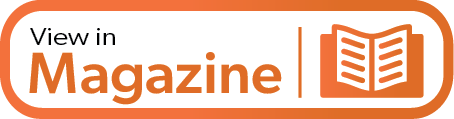
Readers of this publication are likely familiar with two realities about the modern machining industry.
First, the industry has evolved dramatically over the last 20 years. A bewildering variety of cutting tool geometries, substrates, coatings, and software solutions offer to optimize cutting processes, driving innovation across aerospace, automotive, medical, and other industries. High-performance tooling has become essential, but has yet to develop a significant presence within the curriculum for most undergraduate engineering programs.
Second, many engineering students graduate with minimal practical knowledge of modern machining practice. Their experience often consists of machining a few aluminum parts using outdated tools and machines. This leaves them ill-prepared for today’s world of higher material removal rates, tighter tolerances and advanced materials.
This gap is the driving force behind Utah Tech University’s new engineering course, “MECH 4990 - Modern Machining.” Designed for junior and senior engineering students, the course aims to create engineers equipped with both a fascination with machining and the expertise to make real-world decisions.
What sets this course apart? Three core ideas:
1. Technical Depth:
Students dive into the physics and thermodynamics of chip formation, understanding phenomena like heat generation, cutting forces and work-hardening. Lectures explore carbide substrate quality, tool geometry and machining strategies like high-feed milling. The curriculum emphasizes how these technical details tie directly to machining economics, teaching students how small decisions can significantly impact productivity.
2. Hands-On Learning:
The course goes beyond theoretical knowledge. Students run real-world experiments, such as testing PCD cutting tools to reduce cycle times or generating stability lobe diagrams to optimize cutting conditions. Projects include machining titanium impellers and designing processes for repeatable production runs, ensuring students gain relevant, applicable experience.
3. Utilizing World-Class Tools:
Unlike typical programs that rely on low-cost machines and tools, Utah Tech prioritizes exposing students to industry-standard equipment. This includes advanced tool-holders, high-quality cutting tools and challenging materials. By working with these tools and materials, students learn why details matter, and develop the skills to design successful, profitable processes.
Intrigued?
This is just the beginning. Discover how Utah Tech is forging partnerships with industry leaders, overcoming budget challenges and preparing the next generation of engineers.
Related Glossary Terms
- gang cutting ( milling)
gang cutting ( milling)
Machining with several cutters mounted on a single arbor, generally for simultaneous cutting.
- milling
milling
Machining operation in which metal or other material is removed by applying power to a rotating cutter. In vertical milling, the cutting tool is mounted vertically on the spindle. In horizontal milling, the cutting tool is mounted horizontally, either directly on the spindle or on an arbor. Horizontal milling is further broken down into conventional milling, where the cutter rotates opposite the direction of feed, or “up” into the workpiece; and climb milling, where the cutter rotates in the direction of feed, or “down” into the workpiece. Milling operations include plane or surface milling, endmilling, facemilling, angle milling, form milling and profiling.
- polycrystalline diamond ( PCD)
polycrystalline diamond ( PCD)
Cutting tool material consisting of natural or synthetic diamond crystals bonded together under high pressure at elevated temperatures. PCD is available as a tip brazed to a carbide insert carrier. Used for machining nonferrous alloys and nonmetallic materials at high cutting speeds.