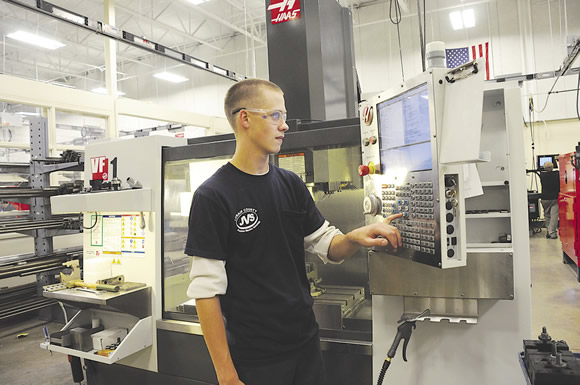
Courtesy of NIMS
A student at Lorain County Joint Vocational School’s NIMS-accredited Precision Machine Technology Program in Oberlin, Ohio, programs a CNC machine.
|
It’s no secret that thousands of skilled manufacturing jobs go unfilled due to a lack of qualified applicants. To combat this skills gap, the National Institute for Metalworking Skills Inc. (NIMS), Fairfax, Va., has spent most of the last 2 decades since its founding developing an extensive credentialing program. Also, through accredited training programs across the country, NIMS has pushed for the widespread adoption of national industry standards, as well as encouraging schools and manufacturers to dispel negative public perceptions of the metalworking industry.
NIMS was incorporated in 1995, and since then has issued more than 50,000 credentials to qualified machinists—more than 2,000 in 2013 alone, according to NIMS Executive Director James A. Wall—and those credentials are fast becoming the industry standard. By Wall’s estimate, of the approximately 1,600 publicly funded machining training programs in the country, more than half are issuing NIMS credentials, with roughly 20 percent being fully accredited.
“The U.S. Departments of Labor and Education are encouraging schools to use national industry standards as a performance measure,” Wall said, noting the nearly $1.5 billion disbursed through the Trade Adjustment Assistance Community College and Career Training program, put into place by the U.S. Department of Labor in 2010, have helped give schools discretionary funds to improve their programs. “We’re seeing a lot of movement [towards accreditation] as these large federal grants begin to move through,” he said.
The process for a training center to attain accredited status through NIMS isn’t quite the same as in other industries.
“We are a little different than some other organizations, where you have to be a certified [training] site before you can credential people,” Wall said. “We are just the opposite. You’ve got to train some people to pass their credentialing exams to prove you can [train effectively] before we will accredit your program.”
Once a training center has established a history of credentialing, the next step is submitting an application to receive a comprehensive self-study kit. Everything—from making sure the center’s curricula are aligned with national industry standards to checking the qualifications of the instructors to completing an overview of safety, health and welfare measures in the facility—must be documented, with points given at each step. If the organization successfully completes its self-study, three NIMS auditors are dispatched to complete a 2-day inspection.
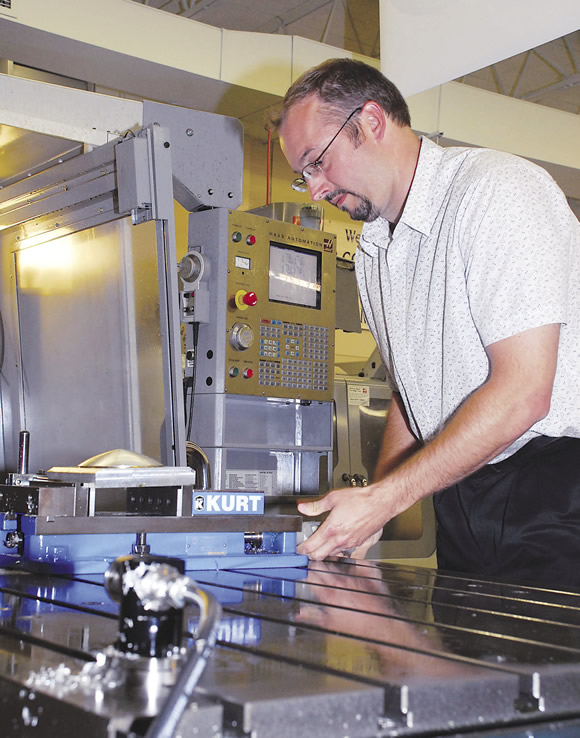
Courtesy of LCC
Lenoir Community College graduate Glen Stalknaker operates a Haas VR-8 5-axis machine.
