When marking parts, multiple methods are available. When marking medical devices, especially metal implantable ones, a laser is the primary tool, according to Andrew Bourgoine, co-president and vice president of sales for Geo. T. Schmidt Inc. In addition to fiber, ultraviolet, carbon dioxide and green laser marking equipment, the manufacturer of marking systems offers options for dot peen marking; scribe marking; handheld inkjet printing; and traditional marking, including roll, rotary roll, press and steel stamps.
Dot peening has a limited place in marking medical devices, he noted, but only for items that do not go in the body, such as oxygen tank cylinders and pipes at a medical facility that are marked to assist maintenance personnel.
Although CO2 lasers are mainly for marking organic material, such as glass and wood, as well as plastics and other non-metallic materials, Bourgoine said fiber lasers are suitable for marking metal. UV lasers are for plastic, while green lasers are ideal for heat-sensitive materials, including those with reflective surfaces, delicate plastics and soft or sensitive components. For example, a large medical supply company “cold marks” plastic parts with a UV laser because the wavelength and heat from a fiber laser would melt the plastic.
To mark medical instruments and devices made of stainless steel, Bourgoine recommends using a fiber laser and creating a heat mark, which is also known as carbon migration or laser annealing. The heat from the laser during this thermos-chemical reaction alters the color of the material, resulting in a visible mark without the displacement of any material. “We are raising the carbon up out of the stainless steel, so we’re not really engraving the material. This is particularly important for medical components, where surface integrity must be preserved to deter the growth of bacteria.”
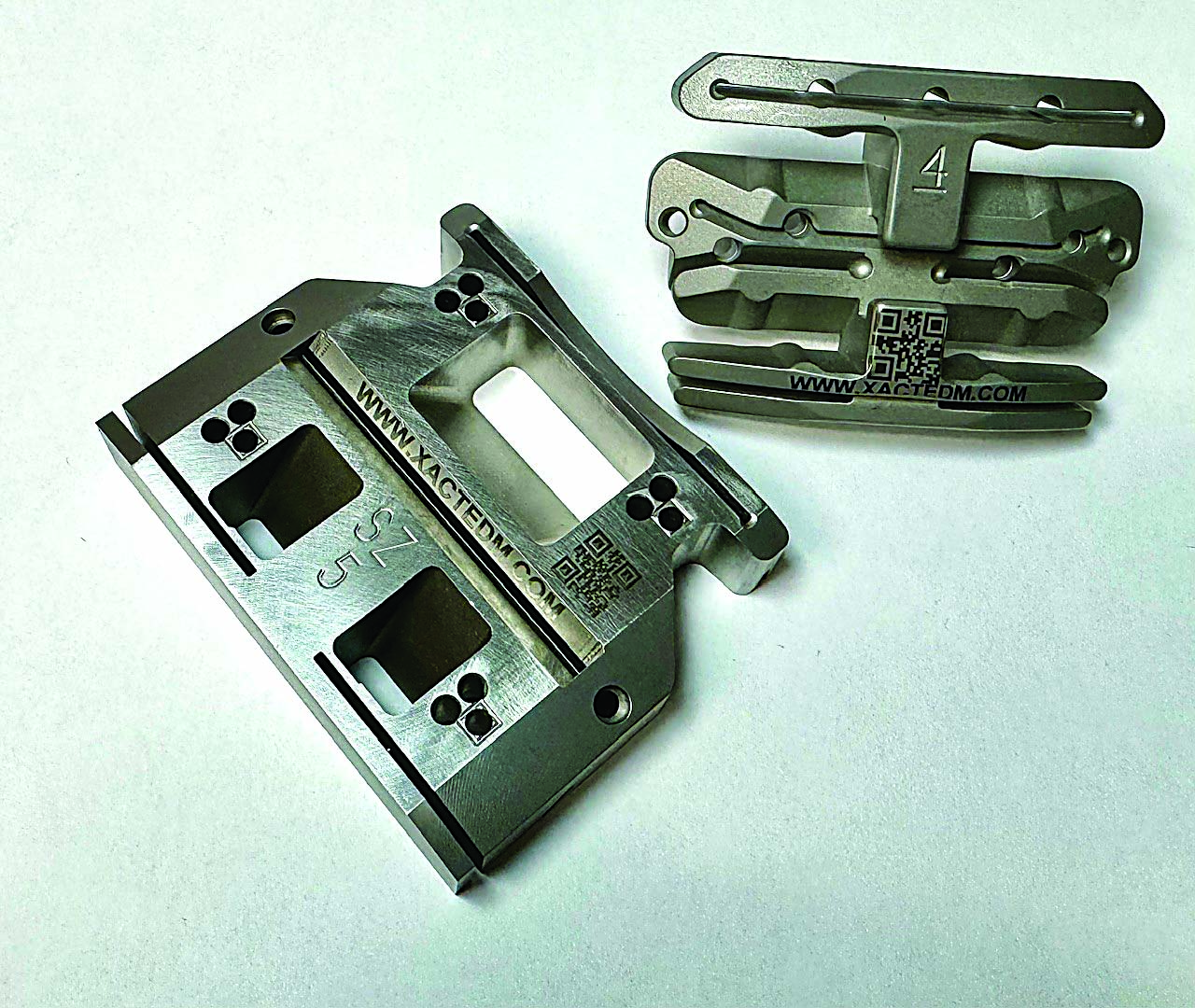
The company, which was founded in 1895, reports that other types of marks include laser etching, or ablation, and engraving. The former displaces very little material, and the marking depth can be as little as 0.0254 mm (0.001") and often involves removing a topcoat, such as an anodized laser, to expose material. Engraving goes deeper and is suitable for parts that experience a lot of wear, are exposed to extreme temperatures or undergo a post-processing step such as painting.
