Offering what the manufacturer touts as a tempting menu of attractions at a budget-friendly price, a recently introduced CNC mill is designed to appeal to both commercial enterprises and machining enthusiasts working in their garage.
A three-axis, servo-driven mill on linear rails, the new 1500MX is “by far the fastest, most accurate and most powerful machine we’ve ever made,” noted Daniel Rogge, CEO of Tormach Inc. in Madison, Wisconsin. Its capabilities, along with ease of use, make the 1500MX a good choice for both prototyping and production, according to the company.
Offering cutting feed rates of up to 1,200 ipm (XY), the machine is equipped with a 10,000 rpm BT30 spindle (maximum 6 hp) that provides enough torque to cut through a variety of materials and sufficient speed to make good use of modern carbide tooling. In addition, Tormach reports that the 1500MX facilitates integration of through-spindle coolant for improved drilling efficiency, smoother finishes, more consistent parts and longer tool life.
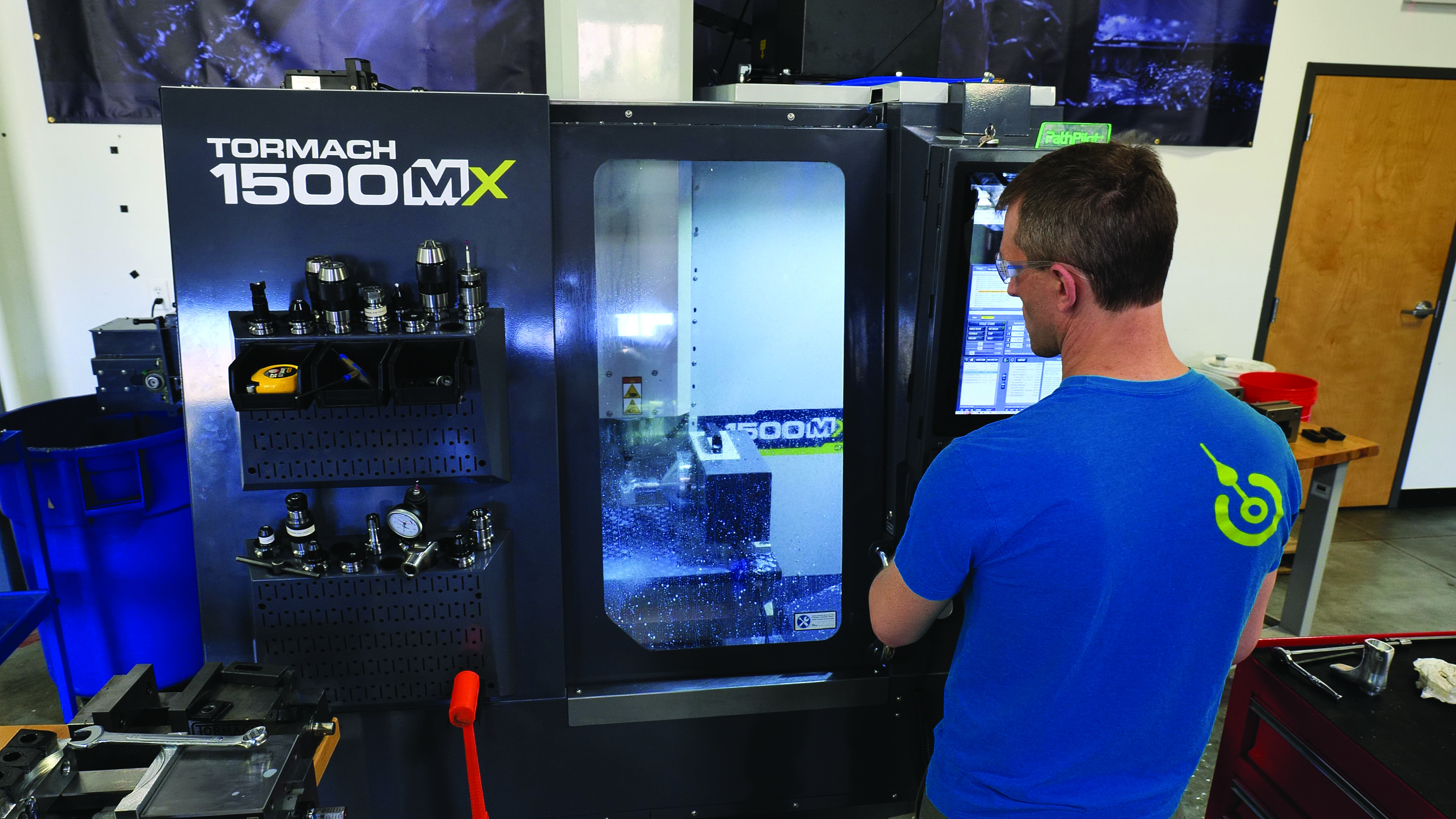
For motion, the 1500MX relies on servo motors with absolute encoders featuring 23-bit accuracy and battery backup to eliminate the need for machine referencing. “While the machine is shut down, a battery keeps the encoder powered up so the machine always knows where it is,” Rogge explained.
