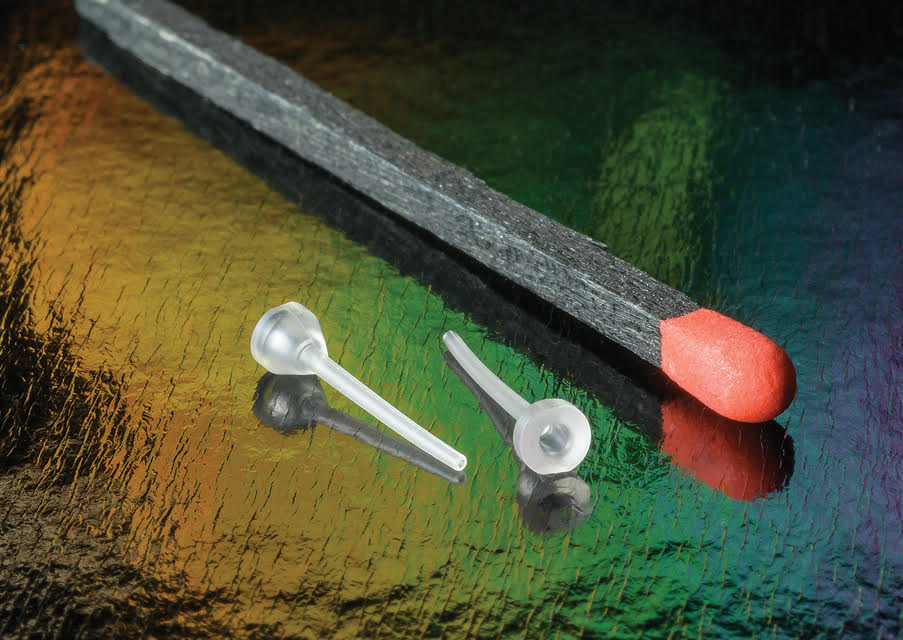
Examples of "impossibly small and intricate parts" that Accumold has developed for medical device OEMs over its nearly 40-year history will be on display at the upcoming MD&M South event on booth 1911, June 4-6, in Charlotte, North Carolina.
In addition, attendees will also be able to see examples of Accumold’s thin-walled cannulas which the company can now micro injection mold at volume.
Since 1985, Accumold has been pioneering the industrial application of micro molding for the medical device industry, which requires affordable, timely, and miniaturized parts and components, while at the same time catering to the demand for more complex geometries, the use of an array of complex-to-process thermoplastics, and tighter tolerances.
The medical device industry demands absolute precision, totally repeatable manufacturing processes, and zero failure rates for products that are frequently used in safety-critical applications. As such they must work alongside and partner with companies that are working at the cutting edge of advanced design and manufacture.
Paul Runyan, VP Sales & Marketing says, “Accumold is rightly today acknowledged as the world leader when it comes to the manufacture of extraordinarily small plastic parts that require extreme precision — typically measured in microns. The company is adept at the production of small-sized parts with micro features from 5 cm to less than 1 mm, and has specific expertise in insert molding, two-shot molding, and cleanroom molding using an array of materials including PEEK, LCP, and most engineering thermoplastics. The company is unique in that it is truly vertically integrated, and as such it can operate as a one-stop partner in the development and manufacture of medical devices and components. Under one roof, Accumold offers design and material assistance, micro tool fabrication, proprietary micro molding services, cutting-edge metrology, assembly, and automation, and this facilitates the streamlining of customer’s medical product development process, and the attainment of optimal outcomes in terms of timeliness, cost, and accuracy.”
Accumold has partnered with countless leading medical device manufacturers across the world, and with each, the company operates strategically to ensure that the product development process is as efficient as possible. The company is not only the most experienced micro molder in the world, but also the largest. This affords Accumold’s customers the reassurance of working with a robust and secure company that can provide efficiencies that lead to affordable pricing and has the capacity and infrastructure to ramp up to full mass volume manufacture. Accumold is also ISO 13485 accredited, the stringent and internationally recognized quality management system for medical devices.
Runyan continues, “We are especially pleased to be able to discuss our ground-breaking innovation in the field of thin wall cannula manufacture at MD&M South. Micro molding cannulas at volume with an outside diameter of 0.035” (0.889 mm), an inside diameter is 0.027” (0.6858 mm), and a wall thickness of 0.004” (0.1016 mm) are routine at Accumold today. We have achieved this through attention to material choice, several critical DfM considerations, assembly considerations, maintaining a balanced aspect ratio to avoid challenges associated with flow dynamics, cooling, and structural integrity, and critically importantly through the use of our proprietary micro molding presses. Micro molding thin-walled cannulas is a game changer for medical device manufacturers overcoming the labor-intensive, time-consuming, and expensive traditional thin wall cannula manufacturing processes such as extrusion, tipping, and gluing to a metal hub.”
Contact Details
Related Glossary Terms
- extrusion
extrusion
Conversion of an ingot or billet into lengths of uniform cross section by forcing metal to flow plastically through a die orifice.
- metrology
metrology
Science of measurement; the principles on which precision machining, quality control and inspection are based. See precision machining, measurement.