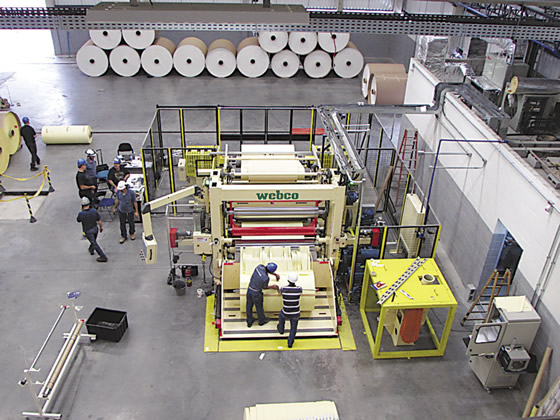
Folding Guard partitions ensure equipment at Brazilian automotive manufacturer Webco are up to all current safety codes.
“Safety is a big deal,” said Keith Jennings, president of Tomball, Texas, manufacturer Crow Corp. and a CTE columnist. “We don’t want anybody getting harmed in any form or fashion because we care about our employees, but from an insurance and financial standpoint, it’s expensive. It creates drama and stress, and it causes your insurance premiums to increase.”
Crow Corp. hasn’t had an employee miss work due to injury in several years, Jennings continued. He attributes this to two main points: training employees with an established safety plan and keeping the shop floor clean, organized and well-maintained.
A Man, A PlanCrow outsources its payroll and human resources, as do many machine shops. The company hired Paychex, which offers a safety department and consultant service to its customers, providing physical and digital materials and keeping owners up to date with the latest information regarding workplace safety.
“We make sure our supervisors have access to all the material and can use it when needed,” Jennings said. “We also get lots of posters and visuals that emphasize safety best practices and potential hazards to avoid. We make sure safety is something people are aware of and thinking about.
“If we hear of a certain type of safety issue that’s relevant or pressing or OSHA develops a new requirement, the company issues a safety alert and incorporates that information into our plan,” he continued.
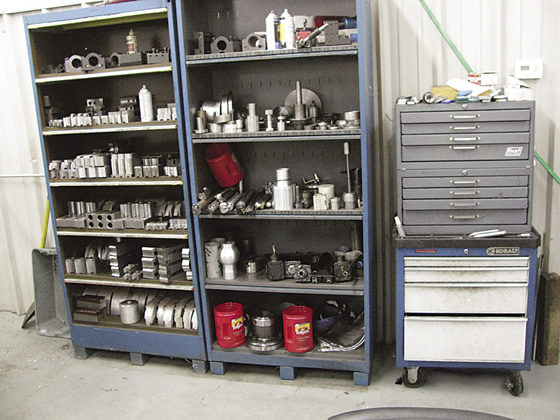
A well-defined organizational system—and ensuring employees stick to it—keeps parts and tools from cluttering the shop floor at Crow Corp.
Ultimately, though, he admitted that a shop can hang as many posters, conduct as many safety meetings and mandate as much training as it wants, but accidents still happen. Jennings said: “It doesn’t matter how careful you are, human beings just do goofy stuff, even when they know better. So, another part of our plan is to make sure our managers and supervisors are well-trained. That way, when they see employees being careless or unsafe, they can hopefully step in before an incident occurs.”
In addition to a safety plan, machinists can keep themselves current on safety policies and procedures through ongoing training. The National Institute for Metalworking Skills Inc. (NIMS) not only offers a measurements, materials and safety introductory-level standard, but incorporates safety into all its machining credentials.
“In all of our credentials, there are two components,” explained James Wall, executive director of NIMS. “The first is being able to actually demonstrate the skill, and the second is a written test to make sure people have all the relevant technical knowledge behind that particular content area. So, if someone’s doing a CNC programming credential, there will be questions about safety issues that pertain specifically to CNC, but there could also be something about safety glasses and power lockout/tag-out mechanisms, which would apply to any situation in a shop environment.”
