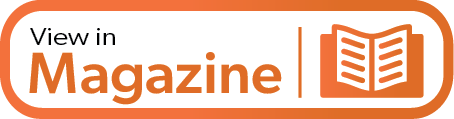
In partnership with CAMufacturing Solutions Inc. in Windsor, Ontario, Mastercam in Tolland, Connecticut, offers the APlus Add-On for additive manufacturing for use with the CAD/CAM software developer’s Mastercam Mill, Mastercam Lathe or Mastercam Router licenses — except for Entry. Using the same Mastercam interface, APlus customers can reportedly program, backplot and post process like they would with traditional toolpaths.
APlus supports directed energy deposition and has toolpaths developed specifically to handle any AM geometry. “APlus brings additive manufacturing to the Mastercam user in a form that is consistent with the workflow used for over 40 years,” said Mastercam Technical Product Manager Kenneth Fortier. “Direct energy deposition is making its way into many machine shops, and being able to program hybrid machines or dedicated additive manufacturing machines using Mastercam makes the transition seamless. With the hybrid process of alternating adding material and milling allows parts with internally machined features to be created that would have been impossible without additive.”
Using APlus, for example, is appropriate when repairing a blade where the tips are showing wear. To repair the part, the user machines away the worn tips using a suitable toolpath in Mastercam. With APlus, a user can deposit material onto the machined surfaces to a near-net shape before machining the 3D-printed sections to the desired specifications. This process can dramatically lower costs compared to buying or machining a new blade, or even stocking spare parts.
For more information, visit www.mastercam.com .
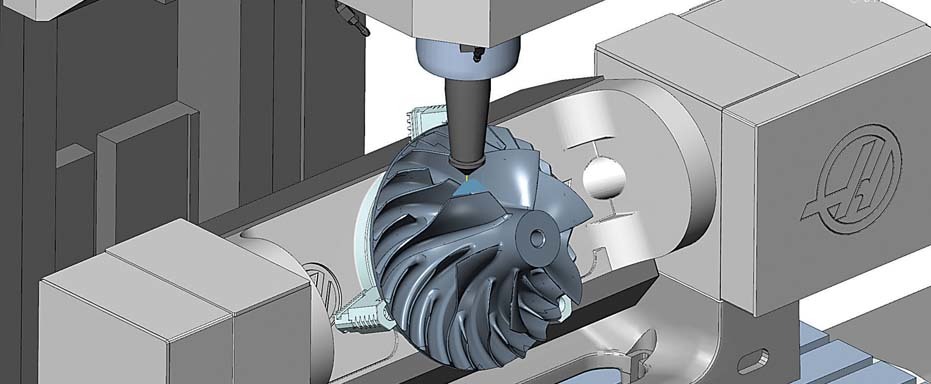
Related Glossary Terms
- gang cutting ( milling)
gang cutting ( milling)
Machining with several cutters mounted on a single arbor, generally for simultaneous cutting.
- lathe
lathe
Turning machine capable of sawing, milling, grinding, gear-cutting, drilling, reaming, boring, threading, facing, chamfering, grooving, knurling, spinning, parting, necking, taper-cutting, and cam- and eccentric-cutting, as well as step- and straight-turning. Comes in a variety of forms, ranging from manual to semiautomatic to fully automatic, with major types being engine lathes, turning and contouring lathes, turret lathes and numerical-control lathes. The engine lathe consists of a headstock and spindle, tailstock, bed, carriage (complete with apron) and cross slides. Features include gear- (speed) and feed-selector levers, toolpost, compound rest, lead screw and reversing lead screw, threading dial and rapid-traverse lever. Special lathe types include through-the-spindle, camshaft and crankshaft, brake drum and rotor, spinning and gun-barrel machines. Toolroom and bench lathes are used for precision work; the former for tool-and-die work and similar tasks, the latter for small workpieces (instruments, watches), normally without a power feed. Models are typically designated according to their “swing,” or the largest-diameter workpiece that can be rotated; bed length, or the distance between centers; and horsepower generated. See turning machine.
- milling
milling
Machining operation in which metal or other material is removed by applying power to a rotating cutter. In vertical milling, the cutting tool is mounted vertically on the spindle. In horizontal milling, the cutting tool is mounted horizontally, either directly on the spindle or on an arbor. Horizontal milling is further broken down into conventional milling, where the cutter rotates opposite the direction of feed, or “up” into the workpiece; and climb milling, where the cutter rotates in the direction of feed, or “down” into the workpiece. Milling operations include plane or surface milling, endmilling, facemilling, angle milling, form milling and profiling.
- milling machine ( mill)
milling machine ( mill)
Runs endmills and arbor-mounted milling cutters. Features include a head with a spindle that drives the cutters; a column, knee and table that provide motion in the three Cartesian axes; and a base that supports the components and houses the cutting-fluid pump and reservoir. The work is mounted on the table and fed into the rotating cutter or endmill to accomplish the milling steps; vertical milling machines also feed endmills into the work by means of a spindle-mounted quill. Models range from small manual machines to big bed-type and duplex mills. All take one of three basic forms: vertical, horizontal or convertible horizontal/vertical. Vertical machines may be knee-type (the table is mounted on a knee that can be elevated) or bed-type (the table is securely supported and only moves horizontally). In general, horizontal machines are bigger and more powerful, while vertical machines are lighter but more versatile and easier to set up and operate.
- toolpath( cutter path)
toolpath( cutter path)
2-D or 3-D path generated by program code or a CAM system and followed by tool when machining a part.