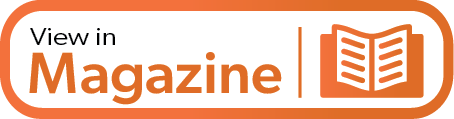
System 3R, part of GF Machining Solutions, introduced its latest breakthrough in manufacturing automation at IMTS 2024 with the debut of Autonomous Mobile Robot (AMR). Designed to enhance flexibility and efficiency in lights-out manufacturing, the AMR builds on System 3R’s decades of experience in automation and tooling innovation.
System 3R’s journey in automation began in 1967 in Stockholm, Sweden, with the development of a high-precision tooling system. This system allowed parts to move seamlessly between different machine operations — such as milling, turning, grinding, and lathing — with a repetition accuracy within 2 μm.
Two decades later, the company introduced robots to automate processes during nights and weekends, significantly improving productivity. The AMR represents the next step in this evolution, enabling flexible movement of large fixtures and pallets across multiple cells within a factory.
Unlike traditional Automated Guided Vehicles (AGVs), which rely on fixed paths embedded in the floor, the AMR is equipped with advanced mapping and obstacle avoidance technology.
Dynamic Navigation: The AMR uses a virtual map to navigate factory floors in real time. If an obstacle appears, it intelligently reroutes to its destination.
Real-Time Monitoring: Operators can view the AMR’s movements and status in real time using System 3R’s Workshop Manager software.
Integrated Software: The Workshop Manager Version 5 ensures that the correct pallets and fixtures are delivered to the right machines at the right time, coordinating multiple systems from various OEMs.
The AMR is designed to meet the needs of manufacturers of all sizes:
- For Small Shops: The AMR can begin with a single machine, providing an entry point for businesses new to automation.
- For Large Facilities: The AMR can scale to support linear cells with up to 20 machines, extending its reach with rail-mounted configurations to automate entire production lines.
Applications in Lights-Out Manufacturing
The AMR fits perfectly within the growing trend of lights-out manufacturing, where machines operate autonomously with minimal human intervention. Its ability to transport fixtures between cells, such as milling and grinding stations, ensures uninterrupted production, even in complex workflows.
For more information, visit System 3R’s website or explore their solutions in person at upcoming industry events.
Related Glossary Terms
- gang cutting ( milling)
gang cutting ( milling)
Machining with several cutters mounted on a single arbor, generally for simultaneous cutting.
- grinding
grinding
Machining operation in which material is removed from the workpiece by a powered abrasive wheel, stone, belt, paste, sheet, compound, slurry, etc. Takes various forms: surface grinding (creates flat and/or squared surfaces); cylindrical grinding (for external cylindrical and tapered shapes, fillets, undercuts, etc.); centerless grinding; chamfering; thread and form grinding; tool and cutter grinding; offhand grinding; lapping and polishing (grinding with extremely fine grits to create ultrasmooth surfaces); honing; and disc grinding.
- milling
milling
Machining operation in which metal or other material is removed by applying power to a rotating cutter. In vertical milling, the cutting tool is mounted vertically on the spindle. In horizontal milling, the cutting tool is mounted horizontally, either directly on the spindle or on an arbor. Horizontal milling is further broken down into conventional milling, where the cutter rotates opposite the direction of feed, or “up” into the workpiece; and climb milling, where the cutter rotates in the direction of feed, or “down” into the workpiece. Milling operations include plane or surface milling, endmilling, facemilling, angle milling, form milling and profiling.
- turning
turning
Workpiece is held in a chuck, mounted on a face plate or secured between centers and rotated while a cutting tool, normally a single-point tool, is fed into it along its periphery or across its end or face. Takes the form of straight turning (cutting along the periphery of the workpiece); taper turning (creating a taper); step turning (turning different-size diameters on the same work); chamfering (beveling an edge or shoulder); facing (cutting on an end); turning threads (usually external but can be internal); roughing (high-volume metal removal); and finishing (final light cuts). Performed on lathes, turning centers, chucking machines, automatic screw machines and similar machines.