When trying to have the most advanced manufacturing possible and buying new machines that are extremely complex, forward thinking is better.
Weiss Watch Co. combines traditional Swiss watchmaking techniques with advanced manufacturing technologies to produce heirloom-quality timepieces that are built to last. Using Swiss-style machine tools powered by Hexagon’s Esprit CAM software from North Kingstown, Rhode Island-headquartered Hexagon’s Manufacturing Intelligence div. enables the company to manufacture components more efficiently while honoring traditional craftmanship.
Long before he helmed the business that bears his name in Nashville, Tennessee, Cameron Weiss of Weiss Watch was a born engineer.
“I built a lot of different things as a kid but gravitated toward watches because I liked the technical aspect and their mechanical nature,” Weiss said.
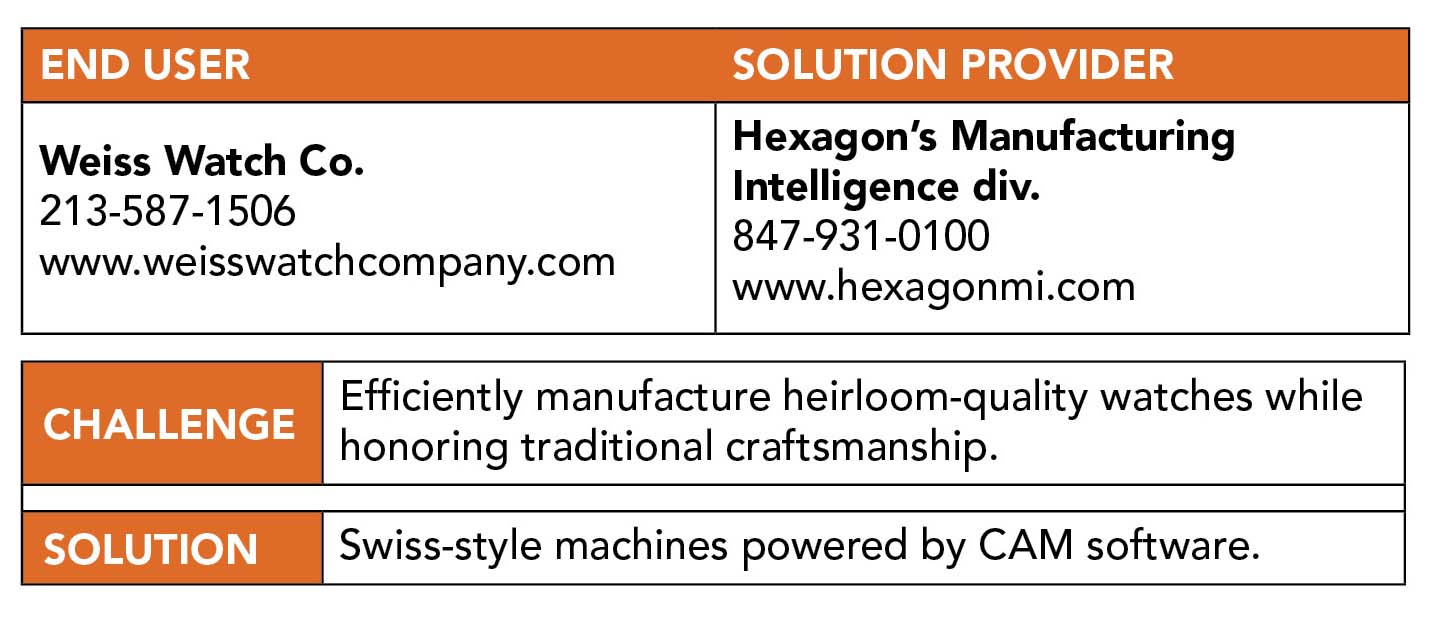
His enduring interest in timepieces led to his enrollment in a school operated by Swatch Group, which offers a Swiss-style curriculum dedicated to the repair and restoration of watches sold in the U.S. He then worked in Europe for watchmakers Vacheron Constantin and Audemars Piguet.
While his goal was to establish his own watchmaking business, Weiss believed that he’d have to relocate to Switzerland to make his dream come true. Upon returning to the U.S., however, he found that there was interest in domestically produced watches made by small companies that provide opportunities for customers to interact with brand founders and designers.
“I learned that people are willing to spend more knowing that a watchmaker designed and made the product in the U.S.,” Weiss said. “I realized we could use advanced manufacturing technology to keep costs attainable while producing watches of the same quality as Swiss watch brands.”
To learn more about manufacturing, and specifically how to operate CNC machinery and CAM software, he joined a company in Los Angeles that produces housings for underwater cameras.
