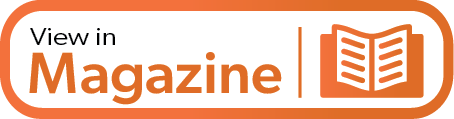
Machinists are a unique bunch of people. Ask 10 machinists the same question about machining, and you’ll get 10 different answers — each delivered with the vigor and conviction of those who rarely change their position on a subject.
Such entrenched opinions have given rise to many of the comments we hear about machine tools. Phrases like “that’s a throwaway machine” or “you can’t take a cut with those things” reflect a machinist’s unshakable opinion about a machine tool brand they don’t like.
Machinists also have strong opinions about the construction of machines. You can hear them denounce the guideway structure, spindle interface, CNC control, type of tool changer, and more.
Grumpy curmudgeon machinist attitudes aside, every brand and style of machine tool has its place. Matching the machine tool to the application is critical for success. Machines get saddled with a bad reputation when they fail to perform as expected, which is pretty much guaranteed when machines are not matched with the right application.
In short, there are some basic elements to a successful machine tool purchase that some shops fail to consider.
Key Considerations
1. Price shouldn’t be the primary factor.
Try not to use price as a significant factor in the selection of the machine. Of course, most shops have budget constraints that ultimately influence purchasing decisions. Guard against the instinct to let money drive your purchase because the reality is that an expensive machine tool isn’t always the better choice, just as a less expensive machine purchased to save money could be disastrous.
2. Match the machine to the work.
Consider the type of work that is being done with the machine.
If you’re running close-tolerance aerospace parts made from expensive materials, it probably makes sense to invest in a high-end machine with features designed for producing tight-tolerance parts.
Likewise, if you’re making commodity parts with looser tolerances, then a high-end machine may not be necessary.
3. Standardize CNC controls when possible.
CNC controls are a feature that is highlighted in the selling process. However, if you have a shop full of brand X controls, it may not make sense to buy brand Y. When you buy a new control there is a learning curve that can result in training expense and lost production. Having multiple types of controls in a shop also creates a situation that limits the number of people that can use the machine. I have seen situations where “the guy” running a key piece of equipment left the company and no one else knew anything about his machine.
4. Consider tooling compatibility.
What kind of toolholders are in the shop? If the machine you’re looking to purchase has a 50-taper spindle and your existing machines all use 40-taper spindles, there will be additional costs for new toolholders.
5. Speed matters, but only if it saves you money.
Speed is another aspect of machine tools that is used to differentiate brands in the market. Things like rapid traverse rates, tool-to-tool time, processing speeds and spindle speeds all can be critical factors — but only in the right context, and depends on the work. Fast machines, like fast cars, cost more than the slow ones.
For high-volume manufacturers that make the same parts over and over, saving a few seconds per part can become significant, thereby making speed more important. On the other hand, a low-volume shop that machines specialty parts and makes a lot of setups may not realize measurable savings after purchasing speedy toolchangers and rapid traverse rates.
Shops that are machining blades for aerospace engines or making molds need CNC controls with high processing speeds to ensure the multi-axis interpolative moves are executed without hesitation. However, a shop making money on twoaxis moves like milling keyways and drilling holes simply has no need for ultra-fast processing speeds.
6. Spindle speed should match the material.
Spindle speed and cutting feed rate is dictated by the tool diameter and the raw material. Shops specializing in easier to machine materials like aluminum gain a cost benefit from high spindle speeds. Faster spindles translate into faster traverse speeds, resulting in less cost. For shops that are machining parts from tool steel, stainless steel and super alloys a machine with a high-speed spindle is not beneficial. This is because the difficult materials can’t be machined at high rpm like aluminum. Again, like cars, speed costs money so the extra cost of a highspeed spindle may not be justified.