Bourgoine noted that GT Schmidt targets its marking system sales — of which medical customers account for 5% to 10% — to OEMs and suppliers to OEMs. “We really don’t supply machines to anybody that is doing contract marking.”
X Marks the Spot
Xact Wire EDM Corp. in Waukesha, Wisconsin, was started in 1984 to provide wire EDM and small-hole EDM services to customers across the U.S. A second facility was added in 1994 in Cary, Illinois. Both locations began offering laser marking services as a value-added service to complement the wire and small-hole EDM services, said Michael Raasch, business development. Xact’s customers include many medical companies that may require laser part marking as a secondary process to wire EDMing.
“Some of our projects include such items as identification with bar codes, QR codes, logos, serial numbers, patent numbers, date codes and more,” Raasch said.
Each of the company’s locations has a Zetalase fiber laser marking machine with a rotary device for 360° marking and a Minilase XL20 fiber laser marking machine.
The medical components that Xact has machined include tibial cut guides, resection cut blocks, laparoscopic graspers and forceps, bone plates, surgical needles, and alignment guides. The workpiece materials are metal because they need to be conductive for
EDMing and include titanium, medical-grade stainless, platinum, tungsten and Nitinol. “We’re set up primarily to do laser marking on metal and not plastic. Those types of jobs we would ‘no quote.’”
Xact does not target medical OEMs, who are often served by Tier 1 manufacturers, Raasch said. “Those [Tier 1 manufacturers] would be the companies that we are better suited to work with, because they’re full-service machine shops. They have the connection to the OEMs, and then a lot of times they have EDMs in-house, but they offload work to us when they’re super busy or it’s a tricky part or something that they’re not familiar with.”
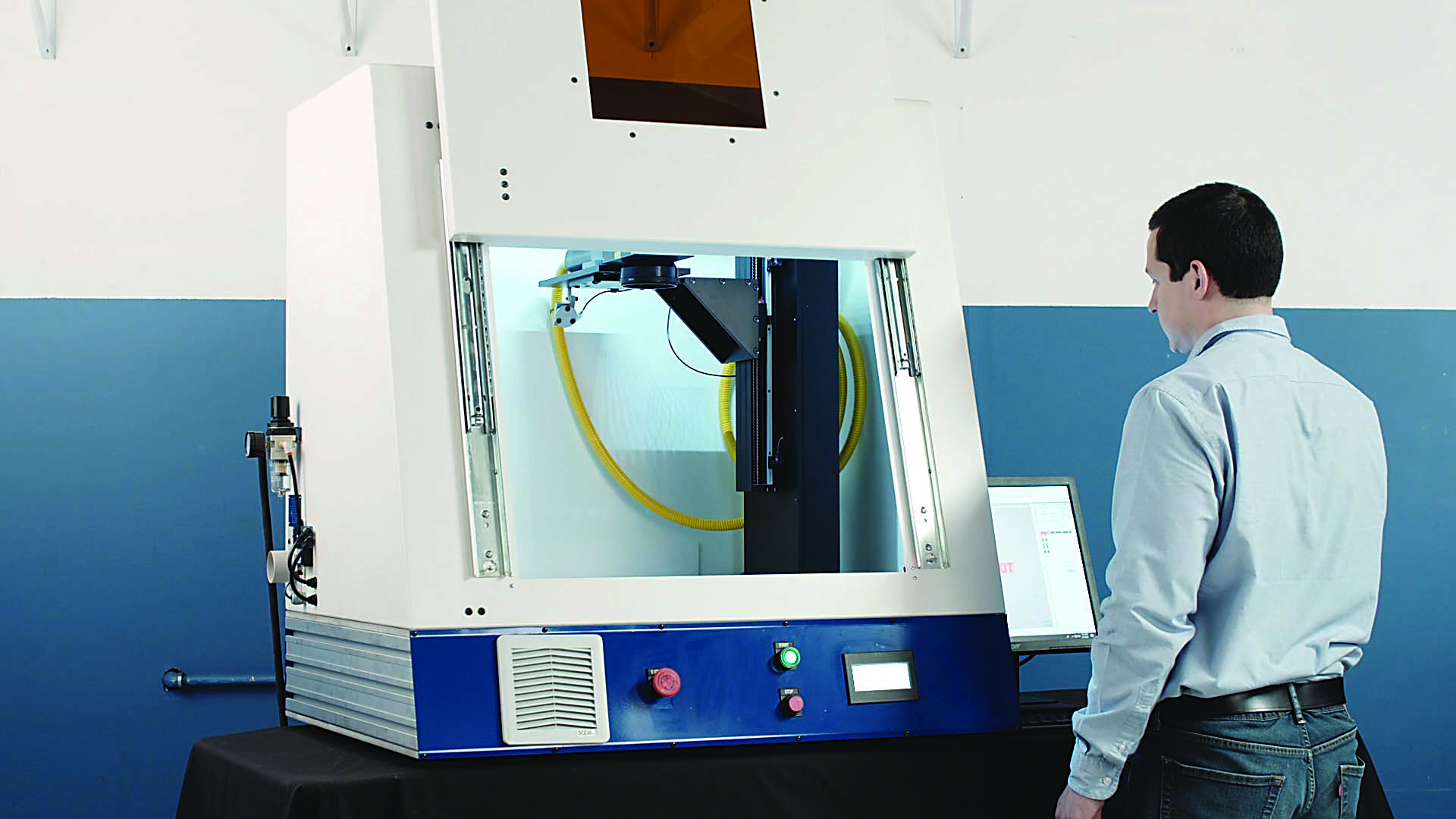
Most of the medical marking Xact performs is for instruments and components used externally on a patient, Raasch explained. The company has laser-marked some implants, but those are determined on a case-by-case basis where the risk factor and level of liability play significant roles. The considerations include whether the part is for an implant or instrument, the workpiece material, the type of mark, and whether the part will fit in the marking machine.