Good HousekeepingThe other pillar of shop safety, according to Jennings, is shop housekeeping. Crow’s machine shop features painted floors, bright lighting, ample space around machines and—perhaps most importantly—as little clutter as possible.”
“A lot of shops don’t have a lot of extra space, which means they’re limited in how they can arrange things,” Jennings noted. “I’ve visited shops that are a safety hazard simply because they lack adequate space to properly arrange and store everything, which can really impact the quality of housekeeping and maintenance. We’re limited in our shop’s total space, but ensure we arrange equipment with plenty of space around the machines. You need enough adequate space to move around, check things and perform maintenance, all very important.”
Housekeeping might be a bit of a vague term, but Jennings has a simple philosophy: He doesn’t want employees working in a shop environment that he as an owner wouldn’t be happy working in. Painted floors look better and they also brighten up the shop and are easier to keep clean. Good lighting ensures machinists aren’t straining their eyes, but also makes potential hazards easier to spot. Keeping a shop clean makes for a good first impression on customers and also minimizes the number of potential problems in the shop.
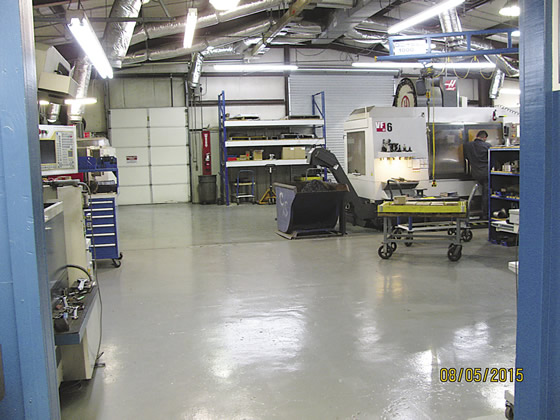
Painted floors, bright lighting and adequate space for movement without clutter are key elements in how Crow Corp. keeps its machine shop safe.
“Another important safety factor a lot of shops overlook is simply purging clutter once every year or two and thoroughly cleaning,” he said. “Guarding and safety practices are important, but you can’t underestimate the positive impact of good housekeeping.”
NIMS’s Wall provided some data to support this. NIMS engaged in a collaborative research project with Fireman’s Fund Insurance Co., Novato, Calif., to identify the most pressing safety issues in the industry. According to the company’s data, the most common issues have little, if anything, to do with the machines themselves.
“It’s not the complicated stuff that’s an issue, it’s the simple things that maybe people take for granted,” Wall said. “The majority of incidents were from slip and falls, back injuries from improper lifting technique—most of it wasn’t technology related. In most cases, the machines are guarded extremely well, so unless someone is doing something really out of the ordinary or doing repair and maintenance work where they’ve gone around the safety interlocks, it’s usually not an issue with the machine.”
Surviving the AuditWhile injury avoidance is the primary reason to follow good safety practices, it’s also necessary to meet the approval of auditors—be they from regulatory bodies or a shop’s insurance company.
“Like all shop owners or managers, we prefer to keep safety audits from insurance companies or OSHA to a bare minimum,” said Crow 's Jennings. “The best way to avoid them is to adhere to a good safety plan and make it a part of your shop’s culture. We have insurance adjusters who visit our shop every year or two, so it’s important we give them a good impression and make sure they leave here with very little or no concern about our shop’s safety.”
When they observe a shop taking its employees’ safety seriously, he added, it’s much easier to renew policies and minimize rate increases. Shops that incur frequent claims or have a high rate of incidents are going to be scrutinized far more closely. But even shops with a good track record are expected to have an established and formal safety plan.
“We don’t have safety meetings every day,” Jennings said, “but we address it, have safety training and meetings from time to time and provide access to relevant materials for our employees. I can show the auditors our safety manual, but they can also see that our employees are practicing proper techniques, utilizing proper safety equipment and working in a tidy fashion.”
In addition to insurance companies, there are governmental regulatory bodies setting standards by which all machine shops must abide. To remove an element of worry, Folding Guard, Bedford Park, Ill., ensures its Saf-T-Fence partitions, Drop-N-Lock bracket systems and other products are compliant.
