Companies reshoring parts production are often happy if part cost back home is somewhat close to what they were paying for overseas production. INOVA Geophysical Equipment Ltd. reshored a part and not only produced it at a lower cost, but also reaped other benefits—such as more reliable supply.
In the winter of 2011, INOVA, based in Stafford, Texas, started selling the G3i, a flexible, cable-based recording system for oil and gas exploration and production companies and seismic contractors prospecting for reserves. The unit consists of three main parts: an extruded aluminum shell, a circuit board inside the shell and two 6061 aluminum connector plates that link electrical and communications cables, one on each side of the shell.
INOVA Geophysical Equipment video report offers an overview of the company's facility.
At that time, I was working as machine shop supervisor at INOVA’s regional operations in Calgary, Alberta, and we had no idea how many G3i units we would sell, but 3½ years later, INOVA has built 250,000 units, using a total of 500,000 connector plates.
As demand grew, the machine shop had to overcome several challenges to keep up. The easiest solution would have been to buy and install a new, high-speed horizontal machining center with several pallets—a time-consuming process. We decided instead to increase production without a new machine.
The 3½ "×2½ "×2½ " (88.9mm × 63.5mm × 63.5mm) connector plates are made on two Haas VF3 vertical machining centers, each equipped with a two-pallet changer. In our previous production process, each pallet used two double vises, each of which can hold two parts. Although the vises are handy and convenient, they are not always good for production. The vises consumed too much room on a pallet, so we could only make four parts per pallet.
Each connector plate took 12 minutes to machine, and the machine shop ran two 10-hour shifts 4 days a week. It took two operators to run both VMCs. With both running, we could produce 800 connector plates per week, but we needed at least 1,500 per week to keep up with demand.
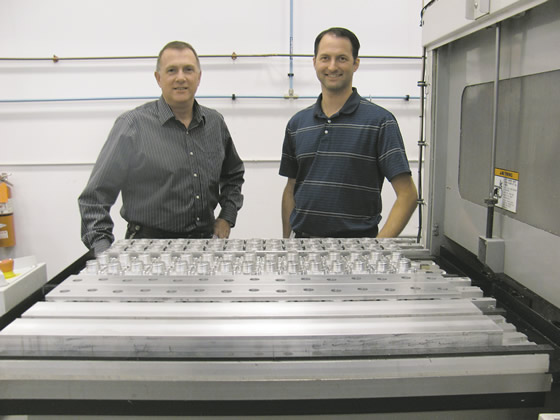
Randy Cameron (left), director, technical services, manufacturing for INOVA Geophysical Equipment, and Tom Mueller, former machine shop supervisor for INOVA. All images courtesy INOVA Geophysical Equipment.
As a result, Production Planner Ashley Rees was forced to outsource production. A sister plant in China supplied 22,500 parts and two job shops in Calgary made about 50 percent of our connector plates, or about 750 parts per week.
However, outsourcing created other problems. The parts must be repeatable and meet tolerances as tight as 0.001 " (0.0254mm), as they are run through a silicone injection molding machine to add a silicone sleeve to a bore in the part to create a watertight seal. If the bores vary by just a few thousandths of an inch, the silicone sleeve will be overshot or undershot.
To maintain quality, we allocated additional resources for continuous inspection of incoming connector plates. Job shops have multiple clients and typically don’t dedicate a machine to a specific job. Every time there is a change from one job to another, the potential for errors exists, hence the need for continuous inspection.
While the quality of the first shipment of 7,500 parts from our Chinese vendor was above our expectations and the price per part was about half of what we made it for, there were serious delivery issues. Our vendor sent the parts in two shipments. The first shipment, due early June 2012, was stopped in Anchorage, Alaska, by the U.S. Customs Service and returned to China because the parts were packaged in wood crates, which could house plant pests and diseases. We finally received the parts in early August. Needless to say, it was hard to plan production when we didn’t know when the parts would arrive. The second shipment of 15,000 parts arrived in November 2012.
New Plan
As a result, we looked at ways to make all of the connector plates in our shop without increasing manufacturing costs or adding machining capacity. We determined that better fixturing might accomplish this goal.
We knew we had to get as many parts on a 3 '×28 " (0.9m × 711.2mm) pallet as possible. The more parts we could machine per tool change, the better. Randy Cameron, director of technical services, Steven Jiang, mechanical engineer, and I calculated that if we staggered our parts by alternating them with one part slightly higher and one slightly lower in each row, we could get 60 parts per pallet in four rows (two rows of 15 parts for the first operation,and two rows of 15 parts for the second operation). As a result, we went from machining four parts on a pallet to 60 parts. A GibbsCAM TMS (tombstone management system) made it fairly easy to program the job, and Tungaloy’s Tung-AluMill insert cutter, which provided an excellent ramp angle and material- removal rate to help expedite machining. The problem was how to hold the parts.
