Founded in 2013 and based in Kecskemét, Hungary, family-owned BS CNC Workshop Kft produces precision metal components in its 900-sq.-m (9,688 sq. ft.) high-mix, low-volume production facility. The manufacturer operates three CNC lathes, four CNC milling machines and a conventional slab grinder. The company has grown steadily to become a supplier to several large multinational companies.
In 2020, BS CNC upgraded its quality assurance department by installing a measuring room that adheres to current standards. The temperature-controlled environment houses a coordinate measuring machine, a linear height gauge, a surface roughness gauge and an optical measuring machine.
BS CNC reports that it employs highly experienced personnel who specialize in CNC machining, locksmithing, programming and quality assurance. Machine tending is a time-consuming task for those valued employees, however, and the repetitive and monotonous nature of the task makes it difficult to hire and keep skilled operators.
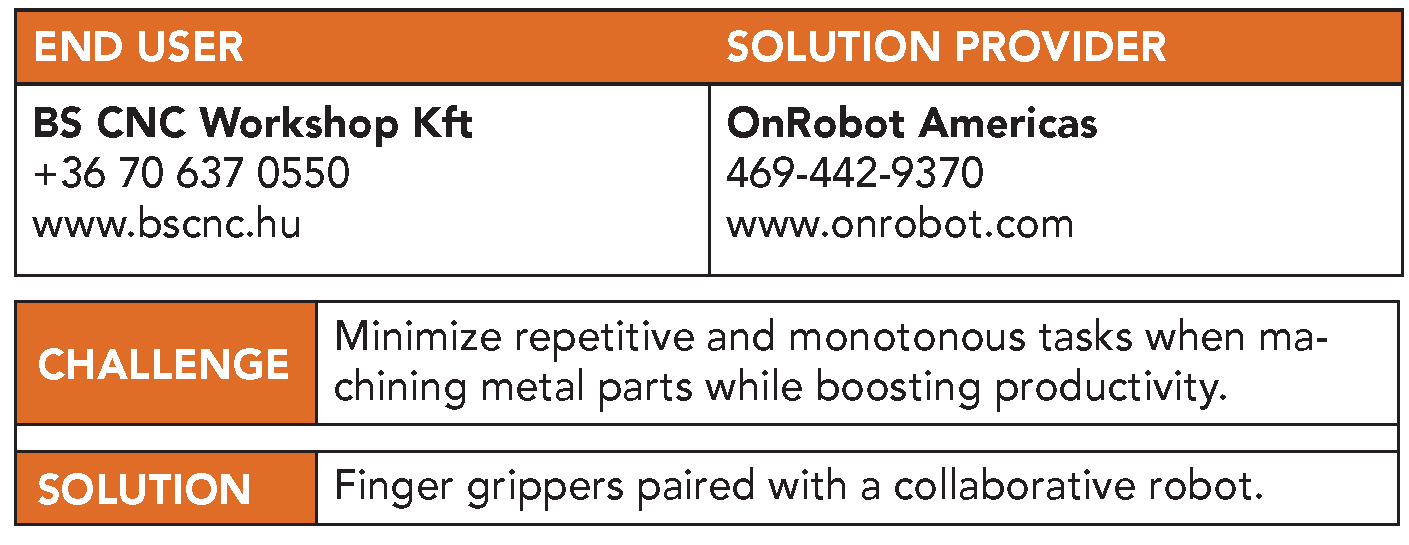
Barabás Sándor, managing director and owner of BS CNC, said, “We knew that robotic automation could solve our challenges, but we were unsure if it was feasible to invest in automation due to the nature of our production.”
BS CNC turned to Wamatec Hungary Kft, a system integrator that works closely with OnRobot to automate CNC machine tending. OnRobot provides tools and software for collaborative robot applications. (OnRobot Americas is in Irving, Texas.) Key to the solution was OnRobot’s broad portfolio of flexible and intelligent electric grippers that can easily adapt to handle a range of different parts.
