By CGTech Inc.
You probably don’t give them much thought until they break or otherwise keep you from accessing what’s inside. Yet kitchen cabinets and, more importantly, the hardware that keeps them functioning each day is one of many unappreciated niceties of life, right alongside air conditioning and reliable cellphone signals.
Julius Blum GmbH knows all about kitchen cabinet hardware. Founded in Austria by farrier and carriage smith Julius Blum in 1952, the company’s first product was a horseshoe stud to give better traction on slippery surfaces. Six years later, Blum designed a hinge for doors and windows. Today, the company has hundreds of products, employs nearly 8,000 people at dozens of facilities and has distributors in more than 120 countries.
Although Blum has become a leader in hardware solutions, the company boasts another proud heritage: apprenticeship. In 1970, Blum launched a vocational training program in Austria, providing young people with an opportunity to participate in a four-year apprenticeship, with programs in mechanical engineering, toolmaking, CNC machining and more.
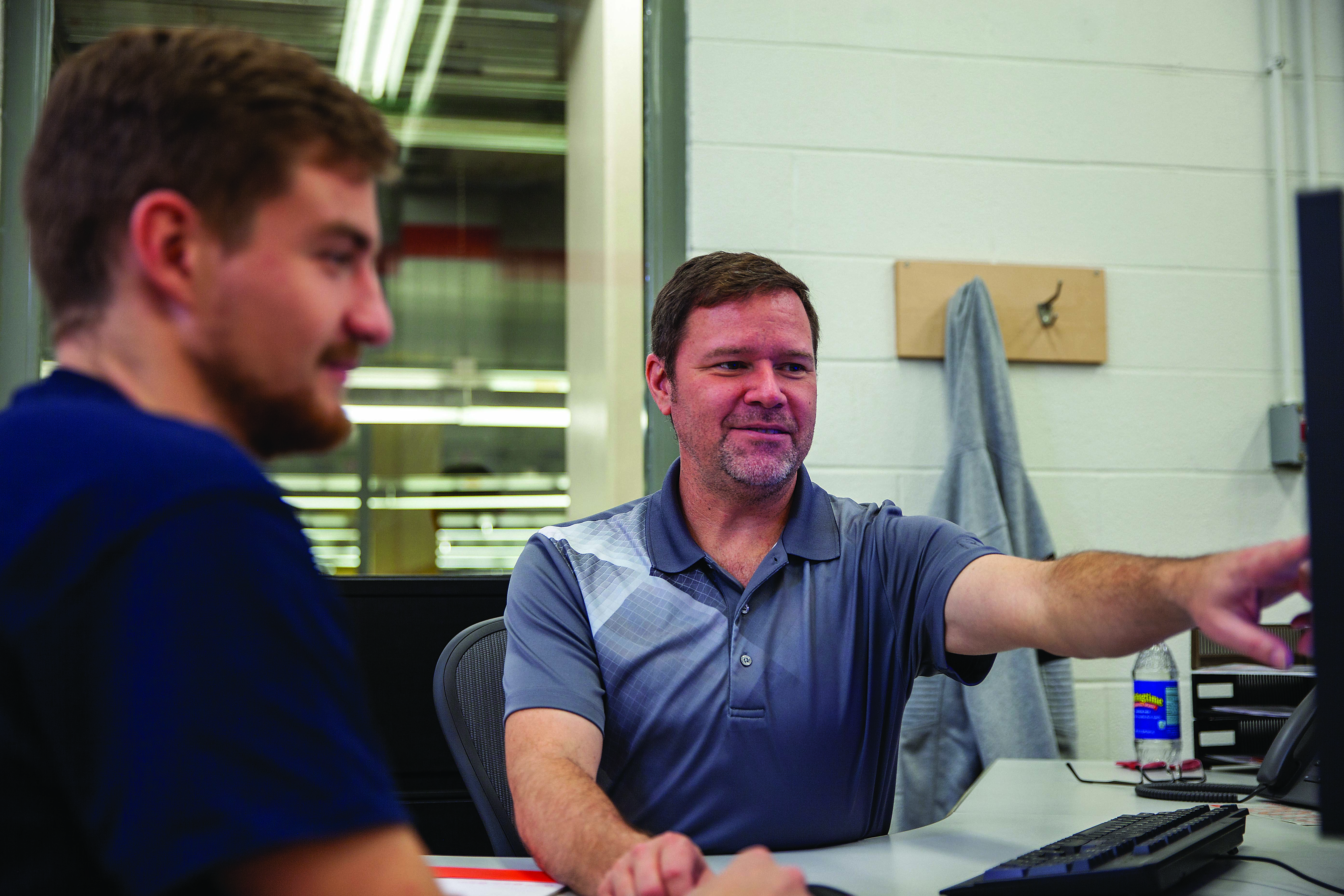
Blum’s commitment to the next generation of workers has been adopted at Blum Inc.’s manufacturing plant in Stanley, North Carolina. In 1995, the company introduced the Apprenticeship 2000 program based largely on the Austrian model. The program since has expanded to include partners Ameritech Die & Mold Inc., Daetwyler USA, Bürkert Fluid Control Systems and other North Carolina manufacturing companies, as well as participation from Central Piedmont Community College in Charlotte.
