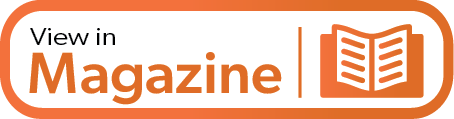
At the United Grinding booth during IMTS 2024, the company unveiled its latest innovations in remote service and machine monitoring technology, designed to streamline customer support and improve machine management for manufacturers.
Direct Communication with Experts
United Grinding demonstrated a cutting- edge feature that allows customers to connect directly with technical experts in real time through the Core Panel interface or a mobile app.
For instance, customers can initiate a call with a specialist, such as Mike Mancoso, a seasoned expert with over 20 years of experience at United Grinding. The system ensures seamless communication, enabling operators to:
- load schematics and share live data.
- upload pictures or videos for immediate diagnosis.
- receive step-by-step guidance, such as checking specific boards or components.
This real-time interaction eliminates delays typically associated with email or phonebased troubleshooting. As described, both the operator and the expert view the same information simultaneously, ensuring quick problem resolution.
Logging and Learning for Future Issues
One feature is the ability to log all interactions. Logged sessions create a knowledge base for future use, allowing operators to resolve similar issues independently. This reduces downtime and dependence on expert support.
Mobile App Capabilities
The remote service system isn’t limited to the Core Panel; it’s also available as a mobile app.
- For Business Owners: The app enables users to monitor their machines remotely, even from vacation destinations.
- Real-Time Insights: Owners and operators can check machine status, drill down into operational details, and send notes to either machine operators or United Grinding’s support team.
- File Sharing: The app supports file uploads, including pictures and schematics, making it as functional as the Core Panel interface.
Online Spare Parts Shop
United Grinding also unveiled its online spare parts shop, integrated with the remote service system.
Customers can browse and order parts directly through the platform, which consolidates all parts sold for each machine over the past 36 months.
Administrative rights allow companies to manage who can view, order and access machine data within their organization.
By reducing downtime, streamlining communication, and providing convenient access to parts and support, these tools empower businesses to maintain peak operational efficiency with minimal disruptions.
For more details, visit United Grinding.
Related Glossary Terms
- grinding
grinding
Machining operation in which material is removed from the workpiece by a powered abrasive wheel, stone, belt, paste, sheet, compound, slurry, etc. Takes various forms: surface grinding (creates flat and/or squared surfaces); cylindrical grinding (for external cylindrical and tapered shapes, fillets, undercuts, etc.); centerless grinding; chamfering; thread and form grinding; tool and cutter grinding; offhand grinding; lapping and polishing (grinding with extremely fine grits to create ultrasmooth surfaces); honing; and disc grinding.