Since the beginning of the pandemic, we’ve learned a lot about the supply chain and global trade — more than most of us ever wanted to know. A simple, significant lesson learned about the supply chain is that China/Asia is far away, not only in terms of physical distance but culturally and governmentally.
With distance comes risk. We’ve had an opportunity to learn how cultural differences and governmental policies can dramatically affect the supply chain. COVID-19 tactics employed across the globe differed greatly and created vastly different supply chain and economic impacts.
China’s ability to operate was severely hampered by its Zero-COVID policy, which resulted in swaths of the country being completely idled for two to eight weeks at a time. Then the pendulum there swung to the other extreme as the country quickly reopened and vast numbers of people contracted the coronavirus. As this article is being written in late January, Chinese businesses again are shut down but this time due to illness, not government-imposed closures.
A potentially scarier disruption to the supply chain, however, has yet to play out in the South China Sea. Chinese President Xi Jinping has made it clear that in the medium to long run Taiwan will be reunited with mainland China. It’s important to understand that for several centuries Taiwan was part of China. Only in the mid-20th century did Taiwan declare independence. Given Xi’s public comments, it would certainly seem that he would like to be the architect of reuniting the mainland with Taiwan. That puts a five-to-10-year window on that happening, given Xi’s likely tenure. It’s worth noting that Russian President Vladimir Putin clearly stated his ambitions regarding Ukraine up to 20 years prior to invading the nation. How China goes about trying to reunify could have major implications for the global supply chain. Hopefully, Xi will use a carrot over a stick to draw Taiwan back.
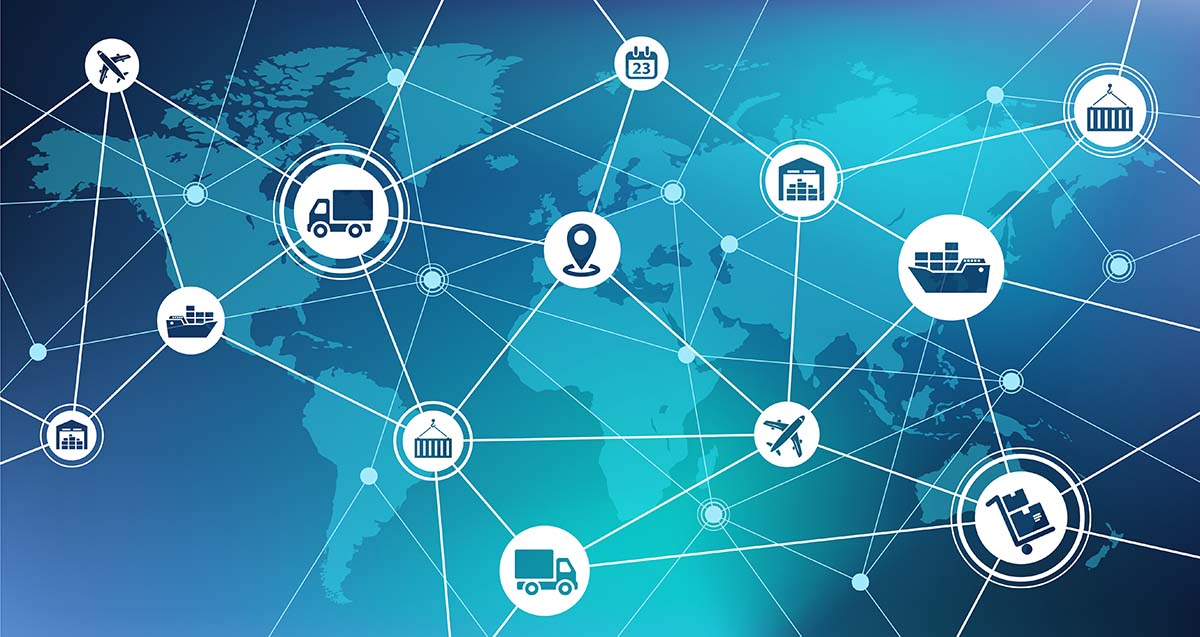
Federal Policies
Another government-inflicted problem for the supply chain — this time by the United States — is from the Section 232 and 301 tariffs. In addition to them, subsequent quotas disrupted trade flows for steel and so much more. The biggest problems with tariffs and quotas is how inefficient and costly they are. In the case of Section 232 tariffs, all that was accomplished was to punish U.S. manufacturers, other than steel and aluminum producers. Many types of steel products that are unavailable in the U.S. are subject to tariffs and quotas. The exclusion process took several years to function somewhat effectively. Even today, inefficiencies and opportunities for abuse in the exclusion process continue to add costs for U.S. manufacturers. Essentially, the government has collected tariffs and U.S. manufacturers have not been globally competitive due to paying a 25% or higher premium over competitors.