Apprenticeship trainer Jim Neal has been there from the beginning. In fact, he was one of the first graduates of the program.
“Blum started Apprenticeship 2000 because we couldn’t find the skilled workers needed to maintain our automated equipment,” he said. “Each spring, we hire a small group of high school graduates and bring them in as apprentices. Over the next four years, they receive 4,000 hours of hands-on training and 1,600 hours in the classroom, at the end of which they’ll earn a journeyman’s card from the state, a mechatronics degree from CPCC, a guaranteed job offer and no tuition debt.”
One tool that Neal uses to train apprentices is Vericut toolpath optimization, simulation and verification software from Irvine, California-based CGTech Inc.
“We originally purchased Vericut for use in our manufacturing operations,” he said. “We had a lot of work stacking up in the machine shop and saw it as a way to reduce CNC downtime and catch programming mistakes that might otherwise result in a crash. That was four years ago. Because of Vericut, there’s no longer a need to prove out a program at the machine, your hand on the feed rate override or e-stop button. Instead, everything is simulated offline. When it gets out to the floor, the operator can just let it run, confident that there won’t be any problems. Vericut paid for itself pretty quickly.”
Blum Inc. employs 450 people and supplies products to the U.S. market. The machine shop supports the factory with parts for its stamping presses, automated assembly machines, packaging equipment and plastic injection molding machines.
Neal said the results from incorporating Vericut into Blum’s training curriculum have been positive. Apprentices can test their programming skills in a virtual environment without fearing they might crash an expensive piece of CNC equipment. And because the machine tools that apprentices learn on are often the same ones that the company uses to keep the manufacturing floor operational, there’s no risk that a bad day for a student will hurt production.
“Everyone starts by writing G and M code longhand,” he said. “This way, they can understand what the program is doing before moving on to CAM-based programming. So they write their own code. And to me as a trainer, it’s really cool to see their expression when they watch it for the first time in Vericut. Most of these kids grew up on video games, and it’s quite easy for them to relate to this kind of virtual environment. They really love it.”
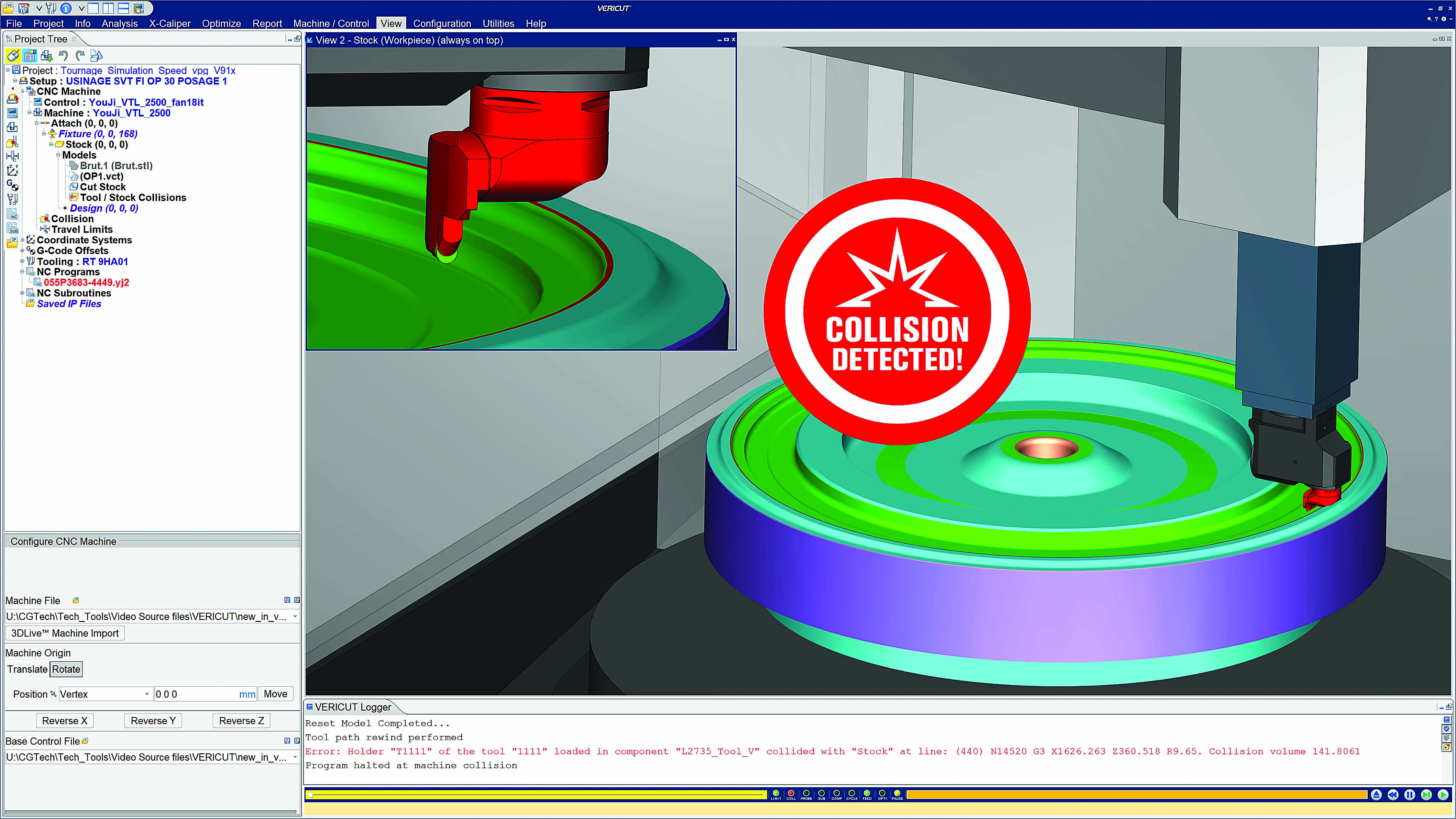
It’s also quite easy to operate, which makes Neal’s life easier.
“I’ve used quite a bit of software over the years,” he said, “and I would say Vericut is one of the most user-friendly (types of) software I’ve come across. It lets you troubleshoot and fine-tune your NC code without eating up valuable machine time. And it helps our students — many of whom have never touched machinery before — to develop a logical thinking process that can then be applied on the factory floor. It’s good for them and good for the industry.”