“Those would be all the boxes we’d have to check off to look at a project for marking,” he said. “We’d have to make sure that it’s a good process or a good part for us. We may just ‘no quote’ it because there’s too much risk versus the reward.”
Compared to laser engraving, which creates marks 0.0762 mm to 0.127 mm (0.003" to 0.005") deep, he said the laser marking Xact performs is shallow at 0.0254 mm to 0.0508 mm (0.002") deep. With an engraving, someone can run a fingernail along the marking and feel the depth. “That’s not what we do. We’re more at the surface.”
Permanent Traceability
Because it is critical to trace a medical device from its inception until it has been fully used, Conroe, Texas-based Technomark North America focuses its expertise on building permanent marking and industrial traceability equipment, said Justine Fayolle, marketing and communication manager, who is based in La Talaudière, France. The company offers dot peen and laser marking machines.
Dot peen technology has its place in making medical devices, such as creating an alphanumeric code or logo, and is relatively low cost, but a laser produces a more aesthetically pleasing mark that is quicker to achieve, she said. “If you have to make a beautiful logo on a product, for example, I think the best solution is with the laser marking machine. If you want to mark a data matrix, you can choose the dot peen marking machine because it also makes permanent markings that can be read by a smartphone or a reader. Both solutions are suitable for the medical sector.”
More and more medical customers are marking parts with codes to ensure traceability, Fayolle noted, and a large portion are data matrix codes to integrate more data. These familiar 2D codes consist of black and white cells, or dots, arranged in a rectangular or square pattern. Other common markings include alphanumeric codes, logos, time stamps and bar codes.
She added that Technomark offers 20-, 30- and 50-watt fiber lasers that allow the marking speed and depth of the mark to be changed. Being able to adjust laser settings is particularly beneficial when marking plastics, rubber and elastomers, which have a lower melting point than metal. Low power and high speed are needed to create a more controlled “micro-burn” on the surface without melting the part or compromising its integrity.