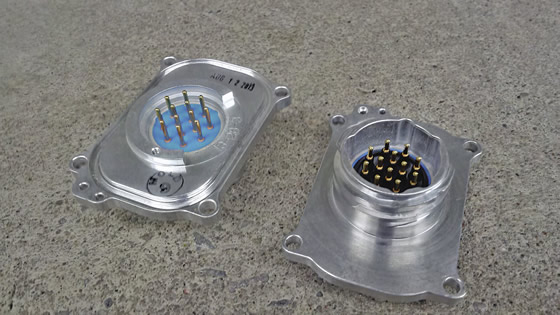
Connector plates for the G3i cable-based recording system (above). The completed device (below).
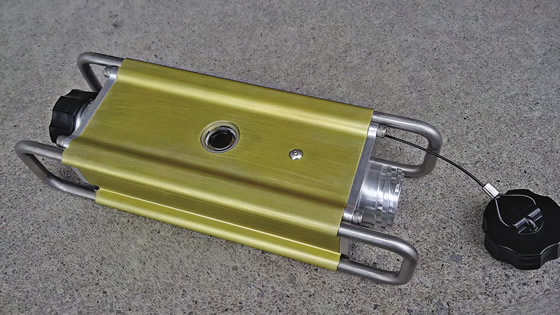
After we talked with Monte Dumesnil, district sales manager from DGI Supply, Calgary, he suggested clamping products from Mitee-Bite Products LLC, Center Ossipee, N.H.
In op. 1, we used two rows of Mitee-Bite locating rails on the bottom row of parts and a row of Mitee-Bite Uniforce clamps in the middle to securely hold two 2.5 "x1.5 "x36 " (63.5mm × 38.1mm × 914.4mm) aluminum bars for roughing (15 parts were machined on each bar and separated during final machining).
In op. 2, we used 30 Mitee-Bite ID Xpansion clamps. The clamps are easily turned on a CNC lathe. Machining the clamps to exactly match multiple bore diameters greatly increased the clamping surface.
After the parts were machined in op. 1, we loosened the Uniforce clamps and took the two full-length bars, removed them from the pallet and flipped them, then slid them onto the ID Xpansion clamps for machining on the back of the parts in op. 2. This process did not require us to move all 30 parts individually—instead, the bar slid into place with a light hit from a 3-lb. (1.36-kg) dead blow mallet.
When the connector plates were in place, the operator tightened a ½ " (12.7mm) bolt on the ID clamps for each part with a set torque wrench.Finish machining of the bar in op. 2 separated the parts from each other, and they were ready to be unbolted and readied for the molding department.
Substantial Savings
After implementing the new fixture, we dramatically decreased cost per part. With our old setup, each connector plate cost $19.29 to manufacture and only 200 units could be made daily. With the new setup, the machining cost is $4.96, a savings of roughly 75 percent. It only takes one operator to run the two VMCs, as opposed to two operators under the old setup. The new fixture and machining process also allow an operator to set up the machine for 2.5 hours of lights-out machining per machine per day. With the increase in parts per pallet and lights-out machining, we can now make 450 parts daily, a 125 percent increase.
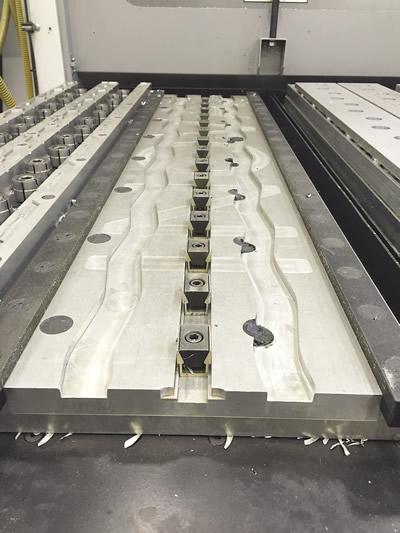
In the photo above, the pallet is ready to receive aluminum bars for op. 1. Mitee-Bite expansion clamps are positioned between the two sections of the pallet. After the bars are loaded on the pallet in the photo below, tightening the ¼ "-20 bolts pushes the work material against the fixed black rails. There are two rows ready for op.1 (right-hand side of image below) and two rows ready for op. 2 (left in image below). The wavy grooves on the pallet are chip channels, so chips can easily wash out after through-holes are drilled. All bolt holes in the fixture are filled with silicone so they don 't fill with chips and coolant, which simplifies cleaning.
