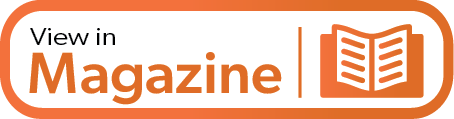
The waterjet cutting industry has witnessed remarkable advancements, and OMAX Corp. stands at the forefront of these developments with a commitment to innovation, sustainability and customer success. In an exclusive interview, OMAX Senior Regional Sales Manager Dave Kvasnicka shared insights into the company’s latest advancements.
The OMAX journey took a significant turn when it joined the Hypertherm Associates family, Kvasnicka said, noting that the partnership not only expanded OMAX’s technological offerings but also strengthened its global presence as a leader in plasma cutting solutions.
“Hypertherm’s involvement has been a booster rocket for us,” Kvasnicka noted. “It has allowed us to integrate complementary technologies and provide comprehensive solutions to our clients.”
Equally noteworthy is OMAX’s transformation into an employee-owned company. This change instills a vested interest in every employee, from shipping personnel to executives. “Being employee-owned means we all care deeply about our customers’ success,” Kvasnicka emphasized. “This unique structure translates into exceptional service and support for our partners.”
OMAX continues to lead the way with cutting- edge products. The new OptiMAX system exemplifies the company’s drive for innovation, incorporating advanced automation features that streamline operations and minimize operator responsibilities.
“The OptiMAX system practically guides itself,” Kvasnicka explained. “With sensors, monitors, and self-calibrating technology, it ensures optimal performance while reducing the potential for human error.”
He cited the OptiMAX 60X, in particular, for setting a new benchmark in waterjet cutting technology. This advanced system, which can handle a diverse range of materials and thicknesses, features:
- a cutting area of up to 13' by 6.5', making it ideal for large-scale industrial applications.
- IntelliMAX software, which is said to deliver cutting accuracy that ensures clean, precise cuts for even the most complex designs.
- intuitive controls, automated calibration and self-diagnostic capabilities that minimize downtime.
Plus, the system maximizes energy efficiency while minimizing water and abrasive usage.
Sustainability remains a core value for OMAX. The company prioritizes eco-friendly manufacturing practices, and designs products that support sustainable operations for customers.
OMAX waterjet systems cater to a range of industries, including aerospace, medical, automotive and general manufacturing. The technology’s versatility allows customers to cut materials as diverse as steel, glass, rubber and even T-shirt blanks.
“The diversity of applications is one of the reasons customers choose OMAX,” Kvasnicka said. “Whether you’re creating precision parts for aerospace or prototypes for educational settings, our systems deliver exceptional performance.”
The company’s consultative sales approach ensures that clients receive tailored solutions.
“We don’t sell a system until we’re confident it’s the right fit for the customer,” Kvasnicka stated. “From analyzing their business goals to providing lifetime support, we’re committed to their success.”
This philosophy extends to education and training. OMAX provides unlimited software seats, access to resources and ongoing training, ensuring customers maximize the value of their investment.
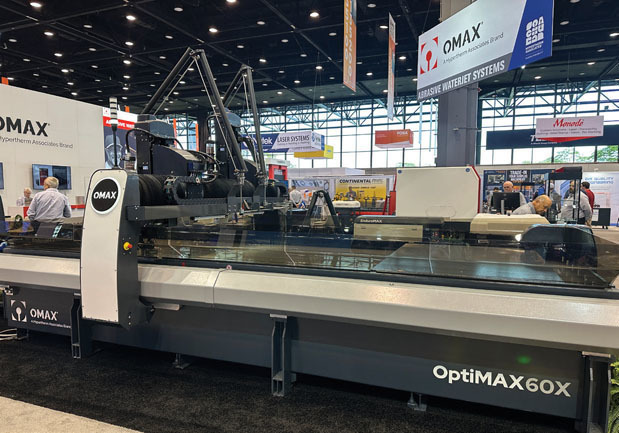
OMAX’s dedication to technological advancement is evident in its new dashboard monitoring system. This intuitive tool offers predictive maintenance insights, operational efficiency metrics, and real-time data analysis.
The OMAX app further simplifies maintenance and part ordering. By scanning a machine’s serial number, users can access detailed schematics, identify required parts, and streamline the ordering process.
“Our goal is to make operations as seamless as possible for our customers,” Kvasnicka explained. “From self-monitoring machines to centralized data dashboards, we’re redefining efficiency in manufacturing.”
If you’re ready to explore OMAX’s innovative solutions, visit the company's website.
Related Glossary Terms
- abrasive
abrasive
Substance used for grinding, honing, lapping, superfinishing and polishing. Examples include garnet, emery, corundum, silicon carbide, cubic boron nitride and diamond in various grit sizes.
- calibration
calibration
Checking measuring instruments and devices against a master set to ensure that, over time, they have remained dimensionally stable and nominally accurate.
- waterjet cutting
waterjet cutting
Fine, high-pressure (up to 50,000 psi or greater), high-velocity jet of water directed by a small nozzle to cut material. Velocity of the stream can exceed twice the speed of sound. Nozzle opening ranges from between 0.004" to 0.016" (0.l0mm to 0.41mm), producing a very narrow kerf. See AWJ, abrasive waterjet.