Weiss designed and produced components for his first 10 watches in 2013 with the help of local prototype manufacturers and assembled the watches in his apartment. Those first 10 pieces sold within a month and the rest, as they say, is history. Weiss eventually established the small shop where he designs, manufactures and assembles purely mechanical timepieces.
“I’m producing wristwatches that are more attainable and trying to bring the mechanical side of watches to more people,” he said.
As a production team of one, Weiss was challenged with figuring out how to efficiently perform what amounts to three different jobs without hiring anyone. For several years, he outsourced the production of some components and produced what he could using a Swiss-style lathe and a two-axis mill with 2+1-axis positional machining capabilities.
While he doesn’t produce components in volume or require high throughput, Weiss does require adherence to tight tolerances and fine surface finishes. Lights-out machining is his objective.
“I don’t want to fill the shop up with people who just move parts to different machines,” he said. “Manufacturing a watch case is typically done by stamping out a blank, then taking that blank and putting it on a CNC lathe to cut the internal diameters before switching it over to a mill to cut the exterior shape. This requires three different processes performed by three different types of manufacturing professionals.”
To increase his production capabilities, Weiss acquired a Chiron mill-turn machine tool with a bar feeder that offers five-axis milling and Swiss-style turning capabilities. To program the new machine tool, he implemented Esprit CAM software because of its ability to accurately program complicated multiple-axis and multitasking machine tools, specifically Swiss-style lathes.
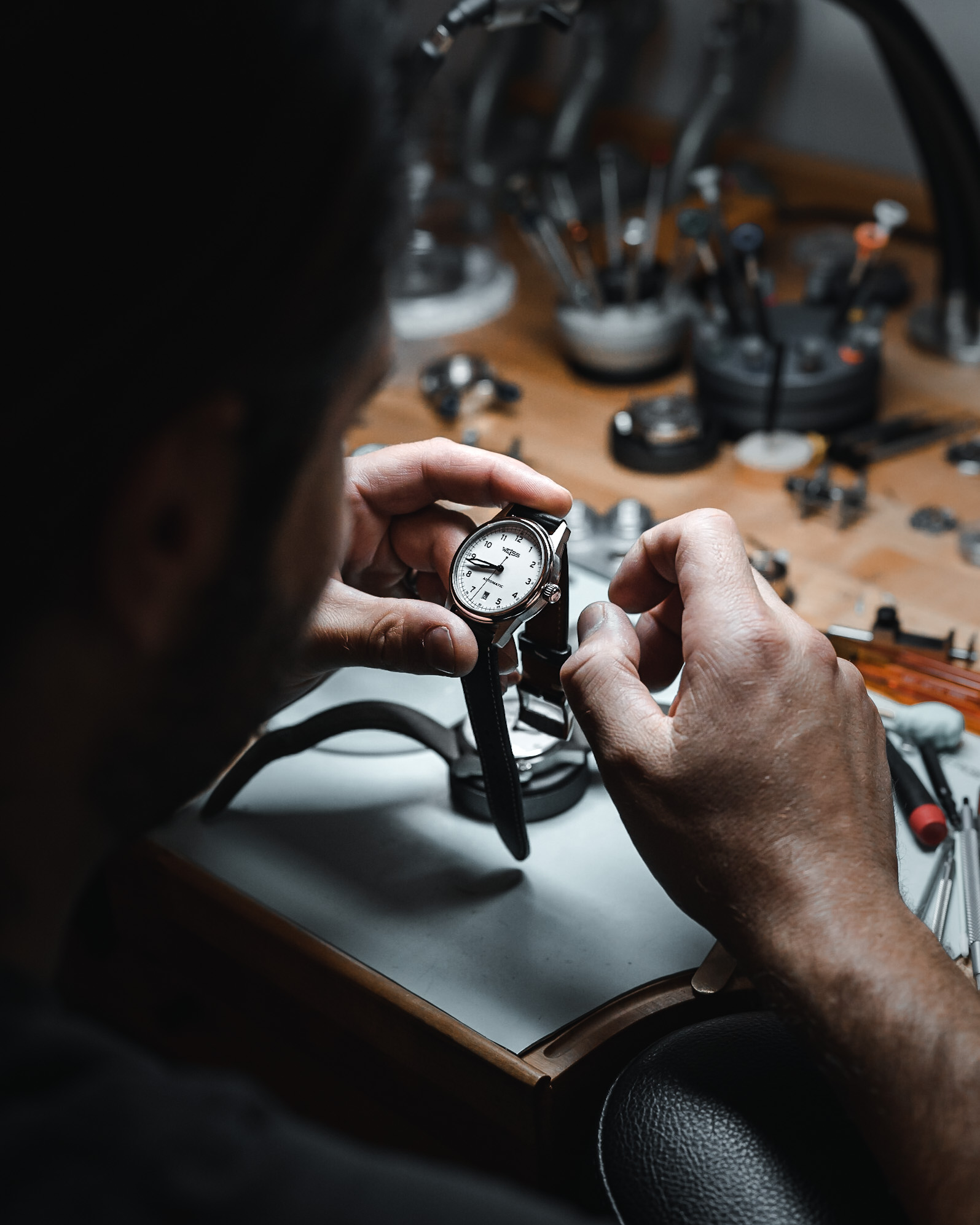
“It seems like Esprit is more focused on improving Swiss programming than other CAM developers,” Weiss said. “I also didn’t want to have to use multiple solutions to program our machine tools, and it’s able to program all of the machinery in my shop.”