“We’ll interview students, talk with the advisory committee and contact customers, as well as industry members, who have hired graduates of the program,” Wall said. Based on the results of the evaluation, the team makes a recommendation to either accredit or not accredit the program, though typically the recommendation is to provisionally accredit the program pending successful completion of action items.
Lenoir Community College, Kinston, N.C., successfully completed its accreditation process on July 29, 2013. According to Paul Hill, head of Lenoir’s computer-integrated machining program, it was the logical next step in what he sees as a growing national trend.
“In the past few years, NIMS has gained a lot of recognition at the national level,” he said. “At this point, I really feel like [NIMS accreditation] is going to be the future of the industry, and most schools that are teaching machining already have a lot of the necessary things in place to achieve that.”
Lenoir has also realized other benefits associated with running an accredited program. The credentialing examination requires an investment, but students receiving financial aid through Pell grants or the federal Workforce Investment Act can receive additional aid that offsets the cost of their certification. That’s important because Hill and his team are always looking to remove as many financial obstacles as possible for their students. However, money is not the only issue facing machinist training programs.
“You’re dealing with a generation of kids whose parents and grandparents worked in manufacturing,” Hill said. “When companies moved operations offshore in the late ’80s and ’90s, a lot of people [were fired from places they] had been working at for 20 years or more. That doesn’t leave people with a very good view of machining. A lot of those parents are pushing their kids toward 4-year college degrees.” But, he said, skilled and certified machinists can make more money initially than many graduates with 4-year degrees.
Money and Misconceptions
Changing the perception of machining will take time and money, according to Jimmy Hall, a career machinist with more than 2 decades of experience. After spending time in the automotive industry, Hall enrolled in CNC classes at Lenoir Community College and received his NIMS credentials in safety and materials in 2012. After Hall completed his exam, Lenoir hired him as a CNC machine instructor, where he has been teaching students about today’s manufacturing environment.
“With the introduction of CNC machining and CAD/CAM, there are ‘suit-and-tie’ positions in the machining world,” Hall said. “Most people don’t realize that. I would love to see people get away from the stereotype of the old, greasy, dark shop with dangerous machines.”
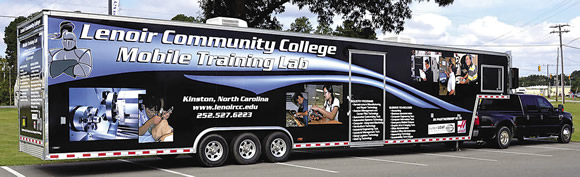
Courtesy of LCC
LCC’s mobile industrial training lab is a self-contained instructional classroom for teaching CNC machining skills.
Indeed, overcoming that stereotype is one of the goals of NIMS accreditation. If a program doesn’t look good to students, NIMS’s Wall asked, what’s the appeal?
“Even if a school has some high-tech CNC equipment, if it’s in the back of the shop and the shop isn’t well lighted, it’s going to be a detriment to recruiting,” he said. “We really encourage training centers to look at the physical facility and update it so it has the look and feel of a modern, high-tech manufacturing environment. We’re firm believers that what people see is more important than what you say, so if you say you’ve got an advanced manufacturing program and people walk in and see a lot of old machines painted gray under poor lighting … well, it doesn’t look good.”
