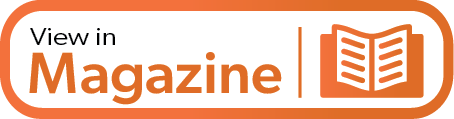
At this year’s IMTS, KUKA Robotics made a compelling case for automation with a demonstration of the company’s latest technologies. From advanced bin-picking systems to flexible mobile platforms, KUKA is showcased automation that can be both efficient and adaptable for manufacturing facilities of all sizes.
The centerpiece of KUKA’s booth was its smart bin-picking solution, which uses a 3D vision system developed in collaboration with Roboception, Munich, Germany. This technology enables robots to pick randomly placed parts from a bin, avoiding collisions and organizing them on trays for downstream processes.
“The 3D camera and KUKA’s smart bin-picking software work together seamlessly,” explained Phillip Peloso, a representative from KUKA Robotics. “The camera serves as the eyes, while the software provides the intelligence needed for collision-free motion planning.”
This system addresses common challenges in manufacturing by introducing raw parts into the production line in a controlled, organized manner, even when the initial setup is chaotic.
CNC Tending
KUKA’s CNC tending solution showcased the flexibility of the company’s industrial robots. These systems can handle low-volume, high-changeover applications while maintaining high-speed and industrial-grade performance.
“Our robots use safety scanners and KUKA’s Safe Operation software to ensure a fence-less operation,” Peloso noted. “This makes the technology accessible even for facilities with limited space or a hesitance toward full-scale automation.”
Parts can be delivered to the robot manually, via forklift, or through KUKA’s automated mobile platforms, offering scalable options for manufacturers at any stage of their automation journey. A key feature of the demonstration was the KUKA Mobile Platform system, or KMPs. These autonomous vehicles shuttle parts and empty totes throughout the operation, guided by KUKA Fleet Manager Software.
“The KMP system combines integrated lifts, sensors and vision systems to transport parts with precision,” Peloso said. “Whether it’s carrying filled trays to the CNC tending robot or cycling empty totes back to the bin-picking station, the KMP ensures smooth, efficient movement throughout the cell.”
This modular approach to automation allows facilities to start small and scale up as needed, integrating only the components that fit their space and operational needs.
KUKA’s modular setup at IMTS highlighted the company’s commitment to making automation accessible for all manufacturers. Smaller facilities can adopt just the CNC tending system, while larger operations might implement the entire workflow — from bin picking to tray organization to mobile transport.
The system’s programmability and integration options make it ideal for facilities with high-mix, low-volume production needs. Additionally, KUKA’s collaboration with partners like Roboception ensures cutting- edge vision and AI technologies are embedded into every solution.
“KUKA offers more than just robotics,” Peloso concluded. “We provide scalable, flexible automation solutions that empower manufacturers to improve productivity and safety, no matter their size or industry.”
For more information, visit the KUKA Robotics website.
Related Glossary Terms
- computer numerical control ( CNC)
computer numerical control ( CNC)
Microprocessor-based controller dedicated to a machine tool that permits the creation or modification of parts. Programmed numerical control activates the machine’s servos and spindle drives and controls the various machining operations. See DNC, direct numerical control; NC, numerical control.
- robotics
robotics
Discipline involving self-actuating and self-operating devices. Robots frequently imitate human capabilities, including the ability to manipulate physical objects while evaluating and reacting appropriately to various stimuli. See industrial robot; robot.
- vision system
vision system
System in which information is extracted from visual sensors to allow machines to react to changes in the manufacturing process.