Like the substance itself, developing new synthetic diamond supermaterials is extremely hard. When reviewing its new product development performance a few years ago, Element Six determined it wasn’t effective and efficient enough and the company needed to increase its innovation performance, according to Steve Coe, executive director of group innovation for Element Six.
To do so, the synthetic diamond manufacturer consolidated its four R&D centers spread around the world and officially opened the 60,000-sq.-ft., $32 million Global Innovation Centre, Harwell, U.K., in early July. “The idea was that for a company of our size, we needed to consolidate into one center so we could have much better communication between our R&D teams and much better coordination of our activities,” Coe said, noting 114 people work at the GIC.
Coe added that the country’s strong science and engineering talent base enables Element Six to better attract the best and brightest workers, and being less than an hour from Heathrow Airport makes it more convenient for customers to visit and interact with the company’s scientists. “We do a lot of product development in collaboration with our customers,” he said. “It gives us the opportunity to better understand their needs and ultimately develop diamond products that better meet their requirements.”
In addition to being used to make PCD, PCBN and single-crystal diamond tools and abrasive products, Element Six’s products are found in a multitude of applications. Recent examples include a diamond road pick that lasts 40 times longer than a conventional road pick, sensors in the Large Hadron Collider particle accelerator and tweeter domes for Bower & Wilkins 800 Series Diamond loudspeakers.
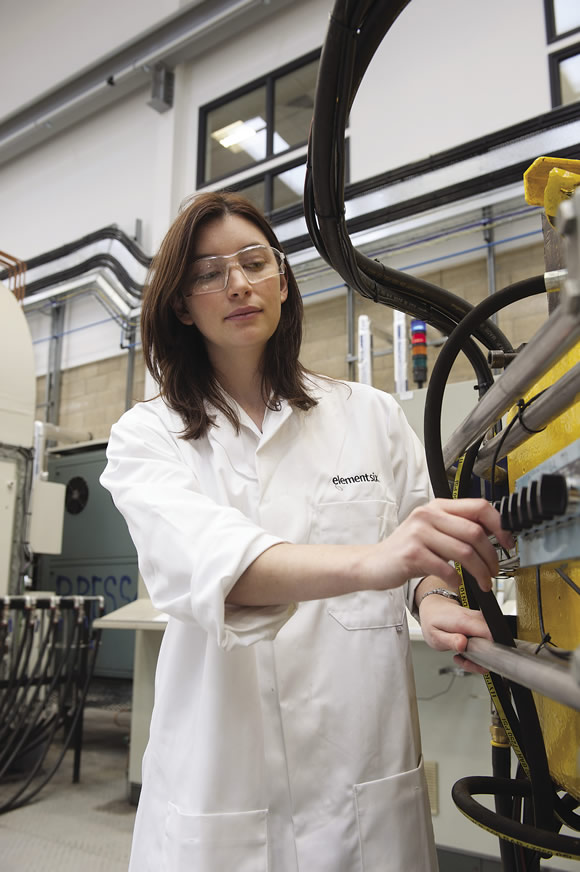
An Element Six scientist uses a high-pressure, high-temperature press at the company’s Global Innovation Centre to create synthetic diamond.
Facilities at the center include ones for modeling and design, materials preparation, materials analysis/characterization and post-synthesis processing, such as polishing, cutting and shaping. The GIC also houses high-pressure, high-temperature synthesis presses and chemical vapor deposition reactor synthesis labs.
“We also do all of our application testing on-site,” Coe said. “We can take the diamond we make into cutting tools and test it in real-life applications. So we design, do R&D, make prototypes and test them all under one roof, with the driver being that we could use that capability to accelerate the development process.”
The mechanical presses are about the size of a three-story building and produce the temperatures and pressures needed to convert graphite into diamond. According to Element Six, the presses create the equivalent conditions of the Eiffel Tower turned upside down on a soda can. “We are creating pressures on the order of 6 to 8 GPa,” Coe said.
The company typically invests more than 7 percent of its revenue in R&D, according to Coe. “That’s a fairly high investment. Innovation is really at the core of Element Six.”
For more information about Luxembourg-headquartered Element Six, visit www.e6.com.
Related Glossary Terms
- abrasive
abrasive
Substance used for grinding, honing, lapping, superfinishing and polishing. Examples include garnet, emery, corundum, silicon carbide, cubic boron nitride and diamond in various grit sizes.
- centers
centers
Cone-shaped pins that support a workpiece by one or two ends during machining. The centers fit into holes drilled in the workpiece ends. Centers that turn with the workpiece are called “live” centers; those that do not are called “dead” centers.
- chemical vapor deposition ( CVD)
chemical vapor deposition ( CVD)
High-temperature (1,000° C or higher), atmosphere-controlled process in which a chemical reaction is induced for the purpose of depositing a coating 2µm to 12µm thick on a tool’s surface. See coated tools; PVD, physical vapor deposition.
- polishing
polishing
Abrasive process that improves surface finish and blends contours. Abrasive particles attached to a flexible backing abrade the workpiece.
- polycrystalline cubic boron nitride ( PCBN)
polycrystalline cubic boron nitride ( PCBN)
Cutting tool material consisting of polycrystalline cubic boron nitride with a metallic or ceramic binder. PCBN is available either as a tip brazed to a carbide insert carrier or as a solid insert. Primarily used for cutting hardened ferrous alloys.
- polycrystalline diamond ( PCD)
polycrystalline diamond ( PCD)
Cutting tool material consisting of natural or synthetic diamond crystals bonded together under high pressure at elevated temperatures. PCD is available as a tip brazed to a carbide insert carrier. Used for machining nonferrous alloys and nonmetallic materials at high cutting speeds.
- shaping
shaping
Using a shaper primarily to produce flat surfaces in horizontal, vertical or angular planes. It can also include the machining of curved surfaces, helixes, serrations and special work involving odd and irregular shapes. Often used for prototype or short-run manufacturing to eliminate the need for expensive special tooling or processes.
- single-crystal diamond
single-crystal diamond
Industrial-grade, natural diamond. Not recommended for cutting ferrous materials because it tends to react chemically with them and break down. Also not recommended for interrupted cuts in hard materials. Replaced by polycrystalline diamond in many applications. See diamond; PCD, polycrystalline diamond; superabrasive tools.