Lenoir’s Hill takes the appeal of modern machining a step further in his recruitment program by operating a mobile training lab that captures the attention of attendees at machining-relevant events. Current instructor Hall was enticed to enroll at Lenoir after seeing the lab at one of his son’s motocross races, which illustrates the goal of connecting machining with prospective students’ hobbies and interests.
“I’ll talk about motorcycle parts and go-kart parts, and right now I’ve got a class making aluminum duck calls,” Hill said. “I have no idea how they’re going to sound, but I’ve got all these kids coming in every day ready to learn and ready to work.” In addition, Lenoir offers machinist math and machinist calculations classes that allow students to learn key concepts in a context that directly relates to their machining classes.
Machine Builder Adopts NIMS
While the vast majority of NIMS-accredited programs are at academic institutions, in May 2012, DMG Mori USA, Hoffman Estates, Ill., became one of the few manufacturing companies in the U.S. to boast having a NIMS-accredited training center, according to Rod Jones, senior adviser of business development and national sales for the machine tool builder.
“We had built a successful corporate training program, Mori Seiki University, that serves our employees and our customers well, and we went through unbelievable growth,” Jones said. “But the bottom line is you don’t really know how good you are until you take that step of courage and let someone come in and evaluate your program.”
Through completing the accreditation process, Mori Seiki University reorganized its documentation process, reevaluated its courses (including when and how students were tested for competencies) and addressed safety issues that had gone overlooked.
“When I first announced the accreditation program, it took the staff and faculty some courage to get behind it,” Jones said. “It was a long, hard process, but once we got through it, everybody was extremely motivated and really excited about having that additional stamp of approval.”
What sets Mori Seiki University’s training program apart from academic programs is the range of courses offered. Though its facility is a national testing center where anyone can take their NIMS credentialing examination, the training offered onsite, as well as company- and equipment-specific classes, assumes a certain level of understanding outside the scope of NIMS credentials. For example, there is no credential for 5-axis programming, but because DMG Mori builds and utilizes 5-axis machines, courses are offered as part of their accredited curriculum.
Although students at Mori Seiki University cannot receive college credit at this time, Jones is working with community colleges in the area to establish matriculation agreements for internships and work-study programs.
“I think the reason more companies have not sought NIMS accreditation at this point is a lack of familiarity,” Jones said. “I also think a lot of companies look at education as something that’s an expense rather than an investment.”
National Baseline
As more and more established organizations seek accreditation for their training programs, the closer the metalworking industry gets to developing a national baseline for skilled machinists. The basis of the NIMS accreditation program is convening groups of industry leaders to develop standards, and those standards and the associated requirements are updated and reviewed by the American National Standards Institute (ANSI) every year, according to Wall.
The accreditation process helps ensure a program is continuously improving and building enrollment, according to NIMS’s Wall. “We’ve seen an increase in enrollment in the last 18 months that has been driven by [job losses from] the [Great] Recession and the realization that manufacturing in the U.S. is alive and well, but programs still need to work on recruiting.”
Lenoir’s Hill sees the universal and evolving nature of NIMS as the answer to outdated training models of the past. The journeyman’s program, he explained, differs from company to company, depending on a company’s specialty and the available equipment. NIMS standards reduce or eliminate those differences.
“Once NIMS is recognized on a more national level, a NIMS graduate’s skills will be recognized no matter where he goes,” he explained. “NIMS is going to be the tool [the manufacturing industry] can use to move forward, and there are a lot of people on board who are really passionate about it. NIMS is the tool that will get us, in North Carolina and in the industry as a whole, where we need to be.” CTE
About the Author: Evan Jones Thorne is assistant editor for CTE. He can be reached at (847) 714-0177 or [email protected].
Casting a different spotlight on manufacturing
“For the record, Starbucks does not sell coffee,” joked comedian Hal Sparks in his 2010 stand-up special, “Charmageddon.” “Starbucks sells milkshakes. Coffee is that [stuff] your dad used to drink by the gallon so he could stay awake at work and not fall into the machinery.”
