END USER: Rolenn Medical Products, (951) 682-1185, www.rolenn.com.
CHALLENGE: Accurately machine EDM electrodes used to produce micromolds for medical parts.
SOLUTION: A high-speed, high-precision, 3-axis micro milling machine.
SOLUTION PROVIDER: Microlution Inc., (773) 282-6495, www.microlution-inc.com.
As medical devices get smaller and more sophisticated, creating the molds used to shape new products becomes more of a challenge. When finished parts are measured in millionths of inches, and the devices save or sustain lives, accuracy in the manufacturing process is paramount. Accurate molds are required to make accurate parts, and accurate cutting tools and machining equipment are needed to make these molds.
Most medical-device molds are made of ultrahard metals and require EDMing to cut the mold cavity and edges to specification. To achieve the tolerances of a new mold, Rolenn Medical Products, Riverside, Calif., often needs to make its own custom EDM electrodes.
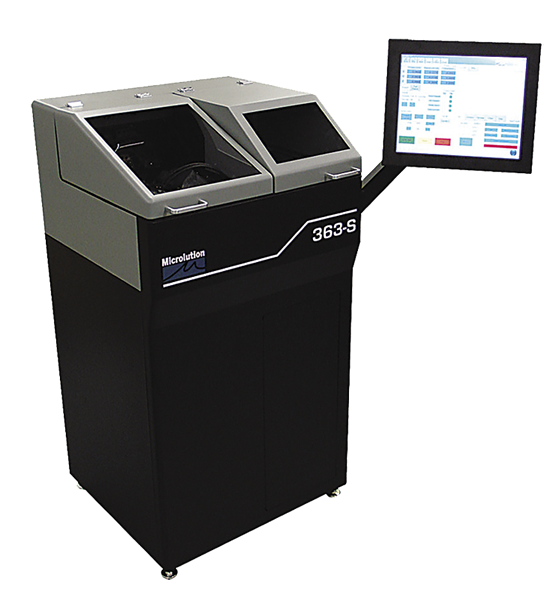
Rolenn produces small silicone parts for the medical industry (bottom) using molds created with EDM electrodes machined on its Microlution 363-S micromachine.
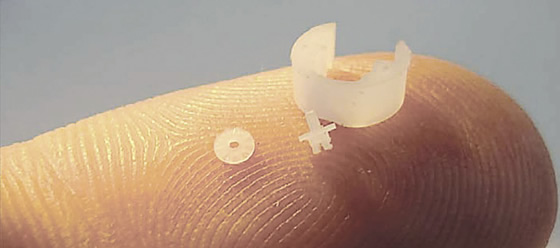
Ron Piotrowski, head of mold design at Rolenn, found a “go to” electrode milling solution in the Microlution 363-S from Microlution Inc., Chicago. The 3-axis micro milling machine offers micron level accuracy and tolerances, according to the machine tool builder. “Everything we do is a challenge,” he said. “Making electrodes for micromolds is one of them. The 363-S has handled everything we’ve thrown at it.”
Piotrowski found the Microlution 363-S when searching for a way to create a micromold for silicon seals that wouldn’t leak. Silicon, which has about the same viscosity as water, tends to find any gap in the mold, no matter how small. It costs as much as $1,500 per pound, so leakage is costly.
“These molds must be totally accurate with parting lines that match perfectly,” he explained. “The 363-S worked beautifully to create the electrodes we needed.”
The machine has a positional accuracy of ±0.00004”, a maximum spindle speed of 50,000 rpm or more and a working volume of 2.48” (63mm) on each axis, according to Microlution. It also features a granite base, palletized workholding, a 36-pocket automatic toolchanger and utilizes standard G-code programming. In addition to these features, Piotrowski found the high-acceleration capability of the linear motor-driven platform particularly attractive.
“The ways are magnetically controlled, which eliminates the need for a ballscrew, and there is absolutely no backlash, allowing measurements to be made accurately and easily,” he said. “Heidenhain glass scales measure everything, and I can control it to within 0.0010 ". Also, it has enough memory for code for very complex parts.”
Piotrowski added that the whole package cost about $130,000—far more palatable than the $250,000 price tag on many comparable machines the company explored.
In addition to machining electrodes, Rolenn uses the 363-S to mill some of the parts. “We’ve probably used this machine for more than 50 products,” Piotrowski said. “It’s easy to set up and reconfigure. We can drill holes 0.002” in diameter, and it goes through the material like butter. A 0.0015 " corner radius is a piece of cake.”
