Contact Details
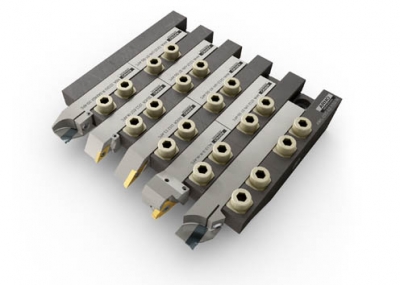
ARNO Werkzeuge offers its new AWL direct mount for Star Swiss-type machines. The toolholder system for turning or grooving tools (patent pending) has an integrated adjustable high-pressure coolant supply of up to 130 bar. When combined with the AFC quick-change system, users can increase productivity for Swiss-type machines because the system significantly cuts setup and non-productive times.
“After Citizen, our new AWL direct mount are now available for CNC Swiss type machines from Star Micronics,” says Werner Meditz, head of technology at ARNO Werkzeuge. The AWL toolholder system (patent pending) is available for the Star machine series SR 20R II, III and IV with immediate effect. The system has two separate cooling channels which can be selectively opened or closed. The various connection options make it adaptable to several machine types. Depending on the machine and execution, the new AWL direct mount can fit two to six tools. Each chamber has an integrated coolant supply to allow the simultaneous use of several tools, whether they have internal cooling or not.
Because the direct mount is designed with integrated cooling, it dispenses with the time-consuming connection of external and cost-intensive tubes. In addition, there are no interfering contours inside the machine. Users can operate with targeted high-pressure cooling pressures up to 130 bar and stable wedged clamping of holders during machining operations to achieve longer tool lives by over 25 percent, says ARNO.
It now takes only a few steps to remove and fit the tools. When turned, an integrated counter nut raises the wedge slightly to permit quick and easy tool removal and fitting. According to Meditz, “The tool system allows fast, simple tool changes with enormous change precision and high process reliability.” The direct mount can also hold the tools of other manufacturers. The freedom of tool choice is one of the greatest benefits of our AWL direct mount,” stresses Meditz, “since users are not forced to depend on only one system.”
“Users have the best benefits when they combine the AWL direct mount with the AFC quick-change system from ARNO,” assures Simon Storf, marketing manager. To change a tool, only the front part of the two-part holder needs to be removed and a new tool is then fitted with a different holder. This dispenses with the need for recalibration in many cases. The AWL direct mount and AFC quick-change system back the manufacturer’s claim of increasing productivity at user production locations by developing customised solutions.
Related Glossary Terms
- computer numerical control ( CNC)
computer numerical control ( CNC)
Microprocessor-based controller dedicated to a machine tool that permits the creation or modification of parts. Programmed numerical control activates the machine’s servos and spindle drives and controls the various machining operations. See DNC, direct numerical control; NC, numerical control.
- coolant
coolant
Fluid that reduces temperature buildup at the tool/workpiece interface during machining. Normally takes the form of a liquid such as soluble or chemical mixtures (semisynthetic, synthetic) but can be pressurized air or other gas. Because of water’s ability to absorb great quantities of heat, it is widely used as a coolant and vehicle for various cutting compounds, with the water-to-compound ratio varying with the machining task. See cutting fluid; semisynthetic cutting fluid; soluble-oil cutting fluid; synthetic cutting fluid.
- grooving
grooving
Machining grooves and shallow channels. Example: grooving ball-bearing raceways. Typically performed by tools that are capable of light cuts at high feed rates. Imparts high-quality finish.
- toolholder
toolholder
Secures a cutting tool during a machining operation. Basic types include block, cartridge, chuck, collet, fixed, modular, quick-change and rotating.
- turning
turning
Workpiece is held in a chuck, mounted on a face plate or secured between centers and rotated while a cutting tool, normally a single-point tool, is fed into it along its periphery or across its end or face. Takes the form of straight turning (cutting along the periphery of the workpiece); taper turning (creating a taper); step turning (turning different-size diameters on the same work); chamfering (beveling an edge or shoulder); facing (cutting on an end); turning threads (usually external but can be internal); roughing (high-volume metal removal); and finishing (final light cuts). Performed on lathes, turning centers, chucking machines, automatic screw machines and similar machines.