Contact Details
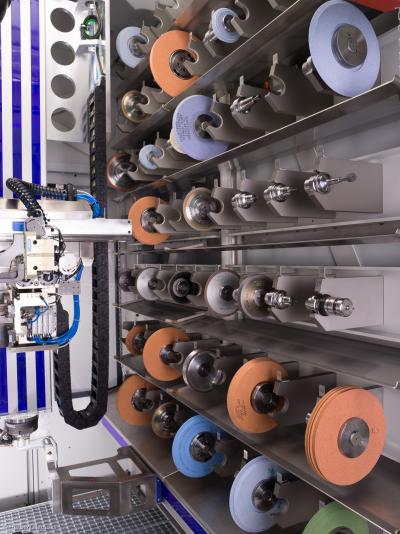
All Haas Multigrind grinding centers are available with an automatic wheel changer. This feature enables Haas customers to combine multiple, high-precision, complex grinding and milling operations into a single part clamping and single machine cycle. Users can realize significant improvements in overall part quality and significant reductions in overall throughput time and cost.
Now Haas customers can take another leap in productivity with the new high-capacity “shelf magazine.” On the Multigrind CB grinding machine, the new Haas shelf magazine (2,000 × 2,400 × 3,200 mm, L × W × H) offers space for 65 grinding wheels of up to 300 mm in diameter. On the Multigrind CA grinding machine, the shelf magazine can be equipped with up to 70 grinding wheels of up to 250 mm in diameter. The magazine can also hold up to 20 coolant nozzles.
The new high-capacity magazine enables customers to add more operations on a single part and to dramatically reduce change-over time between different parts by loading wheels and tools for multiple part numbers in the magazine, according to the company.
The Haas Horizon programming system maintains locations, dimensions and life information of all wheels and tools in the magazine in addition to programming the machine’s grinding and automation functions.
Even with much more wheel capacity, tool change time on the new shelf magazine is only 10 seconds.
"We’re not aware of any other tool magazine that offers as much space and flexibility,” said Dirk Wember, Haas Multigrind’s president.
Related Glossary Terms
- centers
centers
Cone-shaped pins that support a workpiece by one or two ends during machining. The centers fit into holes drilled in the workpiece ends. Centers that turn with the workpiece are called “live” centers; those that do not are called “dead” centers.
- coolant
coolant
Fluid that reduces temperature buildup at the tool/workpiece interface during machining. Normally takes the form of a liquid such as soluble or chemical mixtures (semisynthetic, synthetic) but can be pressurized air or other gas. Because of water’s ability to absorb great quantities of heat, it is widely used as a coolant and vehicle for various cutting compounds, with the water-to-compound ratio varying with the machining task. See cutting fluid; semisynthetic cutting fluid; soluble-oil cutting fluid; synthetic cutting fluid.
- gang cutting ( milling)
gang cutting ( milling)
Machining with several cutters mounted on a single arbor, generally for simultaneous cutting.
- grinding
grinding
Machining operation in which material is removed from the workpiece by a powered abrasive wheel, stone, belt, paste, sheet, compound, slurry, etc. Takes various forms: surface grinding (creates flat and/or squared surfaces); cylindrical grinding (for external cylindrical and tapered shapes, fillets, undercuts, etc.); centerless grinding; chamfering; thread and form grinding; tool and cutter grinding; offhand grinding; lapping and polishing (grinding with extremely fine grits to create ultrasmooth surfaces); honing; and disc grinding.
- grinding machine
grinding machine
Powers a grinding wheel or other abrasive tool for the purpose of removing metal and finishing workpieces to close tolerances. Provides smooth, square, parallel and accurate workpiece surfaces. When ultrasmooth surfaces and finishes on the order of microns are required, lapping and honing machines (precision grinders that run abrasives with extremely fine, uniform grits) are used. In its “finishing” role, the grinder is perhaps the most widely used machine tool. Various styles are available: bench and pedestal grinders for sharpening lathe bits and drills; surface grinders for producing square, parallel, smooth and accurate parts; cylindrical and centerless grinders; center-hole grinders; form grinders; facemill and endmill grinders; gear-cutting grinders; jig grinders; abrasive belt (backstand, swing-frame, belt-roll) grinders; tool and cutter grinders for sharpening and resharpening cutting tools; carbide grinders; hand-held die grinders; and abrasive cutoff saws.
- milling
milling
Machining operation in which metal or other material is removed by applying power to a rotating cutter. In vertical milling, the cutting tool is mounted vertically on the spindle. In horizontal milling, the cutting tool is mounted horizontally, either directly on the spindle or on an arbor. Horizontal milling is further broken down into conventional milling, where the cutter rotates opposite the direction of feed, or “up” into the workpiece; and climb milling, where the cutter rotates in the direction of feed, or “down” into the workpiece. Milling operations include plane or surface milling, endmilling, facemilling, angle milling, form milling and profiling.