Swiss-style lathes make it much easier to machine especially small, thin parts, as well as components that are significantly longer than they are wide. The stock material on Swiss-style lathes emerges from a guide bushing to be machined by tools at the face of the bushing. The material moves in and out of the bushing throughout the machining operation, which enhances part stability.
“The benefit of a Swiss lathe is that very thin parts won’t deflect when the cutting tool touches them because you’re cutting right where it’s being held rather than from 10 mm away on a part that’s only one tenth of a millimeter in diameter,” Weiss explained. “Our thickest watch case is still under 11 mm. The majority of the watch is made with turning and you have a lot of small parts like screws, pinions and wheels that are all cut on Swiss machines.”
Weiss’s Chiron machine tool is equipped with a B-axis head that offers “swivel capability” for flexible machining of the top side and full front face of the bar. It’s also equipped with a vice that grabs and holds the part while the spindle is used as a saw for parting off. The vice then flips back around so that the back of the bar can be machined.
“We do a lot of hobbing and broaching, as well as some tooth profiles and castle-type face gears. This involves machining on many faces of the part in a tiny area with weird profiles and oddball tooling that make the programming nearly impossible.”
Prior to using Esprit to program the new Chiron machine tool, tests were performed to ensure that the toolpath generated by the software would work flawlessly with the machine-specific post processor.
“Both companies were great,” Weiss said. “Esprit sent an engineer to Chiron to run some test programs on the machine and to make sure that everything was operating as expected.”
Weiss relies on the Esprit digital twin to paint an accurate picture of how each machining operation will play out. The twin details the machine tool, stock and vendor-specific data for cutting tools, toolholders and workholders. The software’s simulation capabilities are based upon the accuracy of this digital twin and are enhanced by machine-aware artificial intelligence. Its patent-pending AI engine represents a change in the way that CNC machines are driven, as it uses AI to simplify programming, increase tool life and improve machine performance.
“The Chiron machine is all modeled up in Esprit and the simulation is very helpful because we’re dealing with such tiny areas and tight tolerances that visualization helps tremendously in making sure that nothing’s going to crash,” Weiss said. “With Swiss machines, the movements are so tiny that it doesn’t look like they’re even running. You just see oil spraying and it looks like nothing’s moving and then, all of a sudden, a little screw or a pinion comes out.”
Weiss can cut 60 watch cases from a single piece of stainless steel or titanium bar stock and perform a significant amount of work on one machine tool with limited monitoring. With five-axis capabilities, he can develop more complex case geometry that couldn’t be machined on his existing equipment or outsourced due to prohibitive costs. The addition of the Chiron enables Weiss to be more competitive, produce nearly all components in-house and offer case-making services for watch companies with limited equipment.
Use of the Chiron mill-turn has also eliminated the laborious setups required for performing multiple operations on different machines. Pairing the complex machinery with Esprit ensures that Weiss can machine with confidence.
“Esprit seems more forward thinking on the technology side and when you’re trying to have the most advanced manufacturing possible and buying brand new machines that are extremely complex, forward thinking is better.”
Contact Details
Related Glossary Terms
- broaching
broaching
Operation in which a cutter progressively enlarges a slot or hole or shapes a workpiece exterior. Low teeth start the cut, intermediate teeth remove the majority of the material and high teeth finish the task. Broaching can be a one-step operation, as opposed to milling and slotting, which require repeated passes. Typically, however, broaching also involves multiple passes.
- bushing
bushing
Cylindrical sleeve, typically made from high-grade tool steel, inserted into a jig fixture to guide cutting tools. There are three main types: renewable, used in liners that in turn are installed in the jig; press-fit, installed directly in the jig for short production runs; and liner (or master), installed permanently in a jig to receive renewable bushing.