“After a proof of concept, we realized automating our high-mix, low-volume production was not a problem and that it would make financial sense,” Sándor said.
BS CNC selected two OnRobot 2FG7 electric finger grippers with the Dual Quick Changer paired with a collaborative robot from Doosan Robotics Inc. OnRobot’s seamless integration with the Doosan cobot allowed the team to quickly get the system up and running using the familiar Doosan robot teach pendant interface
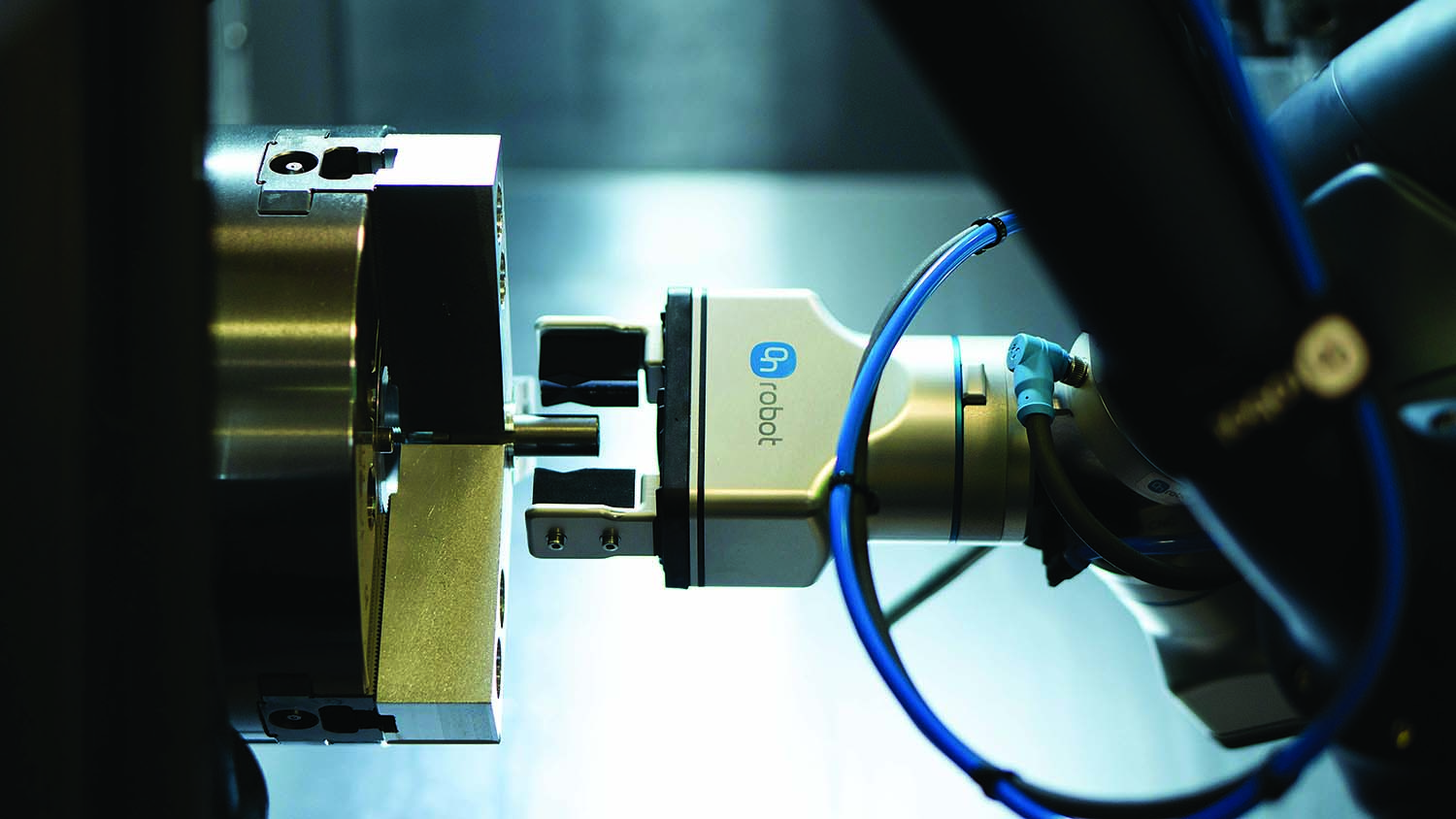
Unlike custom grippers, the 2FG7 parallel finger gripper is reportedly easy to set up and run, handling the variety of parts needed and requiring no additional engineering or maintenance that would otherwise drive up costs. The gripper is well-suited for machine tending tasks because of its compact design and reliability in challenging manufacturing conditions where equipment is exposed to splashing water, oil and coolant. BS CNC boosted productivity by mounting two grippers in the Dual Quick Changer, allowing the robot to load and unload parts in one pass.