“In theory, manufacturers should be designing safety equipment that meets all those specifications—sweep space, mesh size and placement, safety switches,” said Colin Burt, marketing manager for Folding Guard. “However, there are a lot of regulations to be aware of. OSHA is the big one, but there’s also ANSI regulations in America, CSA regulations in Canada, specific guarding standards like ISO 14120 and EN 953, and they’re all being updated all the time. Sometimes, a machine starts out up to code but gets outdated; other times, there are issues inherent to the design.”
While regulatory agencies are able to ensure a fairly high level of compliance, there are some blind spots, according to NIMS’s Wall. In addition to shops simply not following established safety regulations, most school environments do not fall under the purview of OSHA, for example, so the programs in many states are not subject to OSHA inspections.
“Those [school] facilities are typically very safe and I don’t mean to imply otherwise, but just because OSHA exists, that doesn’t mean it applies everywhere,” Wall said. “The reason we put such an emphasis on safety is that our certifications are designed to be validation from the industry to confirm that people have a solid knowledge base. Even though people might go through safety training at work or school, the credential is a way to validate that training and demonstrate that they’ve met the national industry standard for both understanding and practice.”
When it comes to meeting those codes and regulations, nothing beats an experienced eye, Burt said.
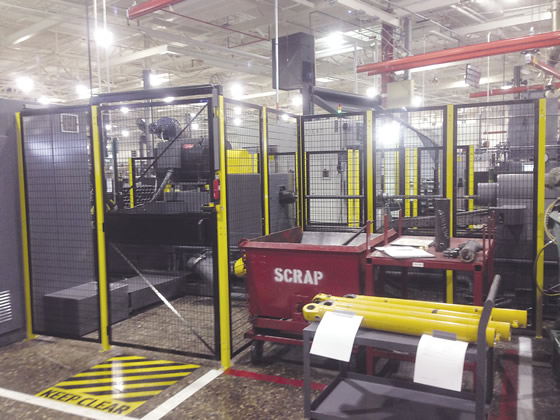
Folding Guard’s Saf-T-Fence machine guarding is used for a rod friction welder at the John Deere Internal Cylinder Div.’s plant, Moline, Ill.
“There are some very basic rules every shop should live by, and, typically, if you keep those in mind, you should be fine,” he said. “Mesh needs to be tight enough that you can’t fit your fingers through the opening, for example, and the distance between the equipment and the sweep space needs to be kept in mind. However, we need to see the shop in person in order to help bring things up to code, because there are plenty of hazards and deficiencies that might not come up unless you’re there to see it—lots of little codes and regulations that tend to go unnoticed.”
Folding Guard offers basic consulting services to customers, including a site visit to help shops bring practices and equipment up to code, as well as CAD-designed safety systems tailored to a shop’s specific machines. However, this may not be necessary, depending on the equipment.
“When we buy equipment, we generally buy newer technology, which typically comes with adequate safeguards included,” Jennings said. “We normally don’t have to add third-party safety equipment because we upgrade our machinery enough that it stays up to code. Our concern is with the people, making sure they’re doing things properly and following our safety procedures.” CTE
About the Author: Evan Jones Thorne is assistant editor for CTE. Contact him at ejonesthorne@jwr.com or (847) 714-0182.
Contributors
Crow Corp.
(800) 642-2769
www.crowcorp.com
Folding Guard
(800) 622-2214
www.foldingguard.com
National Institute for Metalworking Skills Inc.
(703) 352-4971
www.nims-skills.org
Related Glossary Terms
- computer numerical control ( CNC)
computer numerical control ( CNC)
Microprocessor-based controller dedicated to a machine tool that permits the creation or modification of parts. Programmed numerical control activates the machine’s servos and spindle drives and controls the various machining operations. See DNC, direct numerical control; NC, numerical control.
- metalworking
metalworking
Any manufacturing process in which metal is processed or machined such that the workpiece is given a new shape. Broadly defined, the term includes processes such as design and layout, heat-treating, material handling and inspection.