Rolenn operates two other manufacturing facilities, but the most demanding projects are always assigned to Piotrowski’s team. “People from our other facilities now send their high-precision stuff here,” Piotrowski said. “There are some things that just can’t be done with traditional equipment.”
Related Glossary Terms
- G-code programming
G-code programming
Programs written to operate NC machines with control systems that comply with the ANSI/EIA RS-274-D-1980 Standard. A program consists of a series of data blocks, each of which is treated as a unit by the controller and contains enough information for a complete command to be carried out by the machine.
- automatic toolchanger
automatic toolchanger
Mechanism typically included in a machining center that, on the appropriate command, removes one cutting tool from the spindle nose and replaces it with another. The changer restores the used tool to the magazine and selects and withdraws the next desired tool from the storage magazine. The changer is controlled by a set of prerecorded/predetermined instructions associated with the part(s) to be produced.
- backlash
backlash
Reaction in dynamic motion systems where potential energy that was created while the object was in motion is released when the object stops. Release of this potential energy or inertia causes the device to quickly snap backward relative to the last direction of motion. Backlash can cause a system’s final resting position to be different from what was intended and from where the control system intended to stop the device.
- electrical-discharge machining ( EDM)
electrical-discharge machining ( EDM)
Process that vaporizes conductive materials by controlled application of pulsed electrical current that flows between a workpiece and electrode (tool) in a dielectric fluid. Permits machining shapes to tight accuracies without the internal stresses conventional machining often generates. Useful in diemaking.
- gang cutting ( milling)
gang cutting ( milling)
Machining with several cutters mounted on a single arbor, generally for simultaneous cutting.
- micron
micron
Measure of length that is equal to one-millionth of a meter.
- milling
milling
Machining operation in which metal or other material is removed by applying power to a rotating cutter. In vertical milling, the cutting tool is mounted vertically on the spindle. In horizontal milling, the cutting tool is mounted horizontally, either directly on the spindle or on an arbor. Horizontal milling is further broken down into conventional milling, where the cutter rotates opposite the direction of feed, or “up” into the workpiece; and climb milling, where the cutter rotates in the direction of feed, or “down” into the workpiece. Milling operations include plane or surface milling, endmilling, facemilling, angle milling, form milling and profiling.
- milling machine ( mill)
milling machine ( mill)
Runs endmills and arbor-mounted milling cutters. Features include a head with a spindle that drives the cutters; a column, knee and table that provide motion in the three Cartesian axes; and a base that supports the components and houses the cutting-fluid pump and reservoir. The work is mounted on the table and fed into the rotating cutter or endmill to accomplish the milling steps; vertical milling machines also feed endmills into the work by means of a spindle-mounted quill. Models range from small manual machines to big bed-type and duplex mills. All take one of three basic forms: vertical, horizontal or convertible horizontal/vertical. Vertical machines may be knee-type (the table is mounted on a knee that can be elevated) or bed-type (the table is securely supported and only moves horizontally). In general, horizontal machines are bigger and more powerful, while vertical machines are lighter but more versatile and easier to set up and operate.
- milling machine ( mill)2
milling machine ( mill)
Runs endmills and arbor-mounted milling cutters. Features include a head with a spindle that drives the cutters; a column, knee and table that provide motion in the three Cartesian axes; and a base that supports the components and houses the cutting-fluid pump and reservoir. The work is mounted on the table and fed into the rotating cutter or endmill to accomplish the milling steps; vertical milling machines also feed endmills into the work by means of a spindle-mounted quill. Models range from small manual machines to big bed-type and duplex mills. All take one of three basic forms: vertical, horizontal or convertible horizontal/vertical. Vertical machines may be knee-type (the table is mounted on a knee that can be elevated) or bed-type (the table is securely supported and only moves horizontally). In general, horizontal machines are bigger and more powerful, while vertical machines are lighter but more versatile and easier to set up and operate.
- parting
parting
When used in lathe or screw-machine operations, this process separates a completed part from chuck-held or collet-fed stock by means of a very narrow, flat-end cutting, or parting, tool.
- toolchanger
toolchanger
Carriage or drum attached to a machining center that holds tools until needed; when a tool is needed, the toolchanger inserts the tool into the machine spindle. See automatic toolchanger.