One of the main attractions of the 1500MX is its epoxy granite frame, a first for a Tormach machine. According to Rogge, epoxy granite provides about seven times the damping of traditional cast iron, which can increase tool life by 30% to 50%. “You also get a great surface finish with that technology,” he added, as well as much better thermal stability than that provided by cast iron frames.
Like all Tormach machines, the 1500MX runs on the company’s free and open-source PathPilot control software. Additional free features include access to advanced machining functions and software updates for life, as well as 80 GB of memory.
“If you buy a machine tool from one of our competitors, they charge you extra for things like rigid tapping and high-speed machining,” Rogge said. “Some of them even charge extra for program memory. (Maybe) the machine came with a hard drive that has 80 GB, but they’re only going to offer you 1 GB of storage unless you pay them extra. When you buy our machine, we don't upcharge anything. And as we develop new features, we roll those out to our existing customers for free.”
Recent updates to PathPilot include the addition of tool wear compensation and improvements to the trajectory planner to incorporate machine smoothing.
Other 1500MX features include tool rack options, a built-in camera for real-time monitoring, and error-message logs for troubleshooting.
Upgrade options include a 16-tool capacity umbrella-style automatic tool changer, a fourth-axis harmonic gear reducer, a wireless probe and tool setter, and a chip conveyor system with lift. In addition, the machine can be paired with Tormach’s industrial robot, the ZA6, for automation of light part machining.
Selling for a base price of $31,995, the 1500MX offers features and capabilities that normally come at a much higher cost, according to Tormach. For example, the epoxy granite frame “is typically something found in much higher-end machine tools,” Rogge said. “There are a couple other folks out there offering that in this size range [but] at much higher prices”—probably 50% to 100% more.
Asked how his company can sell machines at much lower prices than competitive offerings, Rogge pointed to several factors, including supply chain engineering and the fact that Tormach produces its own control software. In addition, he noted that Tormach doesn’t rely on a traditional distribution model.
“We’re an e-commerce company,” he said. “When you buy a product from us, you're going to our website, adding it to the cart and checking it out just like an Amazon purchase. We don't have a factory outlet or authorized distribution network that's taking a 20% to 30% cut off the top. And we're passing that savings along to the customer.”
Related Glossary Terms
- computer numerical control ( CNC)
computer numerical control ( CNC)
Microprocessor-based controller dedicated to a machine tool that permits the creation or modification of parts. Programmed numerical control activates the machine’s servos and spindle drives and controls the various machining operations. See DNC, direct numerical control; NC, numerical control.
- coolant
coolant
Fluid that reduces temperature buildup at the tool/workpiece interface during machining. Normally takes the form of a liquid such as soluble or chemical mixtures (semisynthetic, synthetic) but can be pressurized air or other gas. Because of water’s ability to absorb great quantities of heat, it is widely used as a coolant and vehicle for various cutting compounds, with the water-to-compound ratio varying with the machining task. See cutting fluid; semisynthetic cutting fluid; soluble-oil cutting fluid; synthetic cutting fluid.
- feed
feed
Rate of change of position of the tool as a whole, relative to the workpiece while cutting.
- inches per minute ( ipm)
inches per minute ( ipm)
Value that refers to how far the workpiece or cutter advances linearly in 1 minute, defined as: ipm = ipt 5 number of effective teeth 5 rpm. Also known as the table feed or machine feed.
- industrial robot
industrial robot
Robot designed for industrial use. Primarily used as a material-handling device but also used for changing tools, assembling parts, and manipulating special tools and measuring devices. Depending on design, an industrial robot can be programmed to perform a task by means of a controller, or it can be “walked” through the required movements by utilizing a digitizing system that translates movements into commands that the robot can be “taught.” See robot; teaching pendant.
- milling machine ( mill)
milling machine ( mill)
Runs endmills and arbor-mounted milling cutters. Features include a head with a spindle that drives the cutters; a column, knee and table that provide motion in the three Cartesian axes; and a base that supports the components and houses the cutting-fluid pump and reservoir. The work is mounted on the table and fed into the rotating cutter or endmill to accomplish the milling steps; vertical milling machines also feed endmills into the work by means of a spindle-mounted quill. Models range from small manual machines to big bed-type and duplex mills. All take one of three basic forms: vertical, horizontal or convertible horizontal/vertical. Vertical machines may be knee-type (the table is mounted on a knee that can be elevated) or bed-type (the table is securely supported and only moves horizontally). In general, horizontal machines are bigger and more powerful, while vertical machines are lighter but more versatile and easier to set up and operate.
- tapping
tapping
Machining operation in which a tap, with teeth on its periphery, cuts internal threads in a predrilled hole having a smaller diameter than the tap diameter. Threads are formed by a combined rotary and axial-relative motion between tap and workpiece. See tap.