Metalworking is becoming increasingly specialized, with manufacturers of lathes and grinders offering a variety of capacities, bed lengths and other options. This promises the user the ability to create custom machining solutions to “meet any production need.” While this is true to a point, standard options have their limits, and truly customized machines cost more and have extended delivery times.
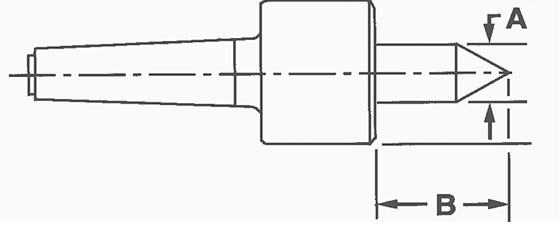
Figure 1. Live center modifications typically include point length (B) and diameter (A). All images courtesy Riten Industries.
However, the demand for unique production operations can frequently be satisfied by a simple custom-engineered workholding solution rather than an expensive dedicated machine. In my 26 years at Riten Industries, I’ve seen explosive growth in customer specials, which make up 40 percent of our sales.
It started years ago as a quote to provide extra tool clearance by changing the point length and diameter of a standard live center (Figure 1). Grinder operators also requested dead centers in nonstandard lengths and point diameters (Figure 2). This allowed grinding various part lengths, which saved setup time by eliminating the need to reposition the machine tailstock and recenter the machine. These types of requests led to the creation of a new production cell for specials. The relatively simple dimensional modifications to existing products were, for many years, the sole workload for the specials department.
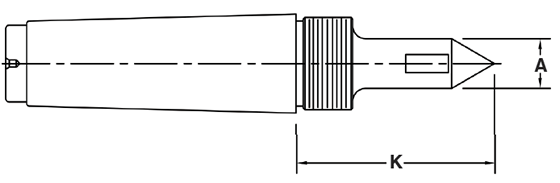
Figure 2. Nonstandard lengths (K) are a common request on dead centers for grinders.
As specialization increased, forward-thinking customers began to ask for quotes on one-of-a-kind workholding beyond the typical live and dead center modifications. As a result, the specials group had to add design engineering expertise to create affordable solutions that could be manufactured.
Although we had to “no quote” some customer ideas that were impossible to build with any guarantee of accuracy, durability or cost-efficiency, we did take on a number of challenges.
- A customer determined that a collet chuck would be the most efficient way to grind a batch of expensive parts for rework. A 3-jaw chuck would not deliver the required accuracy, and indicating a 4-jaw for each part would be too time-consuming. The problem with collet chucks was they could not be mounted on their machines. We designed an integrated collet chuck and Morse-taper live center with a modified spindle (Figure 3). This not only solved the installation problem, but also added process efficiency.
- Center holes on roll journals often take a beating when replacement bearings are installed, rendering the center hole unusable. Also, depending on the repair process, refurbished rolls can end up with journals that are misaligned with the center holes, making future repairs problematic. Machining a new center hole can be difficult and time-consuming. Several customers sought a solution. Our answer was a live chuck mandrel that combined the rotational accuracy of a live center with the flexibility of a 4-jaw chuck (Figure 4). The mandrel chucks on the bearing journals of the roll, bypassing the damaged center hole. Simple indication of the roll while adjusting the 4-jaw chuck brings the part back on centerline. Alternately, where the center hole is in good condition but no longer on center, the mandrel can chuck a dead center and dial in the part by adjusting the chuck jaws.
- A variety of specialized dead centers provide extra gripping force for unusual part geometries. These “drive centers” can have teeth or an abrasive coating to grip the part face, a spring-loaded point or custom pins that can engage keyways, splines, holes or other part features.
- Our most recent custom tool was designed for workpieces with center holes drilled slightly off center. This live center featured a radially adjustable point that locates in the center hole, centering the part by offsetting the deviation. The center is equipped with four external adjusting screws that can move the point up to 0.030" in any direction. The process is similar to indicating a part using a 4-jaw chuck. Like many former specials, our adjustable-point live center is now a semistandard catalog item.
