Completing a part on one machine in a single setup reduces machining time, boosts throughput and can increase part accuracy by maintaining the concentricity between multiple part features. Seeing a need, KOMET of America Inc. offers the KomTronic U-axis system to turn complex contours on a machining center when working with a stationary workpiece, replacing separate machining on a lathe, said Mike Hunter, business development manager for the toolmaker.
The system replaces time-consuming circular machining, or “bottle boring,” he explained. The process involves entering the mouth of a bore that is smaller than the interior of the workpiece with a tool that has a retractable cutting edge. The tool circular interpolates the part feature, moving outward and down at the same time. “It’s hard to control tolerances that way,” Hunter said. “Our tool has an accuracy close enough to do trumpet profiles for pistons and connecting rods.”
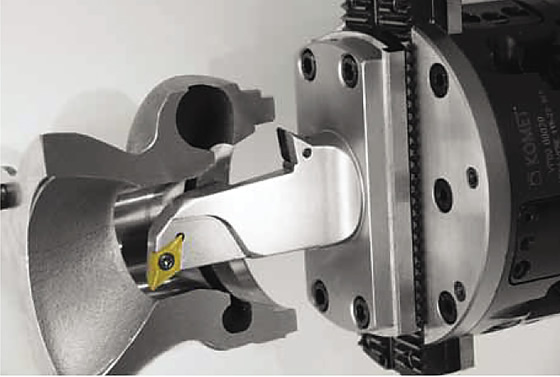
The KOMET KomTronic U-axis system enables turning contours on a machining center when working with a stationary workpiece, such as this turbocharger.
The U-axis system consists of a compact facing head with a single slide, or pusher, which is driven by a servomotor and threaded spindle. The power supplied to the electronics and the KomTronic drive system is transmitted contact-free and inductively to the U-axis system, Hunter noted. Similarly, the data is exchanged inductively with the U-axis system, and the ring-shaped inductive transmission unit on the U-axis reportedly ensures proper data and energy exchange in every angular position. “The U-axis is feeding off the transmitter that’s bolted to the spindle,” he said.
The system is suitable for standard vertical and horizontal machining centers, lathes and special machines as long as a machine’s CNC “talks the same language” as the U-axis system, Hunter noted. The array of applications includes grooving part features, turning valve seats, undercutting differential housings, boring coolant passages, tapering tie rods, generating bearing seats and turning internal and external contours, such as a spherical “door handle” shape.
For more information about KOMET of America Inc., Schaumburg, Ill., call (847) 923-8400 or visit www.komet.com.
About the Author: Alan Richter is editor of CTE. Contact him at (847) 714-0175 or alanr@jwr.comRelated Glossary Terms
- boring
boring
Enlarging a hole that already has been drilled or cored. Generally, it is an operation of truing the previously drilled hole with a single-point, lathe-type tool. Boring is essentially internal turning, in that usually a single-point cutting tool forms the internal shape. Some tools are available with two cutting edges to balance cutting forces.
- centers
centers
Cone-shaped pins that support a workpiece by one or two ends during machining. The centers fit into holes drilled in the workpiece ends. Centers that turn with the workpiece are called “live” centers; those that do not are called “dead” centers.
- computer numerical control ( CNC)
computer numerical control ( CNC)
Microprocessor-based controller dedicated to a machine tool that permits the creation or modification of parts. Programmed numerical control activates the machine’s servos and spindle drives and controls the various machining operations. See DNC, direct numerical control; NC, numerical control.
- coolant
coolant
Fluid that reduces temperature buildup at the tool/workpiece interface during machining. Normally takes the form of a liquid such as soluble or chemical mixtures (semisynthetic, synthetic) but can be pressurized air or other gas. Because of water’s ability to absorb great quantities of heat, it is widely used as a coolant and vehicle for various cutting compounds, with the water-to-compound ratio varying with the machining task. See cutting fluid; semisynthetic cutting fluid; soluble-oil cutting fluid; synthetic cutting fluid.
- grooving
grooving
Machining grooves and shallow channels. Example: grooving ball-bearing raceways. Typically performed by tools that are capable of light cuts at high feed rates. Imparts high-quality finish.
- lathe
lathe
Turning machine capable of sawing, milling, grinding, gear-cutting, drilling, reaming, boring, threading, facing, chamfering, grooving, knurling, spinning, parting, necking, taper-cutting, and cam- and eccentric-cutting, as well as step- and straight-turning. Comes in a variety of forms, ranging from manual to semiautomatic to fully automatic, with major types being engine lathes, turning and contouring lathes, turret lathes and numerical-control lathes. The engine lathe consists of a headstock and spindle, tailstock, bed, carriage (complete with apron) and cross slides. Features include gear- (speed) and feed-selector levers, toolpost, compound rest, lead screw and reversing lead screw, threading dial and rapid-traverse lever. Special lathe types include through-the-spindle, camshaft and crankshaft, brake drum and rotor, spinning and gun-barrel machines. Toolroom and bench lathes are used for precision work; the former for tool-and-die work and similar tasks, the latter for small workpieces (instruments, watches), normally without a power feed. Models are typically designated according to their “swing,” or the largest-diameter workpiece that can be rotated; bed length, or the distance between centers; and horsepower generated. See turning machine.
- machining center
machining center
CNC machine tool capable of drilling, reaming, tapping, milling and boring. Normally comes with an automatic toolchanger. See automatic toolchanger.
- turning
turning
Workpiece is held in a chuck, mounted on a face plate or secured between centers and rotated while a cutting tool, normally a single-point tool, is fed into it along its periphery or across its end or face. Takes the form of straight turning (cutting along the periphery of the workpiece); taper turning (creating a taper); step turning (turning different-size diameters on the same work); chamfering (beveling an edge or shoulder); facing (cutting on an end); turning threads (usually external but can be internal); roughing (high-volume metal removal); and finishing (final light cuts). Performed on lathes, turning centers, chucking machines, automatic screw machines and similar machines.