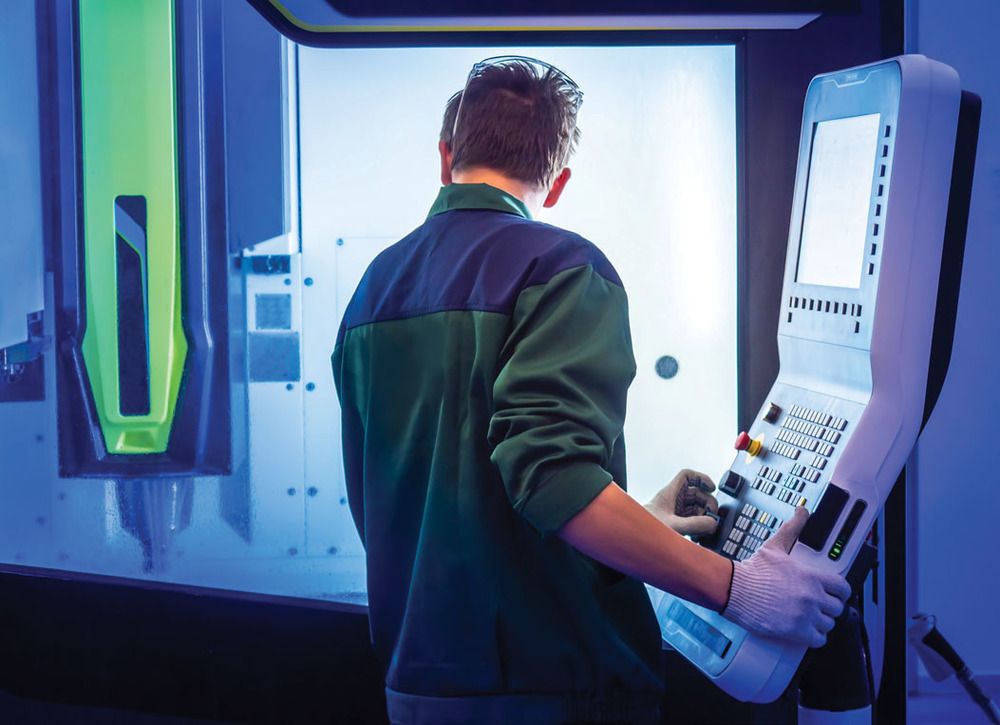
Years ago, manufacturers would use construction methods to differentiate between brands. Some older more prominent machine builders would claim they had a superior machine because of their cast iron box ways machined as part of machine’s base structure. Newer manufacturers entering the market looking to capture the small shop market for CNC machines would build linear guideway machines. Linear guides are a self-contained bearing unit that bolts onto the machine. The argument was that box way machines were stiffer so they resisted deflection and vibration better, making them capable of heavier cuts.
Box way machines are stiffer, not doubt. But in today’s machining landscape, with advances in cutting tools, newer techniques and advanced CAM software, programmers and machinists can easily overcome the deficiencies of linear guides by altering the speed, feed and depth of cut without reducing productivity.
Most people buying a full-size machining center or lathe are not using them for fun. They are using them to make money. Over investing in machine tools detracts from the money-making goal. Smart shops balance machine capabilities and features with the type of parts they make and the materials they use. A $50,000 machining center generating $100 per hour is more profitable than a $150,000 machining center making $100 per hour.
Don’t get caught up in the banter about spindles, guideways and speeds. Select the machine that is appropriate for the job and can maximize your profitability.
Related Glossary Terms
- alloys
alloys
Substances having metallic properties and being composed of two or more chemical elements of which at least one is a metal.
- computer numerical control ( CNC)
computer numerical control ( CNC)
Microprocessor-based controller dedicated to a machine tool that permits the creation or modification of parts. Programmed numerical control activates the machine’s servos and spindle drives and controls the various machining operations. See DNC, direct numerical control; NC, numerical control.
- computer-aided manufacturing ( CAM)
computer-aided manufacturing ( CAM)
Use of computers to control machining and manufacturing processes.
- depth of cut
depth of cut
Distance between the bottom of the cut and the uncut surface of the workpiece, measured in a direction at right angles to the machined surface of the workpiece.
- feed
feed
Rate of change of position of the tool as a whole, relative to the workpiece while cutting.
- gang cutting ( milling)
gang cutting ( milling)
Machining with several cutters mounted on a single arbor, generally for simultaneous cutting.
- lathe
lathe
Turning machine capable of sawing, milling, grinding, gear-cutting, drilling, reaming, boring, threading, facing, chamfering, grooving, knurling, spinning, parting, necking, taper-cutting, and cam- and eccentric-cutting, as well as step- and straight-turning. Comes in a variety of forms, ranging from manual to semiautomatic to fully automatic, with major types being engine lathes, turning and contouring lathes, turret lathes and numerical-control lathes. The engine lathe consists of a headstock and spindle, tailstock, bed, carriage (complete with apron) and cross slides. Features include gear- (speed) and feed-selector levers, toolpost, compound rest, lead screw and reversing lead screw, threading dial and rapid-traverse lever. Special lathe types include through-the-spindle, camshaft and crankshaft, brake drum and rotor, spinning and gun-barrel machines. Toolroom and bench lathes are used for precision work; the former for tool-and-die work and similar tasks, the latter for small workpieces (instruments, watches), normally without a power feed. Models are typically designated according to their “swing,” or the largest-diameter workpiece that can be rotated; bed length, or the distance between centers; and horsepower generated. See turning machine.
- machining center
machining center
CNC machine tool capable of drilling, reaming, tapping, milling and boring. Normally comes with an automatic toolchanger. See automatic toolchanger.
- milling
milling
Machining operation in which metal or other material is removed by applying power to a rotating cutter. In vertical milling, the cutting tool is mounted vertically on the spindle. In horizontal milling, the cutting tool is mounted horizontally, either directly on the spindle or on an arbor. Horizontal milling is further broken down into conventional milling, where the cutter rotates opposite the direction of feed, or “up” into the workpiece; and climb milling, where the cutter rotates in the direction of feed, or “down” into the workpiece. Milling operations include plane or surface milling, endmilling, facemilling, angle milling, form milling and profiling.
- rapid traverse
rapid traverse
Movement on a CNC mill or lathe that is from point to point at full speed but, usually, without linear interpolation.