Before automating, the company typically produced 128 parts per shift. That increased to 155 parts per shift, for a 21% productivity improvement, Sándor said. “With the new solution, we have assured our CNC machines are always operational, enabling us to enhance our production hours by four.”
Like many relatively small companies, BS CNC is able to realize the advantages of robotic automation that was previously only affordable for much larger manufacturers. The flexible, affordable OnRobot tools and Doosan collaborative robot have improved BS CNC’s competitiveness, according to the parts manufacturer.
The company can now run its machine tending processes at full capacity for increased productivity, while freeing employees to do more valuable and interesting tasks. This also makes it easier to retain skilled employees. In addition, the flexible automation solution helps the company quickly respond to production changes without compromising on quality.
“Automating our CNC machine tending resulted in a 50% decrease of downtime,” Sándor added.
Contact Details
Related Glossary Terms
- computer numerical control ( CNC)
computer numerical control ( CNC)
Microprocessor-based controller dedicated to a machine tool that permits the creation or modification of parts. Programmed numerical control activates the machine’s servos and spindle drives and controls the various machining operations. See DNC, direct numerical control; NC, numerical control.
- coolant
coolant
Fluid that reduces temperature buildup at the tool/workpiece interface during machining. Normally takes the form of a liquid such as soluble or chemical mixtures (semisynthetic, synthetic) but can be pressurized air or other gas. Because of water’s ability to absorb great quantities of heat, it is widely used as a coolant and vehicle for various cutting compounds, with the water-to-compound ratio varying with the machining task. See cutting fluid; semisynthetic cutting fluid; soluble-oil cutting fluid; synthetic cutting fluid.
- gang cutting ( milling)
gang cutting ( milling)
Machining with several cutters mounted on a single arbor, generally for simultaneous cutting.
- milling
milling
Machining operation in which metal or other material is removed by applying power to a rotating cutter. In vertical milling, the cutting tool is mounted vertically on the spindle. In horizontal milling, the cutting tool is mounted horizontally, either directly on the spindle or on an arbor. Horizontal milling is further broken down into conventional milling, where the cutter rotates opposite the direction of feed, or “up” into the workpiece; and climb milling, where the cutter rotates in the direction of feed, or “down” into the workpiece. Milling operations include plane or surface milling, endmilling, facemilling, angle milling, form milling and profiling.
- parallel
parallel
Strip or block of precision-ground stock used to elevate a workpiece, while keeping it parallel to the worktable, to prevent cutter/table contact.
- quality assurance ( quality control)
quality assurance ( quality control)
Terms denoting a formal program for monitoring product quality. The denotations are the same, but QC typically connotes a more traditional postmachining inspection system, while QA implies a more comprehensive approach, with emphasis on “total quality,” broad quality principles, statistical process control and other statistical methods.
- robotics
robotics
Discipline involving self-actuating and self-operating devices. Robots frequently imitate human capabilities, including the ability to manipulate physical objects while evaluating and reacting appropriately to various stimuli. See industrial robot; robot.