A scaled-down version of a full-featured control and monitoring system could save money for shops but still meet the requirements of less complicated machining processes.
Sold by Marposs Corp. in Auburn Hills, Michigan, the BLÚ LT modular system is designed to provide real-time process control and monitoring of machine tools in applications that don’t require all the capabilities of the company’s high-end BLÚ system.
“Consider the LT the light version of the BLÚ system,” said Product Manager Frank Powell. “The regular BLÚ system is for complex applications with multiple functions. The BLÚ LT is for more medium-complexity applications where you want the technology and integration abilities of the BLÚ but you don’t need the full-cost network of the BLÚ system.”
Besides allowing fewer sensors than the BLÚ, he said the BLÚ LT requires the sensors to stay within 30 m (98') of the master control panel while the BLÚ system allows the sensors to be located up to 120 m (394') from the control panel. At present, the BLÚ LT accommodates acoustic-emission and spindle-vibration sensors. But he said the plan is for the system to eventually offer sensors that also monitor other types of vibration, as well as power sensors. Monitoring these parameters permits predictive maintenance based on a machine’s changing operating status, he said.
In addition to sensors, the BLÚ LT can use gauges both in process for grinding and post-process for grinding, turning and other applications. The BLÚ LT also can include various systems that control aspects of a machining process, such as automatic grinding-wheel balancing.
In its two formats, the BLÚ LT master unit can directly host as many as two or four function nodes, each of which handles a specific function. For example, a spindle-vibration function node controls the spindle-vibration sensor, receives data from that sensor and formats the data for processing. With the BLÚ LT, all communication between the master processing unit and the functional nodes is handled by the same protocol used by the BLÚ
system.
Designed to allow integration of the measurement system, the machine and the company network, the BLÚ LT features the BLÚ Human Interface for communication between the operator and the BLÚ control system. According to Marposs, the BLÚ HI is easy to use and meets the requirements of digitized “smart factories” that use connected devices, machines and systems to continuously collect and share data. BLÚ HI dashboards can be displayed by a machine’s PC in their own window or resized to fit into a machine’s control screen. The BLÚ LT also can be supplied with a 178 mm (7") 16-9 color touch-screen display for easier programming.
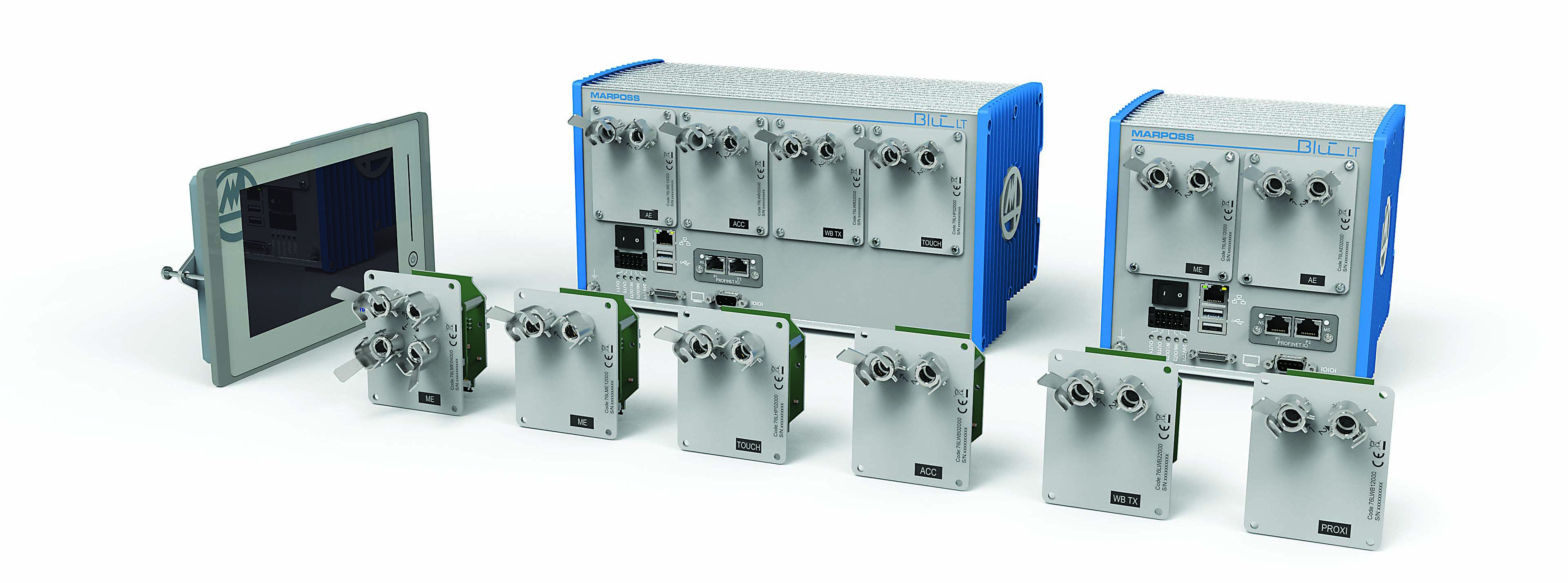
One feature that distinguishes both the BLÚ and BLÚ LT from competitive systems is the proprietary Marposs Measure System Bus, or MMSB. Although most competitors rely on widely used commercial fieldbus technology, Powell said his company developed the MMSB because it needed a much faster system to transmit real-time information. The MMSB actually includes a couple of different buses, he explained. One is a high-speed “priority bus” for data that must be transmitted very quickly while the other is a more traditional bus for slower, nonpriority communication to and from the nodes. In addition to communication signals, the MMSB carries power for the system components.
To determine whether the BLÚ LT can be substituted for the BLÚ in an application, he said shops need to consider two things: the number of functions that must be controlled and the maximum distance between the sensors and the master unit. If the application requires more than eight functions and/or sensors need to be positioned more than 30 m from the master, shops need the full-featured BLÚ system.
But if eight or fewer functions are suitable and sensors will stay in closer proximity to the master, Powell said the BLÚ LT will cost about 20% less than the BLÚ for applications that would require the same number of sensors regardless of which system was deployed.
In those cases, he said, “why do you need the big capacity?”
Contact Details
Related Glossary Terms
- grinding
grinding
Machining operation in which material is removed from the workpiece by a powered abrasive wheel, stone, belt, paste, sheet, compound, slurry, etc. Takes various forms: surface grinding (creates flat and/or squared surfaces); cylindrical grinding (for external cylindrical and tapered shapes, fillets, undercuts, etc.); centerless grinding; chamfering; thread and form grinding; tool and cutter grinding; offhand grinding; lapping and polishing (grinding with extremely fine grits to create ultrasmooth surfaces); honing; and disc grinding.
- process control
process control
Method of monitoring a process. Relates to electronic hardware and instrumentation used in automated process control. See in-process gaging, inspection; SPC, statistical process control.
- turning
turning
Workpiece is held in a chuck, mounted on a face plate or secured between centers and rotated while a cutting tool, normally a single-point tool, is fed into it along its periphery or across its end or face. Takes the form of straight turning (cutting along the periphery of the workpiece); taper turning (creating a taper); step turning (turning different-size diameters on the same work); chamfering (beveling an edge or shoulder); facing (cutting on an end); turning threads (usually external but can be internal); roughing (high-volume metal removal); and finishing (final light cuts). Performed on lathes, turning centers, chucking machines, automatic screw machines and similar machines.