That last part is especially important given the shortage of skilled machinists and manufacturing workers. Apprenticeship 2000 is an example of how individual companies can help others, so much so that it has grown into a statewide program, with about 120 companies using some version of the curriculum developed by Blum Inc.
The job offer that every student receives after graduation provides a wage of at least $37,000 per year, which is higher than many college graduates can expect. Again, there’s no debt. Each student works for and is paid by his or her sponsor company throughout the program, and all tuition is covered by Apprenticeship 2000.
That doesn’t mean, however, that students are beholden to Blum or one of its partner companies after graduation.
“There’s no contract or anything,” Neal said, “but they’re guaranteed to have a job, which they can either accept or decide to go elsewhere. It’s completely up to the student. That said, most decide to stay on as illustrated by our relatively young skilled trades workforce, most of whom went through our apprenticeship program. We’ve been so successful that people from all over the country have reached out to us for information about how they might start their own apprenticeship program. From my side, it’s been a very rewarding experience, and I’m proud to be part of it. It’s a good feeling.”
For more information about CGTech Inc. in Irvine, California, call 949-753-1050 or visit www.cgtech.com.
Contact Details
Related Glossary Terms
- computer numerical control ( CNC)
computer numerical control ( CNC)
Microprocessor-based controller dedicated to a machine tool that permits the creation or modification of parts. Programmed numerical control activates the machine’s servos and spindle drives and controls the various machining operations. See DNC, direct numerical control; NC, numerical control.
- feed
feed
Rate of change of position of the tool as a whole, relative to the workpiece while cutting.
- numerical control ( NC)
numerical control ( NC)
Any controlled equipment that allows an operator to program its movement by entering a series of coded numbers and symbols. See CNC, computer numerical control; DNC, direct numerical control.
- sawing machine ( saw)
sawing machine ( saw)
Machine designed to use a serrated-tooth blade to cut metal or other material. Comes in a wide variety of styles but takes one of four basic forms: hacksaw (a simple, rugged machine that uses a reciprocating motion to part metal or other material); cold or circular saw (powers a circular blade that cuts structural materials); bandsaw (runs an endless band; the two basic types are cutoff and contour band machines, which cut intricate contours and shapes); and abrasive cutoff saw (similar in appearance to the cold saw, but uses an abrasive disc that rotates at high speeds rather than a blade with serrated teeth).
- toolpath( cutter path)
toolpath( cutter path)
2-D or 3-D path generated by program code or a CAM system and followed by tool when machining a part.