Contact Details
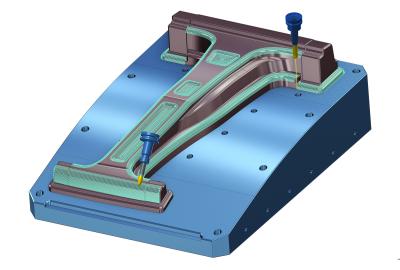
Mastercam 2019 Mill offers expanded machining flexibility and an increased emphasis on speed and automation. 2D high-speed toolpaths, 3D enhancements and multiaxis features combine with dozens of additional new enhancements in a software package intended to improve shop floor productivity.
Here are some of the most significant highlights and new functionality in Mastercam Mill:
A new toolpath, Model Chamfer, is now available for 2D machining. This toolpath allows you to machine safe horizontal chamfers on solid models. After selecting your geometry, Model Chamfer has several unique parameters to further control the toolpath.
Maintain sharp corners is now available for standard 2D Contour and Pocket toolpaths. This new option allows you to roll the toolpath around sharp corners and is available when you enter a positive value for stock to leave on walls.
A new 3D high-speed toolpath, Equal Scallop, creates a consistent scallop motion relative to stepover distance and produces a superior surface finish. Equal Scallop generates clean, noise-free motion with the ability to smooth out sharp corners or convert the motion to a spiral approach while avoiding stepover moves.
The linking process time for Area Roughing toolpaths has been improved, specifically for parts with many pockets and small stepdowns. This improves the overall processing time for high speed machining applications that use high-feed endmills.
Projected boundary smoothing tolerance has been added for Hybrid and Equal Scallop toolpaths. When you project a containment boundary onto the machining model, the resulting projected boundary can be jagged or noisy, especially near steep features. Use this option to allow Mastercam to improve the quality of the projected boundary.
A new toolpath, Deburr, can be used to break edges for 3- to 5-axis, and to remove burrs. Deburr can be used with the ball endmill and the lollipop with undercut tools.
Morph and Parallel toolpaths now support a gradual front shift, which keeps the tool in better contact with the part, without placing excess wear on the tool’s leading and trailing edges. Without it, the tool cuts across the part with the tool’s edge.
Curve, Swarf, Flow, Multisurface, Port and Rotary toolpaths are now multithreaded. This allows Mastercam to operate while the toolpaths generate and allows for speed improvements in multiple and offset cut calculations.
Other powerful tools in Mastercam 2019 Mill include:
- Check an operation’s tool holder for interference with the part with Check Holder enhancements.
- Accelerated Finishing technology has two new tool types, Lens Form and Taper Form.
- Skip Pocket Smaller Than is a new parameter that allows you to skip pockets based on the tool diameter percent, rather than by entering a dedicated size of the pocket.
- New Point Selection Workflow
- Transitions Feed Rate allows you to set which feed rate is used during transition moves for Waterline toolpaths.
Related Glossary Terms
- endmill
endmill
Milling cutter held by its shank that cuts on its periphery and, if so configured, on its free end. Takes a variety of shapes (single- and double-end, roughing, ballnose and cup-end) and sizes (stub, medium, long and extra-long). Also comes with differing numbers of flutes.
- feed
feed
Rate of change of position of the tool as a whole, relative to the workpiece while cutting.
- milling machine ( mill)
milling machine ( mill)
Runs endmills and arbor-mounted milling cutters. Features include a head with a spindle that drives the cutters; a column, knee and table that provide motion in the three Cartesian axes; and a base that supports the components and houses the cutting-fluid pump and reservoir. The work is mounted on the table and fed into the rotating cutter or endmill to accomplish the milling steps; vertical milling machines also feed endmills into the work by means of a spindle-mounted quill. Models range from small manual machines to big bed-type and duplex mills. All take one of three basic forms: vertical, horizontal or convertible horizontal/vertical. Vertical machines may be knee-type (the table is mounted on a knee that can be elevated) or bed-type (the table is securely supported and only moves horizontally). In general, horizontal machines are bigger and more powerful, while vertical machines are lighter but more versatile and easier to set up and operate.
- parallel
parallel
Strip or block of precision-ground stock used to elevate a workpiece, while keeping it parallel to the worktable, to prevent cutter/table contact.
- swarf
swarf
Metal fines and grinding wheel particles generated during grinding.
- tolerance
tolerance
Minimum and maximum amount a workpiece dimension is allowed to vary from a set standard and still be acceptable.
- toolpath( cutter path)
toolpath( cutter path)
2-D or 3-D path generated by program code or a CAM system and followed by tool when machining a part.
- undercut
undercut
In numerical-control applications, a cut shorter than the programmed cut resulting after a command change in direction. Also a condition in generated gear teeth when any part of the fillet curve lies inside of a line drawn tangent to the working profile at its point of juncture with the fillet. Undercut may be deliberately introduced to facilitate finishing operations, as in preshaving.