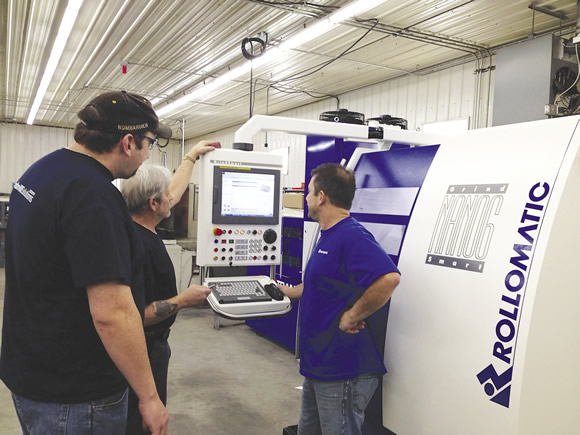
Courtesy of Advanced Tool
Dave Pugliese (center) and Rob DePerno (right) instruct Advanced Tool trainee Dave Carney on a Rollomatic GrindSmart Nano6 CNC tool grinder.
Starbucks will probably be fine, whatever jokes comedians make at its expense, but the real casualty of Sparks’ bit is the machining industry. His casual assertion that operating a machine tool is life-threatening was based on an outdated stereotype so prevalent it has become tacitly accepted in American culture. But the simple fact that the stereotype exists isn’t the problem, according to Advanced Tool President and CEO Sherry DePerno.
“The biggest problem is a lack of knowledge, a lack of exposure to what machining has become,” she said. “I don’t think kids know how exciting the industry is. Those stereotypes exist, but there’s nothing to counter them, nothing to tell people that they aren’t accurate, and, as a result, there are still parents who don’t want their kids to go into manufacturing because of this idea they have of being stuck at one machine in a dark, dirty room, day in and day out.”
Advanced Tool, Marcy, N.Y., retooled its training program to combat these misperceptions. Originally, new hires “shadowed” experienced engineers, learning skills through observing and asking questions. However, this approach came at the expense of productivity, and many trainees felt overwhelmed by this approach and left within 6 months.
“There wasn’t a formal training program, and my senior workers were dreading the process of hiring anybody new,” DePerno said. “I had to find a better way, or I was going to go out of business.”
Advanced Tool hired a dedicated trainer who could start with no knowledge of the company’s processes and systematically dissect each step, building a curriculum from the ground up. In this way, DePerno hoped to increase training efficiency as well as consistent part quality.
“I don’t know what the future holds for my company if I can’t find people who want to work here,” she said. “I think [high schools] push students to go for 4-year degrees, and manufacturing is seen as a place where people can go if they don’t know what they want to do with their lives. I don’t want that. I want people who choose this profession, who see this as exciting. I want people who want to use their brain and their hands, who don’t want to sit behind a desk all day.”
— E. Jones Thorne
Contributors
Advanced Tool
(315) 768-8502
www.advancedtool.com
DMG Mori USA
(847) 387-1290
www.dmgmori-usa.com
Lenoir Community College
(252) 527-6223
www.lenoircc.edu
National Institute for Metalworking Skills Inc.
(703) 352-4971
www.nims-skills.org
SaveSave
Related Glossary Terms
- centers
centers
Cone-shaped pins that support a workpiece by one or two ends during machining. The centers fit into holes drilled in the workpiece ends. Centers that turn with the workpiece are called “live” centers; those that do not are called “dead” centers.
- computer numerical control ( CNC)
computer numerical control ( CNC)
Microprocessor-based controller dedicated to a machine tool that permits the creation or modification of parts. Programmed numerical control activates the machine’s servos and spindle drives and controls the various machining operations. See DNC, direct numerical control; NC, numerical control.
- metalworking
metalworking
Any manufacturing process in which metal is processed or machined such that the workpiece is given a new shape. Broadly defined, the term includes processes such as design and layout, heat-treating, material handling and inspection.