Fallout
Like the arcade game Whac-a-Mole, the supply chain has adapted to the West Coast port problems of 2021 and early 2022. Many ports in Texas, Florida and the East Coast have enjoyed increased activity as businesses have diverted shipments away from Southern California. In all likelihood, some of that shift will be permanent. It appears clear that companies became too dependent on SoCal ports. With a West Coast longshoremen contract still in limbo as of this writing, I’m sure that some businesses will continue to minimize their risk by using alternate ports.
Meanwhile, reshoring is happening and affecting the global supply chain. The Reshoring Institute estimates that 1,312,000 jobs have returned to the U.S. since 2010 — 350,000 in the past year alone. For most of us in manufacturing, we experienced 30 years of jobs being exported from the U.S. During that time, we were able to basically import disinflation. By taking advantage of cheap Chinese labor, we could keep inflation down. That situation was primarily due to the Chinese economic miracle. No country in all of history has ever grown its economy like China did in the past three decades. That success, though, has led to a tenfold increase in wages there. The cheap labor party is over.
Lessons
The pandemic has reminded us that there is great risk to the economy of a country when it loses the ability to make things domestically.
Our economic integration with China has substantial long-term implications. There is no quick fix, and any suggestion that we must significantly curtail trade with China would be lunacy. If we are going to permanently reverse the trend of offshoring, several things need to be addressed.
First, we need a more integrated manufacturing policy. Again, our approach has been Whac-a-Mole: Put in tariffs to support the steel and aluminum industries, and subsidize the solar panel industry, the electric vehicle industry and semiconductor manufacturing. All these one-off bills do not make a comprehensive manufacturing policy. Many countries have well-thought-out, integrated industrial policies. Unfortunately, the U.S. does not.
Second, this country must fix the immigration system. This is not a partisan issue. We are a country of immigrants that has no idea how to handle immigrants. We need to secure our borders and come up with a process to help immigrants obtain permanent legal status. They may well help fill many unfilled U.S. jobs.
Third, we need to invest in talent development. If we are going to bring back high-paying manufacturing jobs, we must have people with the right skill sets. Much like the three-decade-long export of manufacturing jobs to Asia, we have spent three decades not supporting people who work with their hands. Our educational system is pushing far too many toward college, and society does not encourage or recognize the value of people working with their hands to manufacture products or provide services.
Finally, any discussion of supply chain issues should address being prepared for the next “black swan” event. It seems that in recent years we’ve had to deal with a whole flock of black swans: the Great Recession in 2008, the pandemic in 2020 and the Russian invasion of Ukraine a year ago. These ominous events seem to be coming faster and faster. Will the next be an invasion of Taiwan, a nuclear weapon going off in Ukraine or something completely different? Regardless of what the next black swan is, it will require businesses and governments to flexibly work together.
While I’m critical of the Federal Reserve being overly aggressive with its interest rate decisions in the past year, one positive takeaway is that a recession would allow the supply chain to catch up. We’ve already seen the cost of moving a container from China to the U.S. drop from up to $20,000 per container back toward a pre-pandemic cost of about $2,500. This year, I expect the supply chain to catch up slowly but surely. That should lead us to the next upturn, which begs several questions:
Can ports handle increased volumes?
- Will employers be able to find enough people to handle an uptick in 2024 or 2025?
- Will there be enough trucks and rail cars to move products?
- Will COVID-19 still result in local shutdowns?