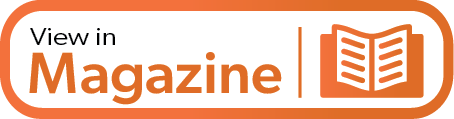
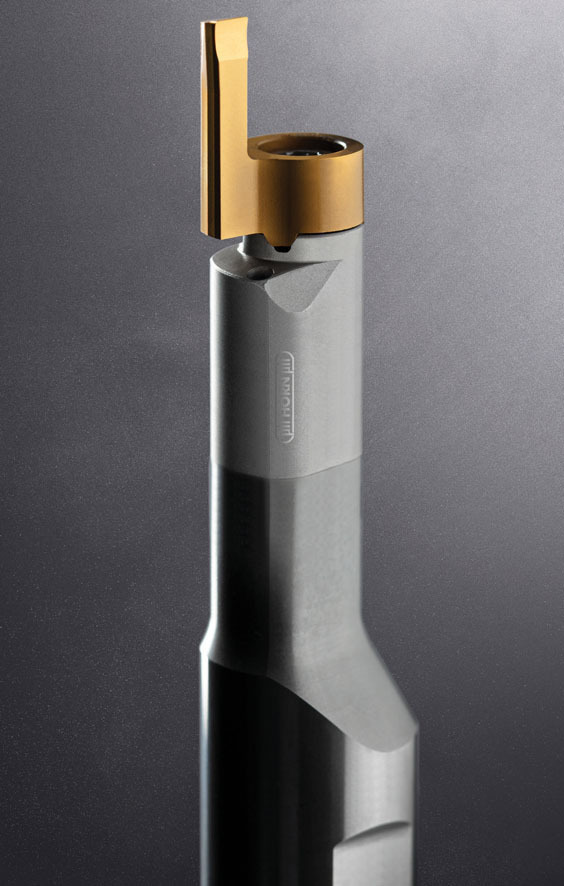
The latest addition to the Mini line from Paul Horn GmbH, the Mini 114 allows face grooving up to 10 mm deep. “Until this new addition, the deepest you could go with this system was 6 mm,” noted Michael Morgan, application and sales engineer at Horn USA Inc. in Franklin, Tennessee.
Horn says the insert is designed for turning and copy turning of axial grooves. The company offers the EG55 carbide grade grooving tool in three standard types with cutting widths of 2 mm, 2.5 mm and 3 mm. The minimum grooving diameter is 14 mm, while the maximum is 34-36 mm, depending on the type.
Compatible with the existing Mini axial holder system, the Mini 114 does not require a special tool holder. Like other members of the Mini line, Morgan points out that Mini 114 inserts are paired with low-vibration carbide holders that, unlike their steel counterparts, won’t cause chatter or vibration issues at greater length-to-diameter ratios. As a result, he said, the inserts will produce a good surface finish even with long overhangs.
As the name suggests, the face-screwed inserts of the Mini system are small tools for small part manufacturing. The tools have proven to be particularly effective for boring and internal grooving as well as for face grooving, according to Horn.
Though some members of the Mini line are a good choice for both turning and milling applications, this does not apply to the Mini 114, according to Morgan. The reason, he explained, is that Horn grinds the neck of the holder into an elliptical shape. While this increases the mass holding the insert, giving it additional strength, it also creates an imbalance when the tool is rotated. As a result, he said, the Mini 114 is primarily a turning tool.
With the introduction of the Mini 114, the Mini line is now up to nine members, which fit into different bore sizes ranging from 6 mm to 18 mm. (The Mini 114 fits into a 14 mm hole.) In addition to different sizes, Mini inserts come in different carbide grades and can also be made with CBN or PCD tips.
According to Morgan, the 114 offers the widest variety of options of any insert in the Mini line. He reports that the 114 system includes almost 700 standard inserts with different coatings, dimensions and other characteristics that can be chosen to meet the requirements of different cutting applications.
Though most of Horn’s main competitors offer products similar to the Mini 114, Morgan said that none of the others can reach a face-grooving depth of 10 mm. And then there’s the number and variety of the offerings. “Where we hold an advantage is the breadth of the product line,” he said. “There's a lot more standard products that we have that our competitors don't."
Related Glossary Terms
- boring
boring
Enlarging a hole that already has been drilled or cored. Generally, it is an operation of truing the previously drilled hole with a single-point, lathe-type tool. Boring is essentially internal turning, in that usually a single-point cutting tool forms the internal shape. Some tools are available with two cutting edges to balance cutting forces.
- chatter
chatter
Condition of vibration involving the machine, workpiece and cutting tool. Once this condition arises, it is often self-sustaining until the problem is corrected. Chatter can be identified when lines or grooves appear at regular intervals in the workpiece. These lines or grooves are caused by the teeth of the cutter as they vibrate in and out of the workpiece and their spacing depends on the frequency of vibration.
- cubic boron nitride ( CBN)
cubic boron nitride ( CBN)
Crystal manufactured from boron nitride under high pressure and temperature. Used to cut hard-to-machine ferrous and nickel-base materials up to 70 HRC. Second hardest material after diamond. See superabrasive tools.
- gang cutting ( milling)
gang cutting ( milling)
Machining with several cutters mounted on a single arbor, generally for simultaneous cutting.
- grooving
grooving
Machining grooves and shallow channels. Example: grooving ball-bearing raceways. Typically performed by tools that are capable of light cuts at high feed rates. Imparts high-quality finish.
- milling
milling
Machining operation in which metal or other material is removed by applying power to a rotating cutter. In vertical milling, the cutting tool is mounted vertically on the spindle. In horizontal milling, the cutting tool is mounted horizontally, either directly on the spindle or on an arbor. Horizontal milling is further broken down into conventional milling, where the cutter rotates opposite the direction of feed, or “up” into the workpiece; and climb milling, where the cutter rotates in the direction of feed, or “down” into the workpiece. Milling operations include plane or surface milling, endmilling, facemilling, angle milling, form milling and profiling.
- polycrystalline diamond ( PCD)
polycrystalline diamond ( PCD)
Cutting tool material consisting of natural or synthetic diamond crystals bonded together under high pressure at elevated temperatures. PCD is available as a tip brazed to a carbide insert carrier. Used for machining nonferrous alloys and nonmetallic materials at high cutting speeds.
- turning
turning
Workpiece is held in a chuck, mounted on a face plate or secured between centers and rotated while a cutting tool, normally a single-point tool, is fed into it along its periphery or across its end or face. Takes the form of straight turning (cutting along the periphery of the workpiece); taper turning (creating a taper); step turning (turning different-size diameters on the same work); chamfering (beveling an edge or shoulder); facing (cutting on an end); turning threads (usually external but can be internal); roughing (high-volume metal removal); and finishing (final light cuts). Performed on lathes, turning centers, chucking machines, automatic screw machines and similar machines.