Contact Details
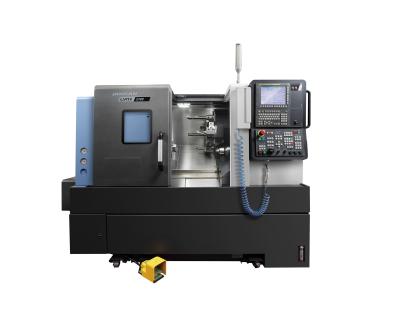
Doosan Machine Tools America introduced its latest generation “Lynx 2100” series of turning centers that evolved from its popular Lynx 220 series. An “M” version in the series offers milling capabilities offering the convenience, accuracy and productivity that one setup machining provides.
“It’s a robust, compact package of power ideal for machining valves, shafts, gears, flanges, housings, bolts and other metal parts up to a maximum turning diameter of 350 mm (13.8 in.) and length of 550 mm (21.7 in.),” said Shane Richards – product support manager, turning centers.
The Lynx 2100 series includes a wide support structure for X and Z axes and tailstock traverse. The X and Z axes are fitted with rigid roller-type guideways. The Lynx 2100’s 15kW (20 hp) motor provides ample power for turning outer and inner surfaces and Udrilling. The high power/high torque 6,000 rpm turning spindle (with 6-inch chuck) 169 Nm (8-inch chuck) (124.7 ft.-lbs.) motor supports high precision and heavy-duty cutting. The subspindle function, also 6000 rpm, enables back-end machining of the workpiece. Full C-axis 0.001-degree control is included to optimize the capabilities of the machine.
The M model is fitted with Doosan’s BMT 45P 12-station turret to provide superior performance for milling operations. The turret uses an air/oil cooling system to minimize negative thermal effects.
Other compelling standard features include a work setting function with automatic measurement for easier and more accurate setup, a CNC tailstock operable by a single press of a button, and a tool monitoring function that provides helpful information about tool change times. Further, an alarm guidance function notifies the operator if there are any errors during operation – their cause and even the corrective action to take. The machine is under the control of the newly designed DOOSAN-FANUC I with a 10.4-inch display.
Any of the Lynx 2100 series turning center models can be equipped with several options including such peripheral equipment as a chip conveyor, bar feeder, parts catcher, tool setter, oil skimmer and grease lubrication system among others.
Related Glossary Terms
- centers
centers
Cone-shaped pins that support a workpiece by one or two ends during machining. The centers fit into holes drilled in the workpiece ends. Centers that turn with the workpiece are called “live” centers; those that do not are called “dead” centers.
- computer numerical control ( CNC)
computer numerical control ( CNC)
Microprocessor-based controller dedicated to a machine tool that permits the creation or modification of parts. Programmed numerical control activates the machine’s servos and spindle drives and controls the various machining operations. See DNC, direct numerical control; NC, numerical control.
- gang cutting ( milling)
gang cutting ( milling)
Machining with several cutters mounted on a single arbor, generally for simultaneous cutting.
- milling
milling
Machining operation in which metal or other material is removed by applying power to a rotating cutter. In vertical milling, the cutting tool is mounted vertically on the spindle. In horizontal milling, the cutting tool is mounted horizontally, either directly on the spindle or on an arbor. Horizontal milling is further broken down into conventional milling, where the cutter rotates opposite the direction of feed, or “up” into the workpiece; and climb milling, where the cutter rotates in the direction of feed, or “down” into the workpiece. Milling operations include plane or surface milling, endmilling, facemilling, angle milling, form milling and profiling.
- turning
turning
Workpiece is held in a chuck, mounted on a face plate or secured between centers and rotated while a cutting tool, normally a single-point tool, is fed into it along its periphery or across its end or face. Takes the form of straight turning (cutting along the periphery of the workpiece); taper turning (creating a taper); step turning (turning different-size diameters on the same work); chamfering (beveling an edge or shoulder); facing (cutting on an end); turning threads (usually external but can be internal); roughing (high-volume metal removal); and finishing (final light cuts). Performed on lathes, turning centers, chucking machines, automatic screw machines and similar machines.