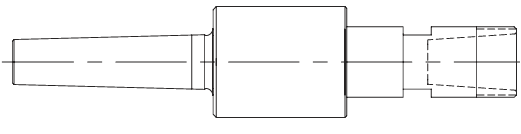
Figure 3. This ER 32 collet chuck/live center is a special.
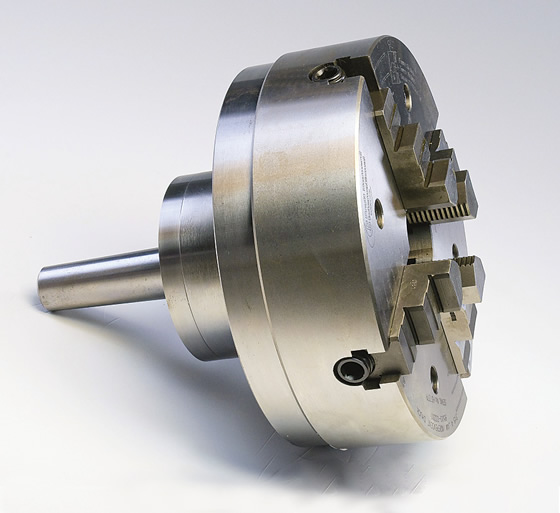
Figure 4. This live chuck mandrel can center rolls with damaged center holes.
There are also standard centers that need to be adapted to perform in unique, even hostile machining environments. Vacuums require special lubricants and high-performance seals. Heat generated by processes such as induction heat treating or plasma spray coating can be dealt with by modifying the center in several ways: a stainless steel spindle; special seals and lubricants; or active cooling mechanisms, including a water jacket or application of an air gun.
These examples illustrate the scope of customized workholding tools that have been produced to assist machinists seeking higher efficiencies or dealing with uncommon applications. We foresee no letup in demand for specials in the future. CTE
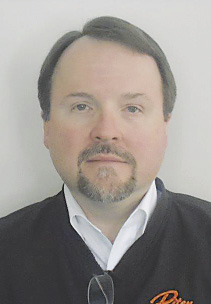
Related Glossary Terms
- abrasive
abrasive
Substance used for grinding, honing, lapping, superfinishing and polishing. Examples include garnet, emery, corundum, silicon carbide, cubic boron nitride and diamond in various grit sizes.
- centering
centering
1. Process of locating the center of a workpiece to be mounted on centers. 2. Process of mounting the workpiece concentric to the machine spindle. See centers.
- centers
centers
Cone-shaped pins that support a workpiece by one or two ends during machining. The centers fit into holes drilled in the workpiece ends. Centers that turn with the workpiece are called “live” centers; those that do not are called “dead” centers.
- chuck
chuck
Workholding device that affixes to a mill, lathe or drill-press spindle. It holds a tool or workpiece by one end, allowing it to be rotated. May also be fitted to the machine table to hold a workpiece. Two or more adjustable jaws actually hold the tool or part. May be actuated manually, pneumatically, hydraulically or electrically. See collet.
- clearance
clearance
Space provided behind a tool’s land or relief to prevent rubbing and subsequent premature deterioration of the tool. See land; relief.
- collet
collet
Flexible-sided device that secures a tool or workpiece. Similar in function to a chuck, but can accommodate only a narrow size range. Typically provides greater gripping force and precision than a chuck. See chuck.
- grinding
grinding
Machining operation in which material is removed from the workpiece by a powered abrasive wheel, stone, belt, paste, sheet, compound, slurry, etc. Takes various forms: surface grinding (creates flat and/or squared surfaces); cylindrical grinding (for external cylindrical and tapered shapes, fillets, undercuts, etc.); centerless grinding; chamfering; thread and form grinding; tool and cutter grinding; offhand grinding; lapping and polishing (grinding with extremely fine grits to create ultrasmooth surfaces); honing; and disc grinding.
- mandrel
mandrel
Workholder for turning that fits inside hollow workpieces. Types available include expanding, pin and threaded.
- metalworking
metalworking
Any manufacturing process in which metal is processed or machined such that the workpiece is given a new shape. Broadly defined, the term includes processes such as design and layout, heat-treating, material handling and inspection.
- payload ( workload)
payload ( workload)
Maximum load that the robot can handle safely.