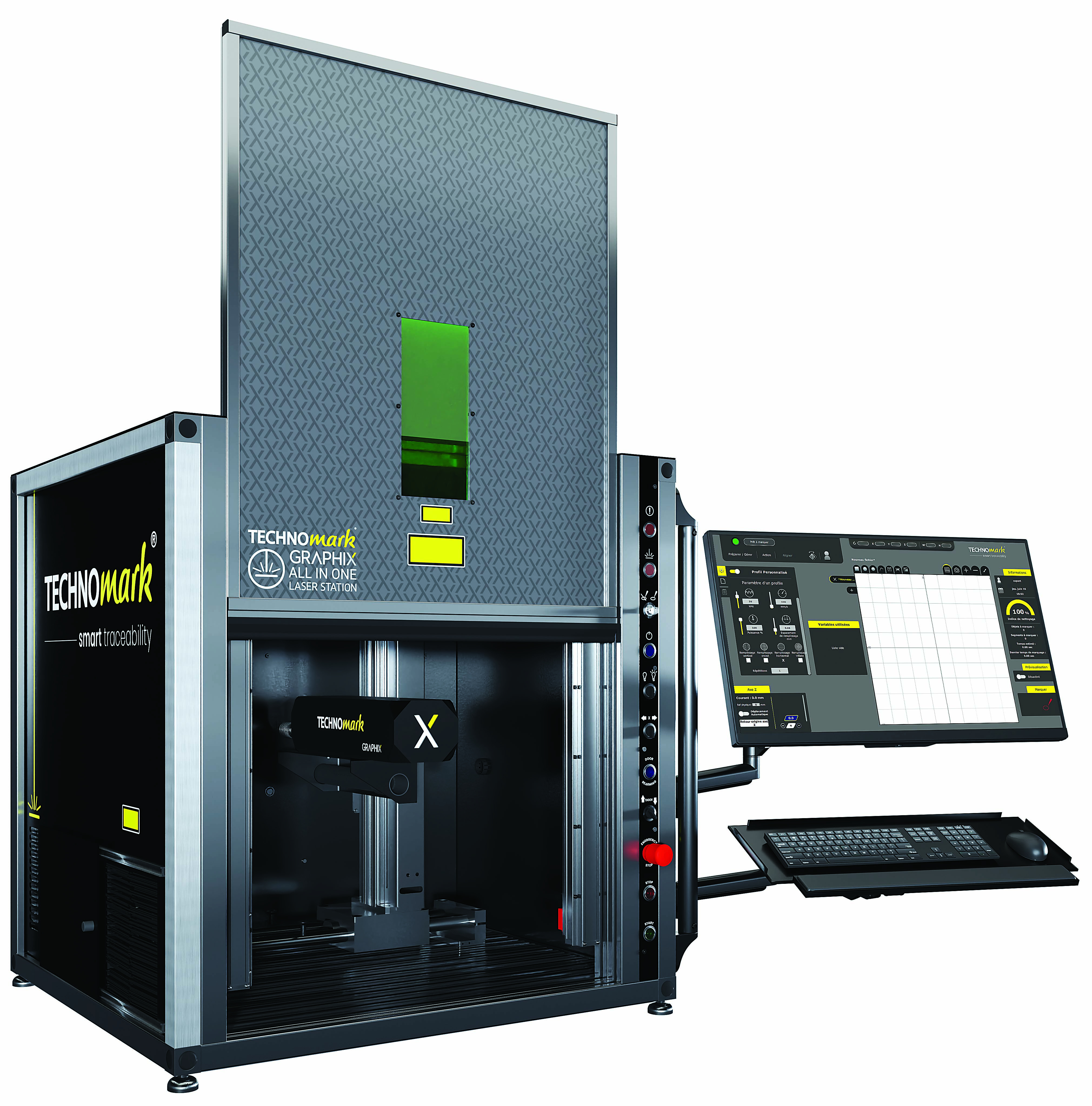
Other types of markings include general, annealing, ablating and deep engraving, the company reports. General marking is the most common, with its ease of programming and creation of extremely durable marks. As previously noted, annealing is used when no visible surface disruption is required. The material is heated by the laser beam to create a dark or burned mark that’s smooth to the touch. Because no physical disruptions occur so the surface does not present any holes or cavities that could retain bacteria, this method is often used to mark surgical tools and implants. Ablating removes some of the surface coating to reveal the underlying material and creates different levels of contrast between the mark and unaffected areas. In addition, deep engraving generally employs a high-powered fiber laser to mark various materials, including rubber and metal. The depth is a function of the laser’s power, speed and repetition rate, or how many pulses per second.