- computer numerical control ( CNC)
computer numerical control ( CNC)
Microprocessor-based controller dedicated to a machine tool that permits the creation or modification of parts. Programmed numerical control activates the machine’s servos and spindle drives and controls the various machining operations. See DNC, direct numerical control; NC, numerical control.
- computer-aided manufacturing ( CAM)
computer-aided manufacturing ( CAM)
Use of computers to control machining and manufacturing processes.
- gang cutting ( milling)
gang cutting ( milling)
Machining with several cutters mounted on a single arbor, generally for simultaneous cutting.
- lathe
lathe
Turning machine capable of sawing, milling, grinding, gear-cutting, drilling, reaming, boring, threading, facing, chamfering, grooving, knurling, spinning, parting, necking, taper-cutting, and cam- and eccentric-cutting, as well as step- and straight-turning. Comes in a variety of forms, ranging from manual to semiautomatic to fully automatic, with major types being engine lathes, turning and contouring lathes, turret lathes and numerical-control lathes. The engine lathe consists of a headstock and spindle, tailstock, bed, carriage (complete with apron) and cross slides. Features include gear- (speed) and feed-selector levers, toolpost, compound rest, lead screw and reversing lead screw, threading dial and rapid-traverse lever. Special lathe types include through-the-spindle, camshaft and crankshaft, brake drum and rotor, spinning and gun-barrel machines. Toolroom and bench lathes are used for precision work; the former for tool-and-die work and similar tasks, the latter for small workpieces (instruments, watches), normally without a power feed. Models are typically designated according to their “swing,” or the largest-diameter workpiece that can be rotated; bed length, or the distance between centers; and horsepower generated. See turning machine.
- milling
milling
Machining operation in which metal or other material is removed by applying power to a rotating cutter. In vertical milling, the cutting tool is mounted vertically on the spindle. In horizontal milling, the cutting tool is mounted horizontally, either directly on the spindle or on an arbor. Horizontal milling is further broken down into conventional milling, where the cutter rotates opposite the direction of feed, or “up” into the workpiece; and climb milling, where the cutter rotates in the direction of feed, or “down” into the workpiece. Milling operations include plane or surface milling, endmilling, facemilling, angle milling, form milling and profiling.
- milling machine ( mill)
milling machine ( mill)
Runs endmills and arbor-mounted milling cutters. Features include a head with a spindle that drives the cutters; a column, knee and table that provide motion in the three Cartesian axes; and a base that supports the components and houses the cutting-fluid pump and reservoir. The work is mounted on the table and fed into the rotating cutter or endmill to accomplish the milling steps; vertical milling machines also feed endmills into the work by means of a spindle-mounted quill. Models range from small manual machines to big bed-type and duplex mills. All take one of three basic forms: vertical, horizontal or convertible horizontal/vertical. Vertical machines may be knee-type (the table is mounted on a knee that can be elevated) or bed-type (the table is securely supported and only moves horizontally). In general, horizontal machines are bigger and more powerful, while vertical machines are lighter but more versatile and easier to set up and operate.
- parting
parting
When used in lathe or screw-machine operations, this process separates a completed part from chuck-held or collet-fed stock by means of a very narrow, flat-end cutting, or parting, tool.
- sawing machine ( saw)
sawing machine ( saw)
Machine designed to use a serrated-tooth blade to cut metal or other material. Comes in a wide variety of styles but takes one of four basic forms: hacksaw (a simple, rugged machine that uses a reciprocating motion to part metal or other material); cold or circular saw (powers a circular blade that cuts structural materials); bandsaw (runs an endless band; the two basic types are cutoff and contour band machines, which cut intricate contours and shapes); and abrasive cutoff saw (similar in appearance to the cold saw, but uses an abrasive disc that rotates at high speeds rather than a blade with serrated teeth).
- toolpath( cutter path)
toolpath( cutter path)
2-D or 3-D path generated by program code or a CAM system and followed by tool when machining a part.
- turning
turning
Workpiece is held in a chuck, mounted on a face plate or secured between centers and rotated while a cutting tool, normally a single-point tool, is fed into it along its periphery or across its end or face. Takes the form of straight turning (cutting along the periphery of the workpiece); taper turning (creating a taper); step turning (turning different-size diameters on the same work); chamfering (beveling an edge or shoulder); facing (cutting on an end); turning threads (usually external but can be internal); roughing (high-volume metal removal); and finishing (final light cuts). Performed on lathes, turning centers, chucking machines, automatic screw machines and similar machines.