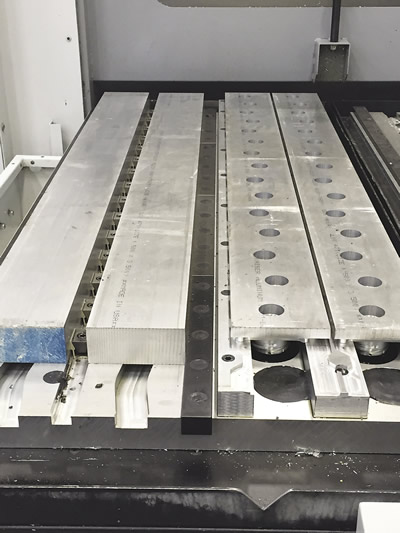
We are also able to machine 36 "-long aluminum stock instead of sawing individual blanks prior to machining, drastically reducing saw cutting and saving $105,000 per year. We also saved 17 cents per part on material by staggering the parts so they took up less space on the bar ($13,600 when producing 80,000 parts yearly).
By eliminating outsourcing, reducing machining time per unit and using the Mitee-Bite workholding, we saved $971,400 on the machining of 80,000 connector plates per year. In addition to the savings, my personal target was to make the connector plates cheaper than our Chinese supplier; the total cost of our part, including material, is $7.31, which is 70 cents cheaper than the parts purchased in China.
Also, we can adjust part output based on actual production needs and no longer need to deal with supply issues. Our new machining setup and fixtures allow us to save close to $1 million per year, produce parts cheaper than they can be made in China, and become a leaner manufacturing operation. CTE
Related Glossary Terms
- centers
centers
Cone-shaped pins that support a workpiece by one or two ends during machining. The centers fit into holes drilled in the workpiece ends. Centers that turn with the workpiece are called “live” centers; those that do not are called “dead” centers.
- computer numerical control ( CNC)
computer numerical control ( CNC)
Microprocessor-based controller dedicated to a machine tool that permits the creation or modification of parts. Programmed numerical control activates the machine’s servos and spindle drives and controls the various machining operations. See DNC, direct numerical control; NC, numerical control.
- coolant
coolant
Fluid that reduces temperature buildup at the tool/workpiece interface during machining. Normally takes the form of a liquid such as soluble or chemical mixtures (semisynthetic, synthetic) but can be pressurized air or other gas. Because of water’s ability to absorb great quantities of heat, it is widely used as a coolant and vehicle for various cutting compounds, with the water-to-compound ratio varying with the machining task. See cutting fluid; semisynthetic cutting fluid; soluble-oil cutting fluid; synthetic cutting fluid.
- fixture
fixture
Device, often made in-house, that holds a specific workpiece. See jig; modular fixturing.
- inner diameter ( ID)
inner diameter ( ID)
Dimension that defines the inside diameter of a cavity or hole. See OD, outer diameter.
- lathe
lathe
Turning machine capable of sawing, milling, grinding, gear-cutting, drilling, reaming, boring, threading, facing, chamfering, grooving, knurling, spinning, parting, necking, taper-cutting, and cam- and eccentric-cutting, as well as step- and straight-turning. Comes in a variety of forms, ranging from manual to semiautomatic to fully automatic, with major types being engine lathes, turning and contouring lathes, turret lathes and numerical-control lathes. The engine lathe consists of a headstock and spindle, tailstock, bed, carriage (complete with apron) and cross slides. Features include gear- (speed) and feed-selector levers, toolpost, compound rest, lead screw and reversing lead screw, threading dial and rapid-traverse lever. Special lathe types include through-the-spindle, camshaft and crankshaft, brake drum and rotor, spinning and gun-barrel machines. Toolroom and bench lathes are used for precision work; the former for tool-and-die work and similar tasks, the latter for small workpieces (instruments, watches), normally without a power feed. Models are typically designated according to their “swing,” or the largest-diameter workpiece that can be rotated; bed length, or the distance between centers; and horsepower generated. See turning machine.
- machining center
machining center
CNC machine tool capable of drilling, reaming, tapping, milling and boring. Normally comes with an automatic toolchanger. See automatic toolchanger.
- sawing
sawing
Machining operation in which a powered machine, usually equipped with a blade having milled or ground teeth, is used to part material (cutoff) or give it a new shape (contour bandsawing, band machining). Four basic types of sawing operations are: hacksawing (power or manual operation in which the blade moves back and forth through the work, cutting on one of the strokes); cold or circular sawing (a rotating, circular, toothed blade parts the material much as a workshop table saw or radial-arm saw cuts wood); bandsawing (a flexible, toothed blade rides on wheels under tension and is guided through the work); and abrasive sawing (abrasive points attached to a fiber or metal backing part stock, could be considered a grinding operation).
- sawing machine ( saw)
sawing machine ( saw)
Machine designed to use a serrated-tooth blade to cut metal or other material. Comes in a wide variety of styles but takes one of four basic forms: hacksaw (a simple, rugged machine that uses a reciprocating motion to part metal or other material); cold or circular saw (powers a circular blade that cuts structural materials); bandsaw (runs an endless band; the two basic types are cutoff and contour band machines, which cut intricate contours and shapes); and abrasive cutoff saw (similar in appearance to the cold saw, but uses an abrasive disc that rotates at high speeds rather than a blade with serrated teeth).