Fayolle said Technomark’s Graphix laser marking system is targeted for low-volume, high-matrix jobs because of its adaptability and flexibility. The system comes standard with two F-theta lens options for a customized marking area size, the ability to mark pieces with dimensions up to 500 mm × 500 mm × 400 mm (19.68" × 19.68" × 15.75"), and an integrated PC with keyboard, mouse and monitor.
One available option is the rotating axis accessory to mark parts with a variety of shapes, which is also suitable for dot peening. “With a rotating axis,” she said, “you can mark on the generator, and you can also mark on the circumference of the parts.”
To integrate laser marking technology into an automated production environment, Technomark offers the Graphix Inline machine. In addition, the company introduced the Graphix Plus all-in-one marking station with a motorized door, on-board camera and intuitive software. The company-developed software enables an ergonomic interface with two operating modes: one for creation of marking files with simplified settings for novice users or advanced settings for experts, and one for production with variable filing and preconfigured files marking to optimize productivity and reduce the risk of errors. “Our machine can make the settings for you with the very easy-to-use software,” Fayolle said.
Not on the Shelf
In addition to standard offerings, Fayolle said Technomark produces custom marking machines for special applications, with options available to enhance automation, assist with part loading and make marking easier. “It’s not rare that we need to create a different machine because of the size of the parts to be marked.”
Bourgoine emphasized that Schmidt is also a marking machine manufacturer that specializes in developing systems that fit customers’ needs. “We offer a wide range of technologies, focusing on solving customer application needs with the right equipment. And because we design and manufacture everything in-house, we can customize any of our standard machines to provide the best possible solution.”
Because part manufacturers often struggle with attracting and retaining employees, they frequently seek to automate equipment while repurposing workers to areas and operations that cannot be automated, he added. “Labor shortage is a battle many are facing, which is why we are often asked to help automate in certain situations.”
Bourgoine distinguishes between marking machine users and operators. A user performs the programming, adjusts the settings and takes similar actions, while an operator pulls up a program file, puts a part into the machine and presses the start button. “A door is going to close, [the laser] is going to mark, the door is going to open, they’re going to pull [the part] out, rinse and repeat.”
This arrangement restricts the human element when inputting data, such as having an operator entering a “B” instead of [the number] eight or an “O” instead of a zero, he said. “There’s no input by the operators and that’s how we’re setting these systems up.”
Whether it is a standard or special machine, Bourgoine said a fiber laser is rated to last around 100,000 marking hours. “Depending on the usage, I’ve seen folks go seven to 20 years.” In addition, it depends on how well a machine is maintained, similar to caring for a car. “If you don’t maintain your car, it’s going to break down and have trouble a lot faster than if you maintain it.”
Contact Details
Contact Details
Contact Details
Related Glossary Terms
- annealing
annealing
Softening a metal by heating it to and holding it at a controlled temperature, then cooling it at a controlled rate. Also performed to produce simultaneously desired changes in other properties or in the microstructure. The purposes of such changes include improvement of machinability, facilitation of cold work, improvement of mechanical or electrical properties and increase in stability of dimensions. Types of annealing include blue, black, box, bright, full, intermediate, isothermal, quench and recrystallization.
- electrical-discharge machining ( EDM)
electrical-discharge machining ( EDM)
Process that vaporizes conductive materials by controlled application of pulsed electrical current that flows between a workpiece and electrode (tool) in a dielectric fluid. Permits machining shapes to tight accuracies without the internal stresses conventional machining often generates. Useful in diemaking.
- filing
filing
Operation in which a tool with numerous small teeth is applied manually to round off sharp corners and shoulders and remove burrs and nicks. Although often a manual operation, filing on a power filer or contour band machine with a special filing attachment can be an intermediate step in machining low-volume or one-of-a-kind parts.
- peening
peening
Mechanical working of a metal by hammer blows or shot impingement.
- wire EDM
wire EDM
Process similar to ram electrical-discharge machining except a small-diameter copper or brass wire is used as a traveling electrode. Usually used in conjunction with a CNC and only works when a part is to be cut completely through. A common analogy is wire electrical-discharge machining is like an ultraprecise, electrical, contour-sawing operation.
Contributors
Geo. T. Schmidt Inc.
847-647-7177
www.gtschmidt.com
Technomark North America
888-610-0151
www.technomark-inc.com
Xact Wire EDM Corp.
800-798-9228
www.xactedm.com