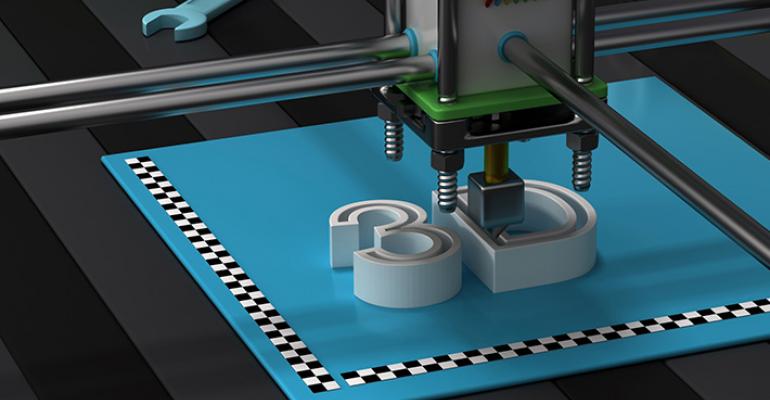
A good friend and I have had a running argument lately about 3D printing. He says the fervor over additive manufacturing is, for the most part, hype, something he likes to call the boondoggle of the manufacturing century.
He could be right.
Like me, he saw the first stereolithography (SL) machines back in 1987. We both heard the predictions back then that 3D printing would revolutionize the manufacturing industry; traditional subtractive processes would grow obsolete while a tsunami of 3D printing washed over us all. Those predictions were clearly wrong.
Additive manufacturing has been more summer sprinkle than world-changing tsunami, especially during the first decade or two as the industry tried to figure out how it all fit together. There was endless shuffling of the deck chairs on what at times seemed like a 3D-printed Titanic—the paper-based laminated object manufacturing (LOM) occasionally caught fire. The SOUP (solid object ultraviolet plotter) got cold. There’s been ballistic particle manufacturing (BPM), LENS (laser-engineered net shaping), CMB (controlled metal buildup), DMD (direct metal deposition), and DSPC (direct shell production casting) to name a few, a seemingly endless stream of acronyms that have either not amounted to much or have fallen like so much wheat to a threshing machine.
Still, 3D printing technologies such as fused deposition modeling (FDM), selective laser sintering (SLS), and direct metal laser‐sintering machine (DMLS) have created thousands of jobs and millions of products. Few would argue (not even my headstrong friend) with the fact that they’re all going strong. Nor are they alone:
Last year General Electric bought a controlling share in a leading manufacturer of 3D metal printing equipment and has since installed more than 400 such machines in its Brilliant Factory.
Companies such as Markforged, Desktop Metal, Hewlett Packard, and others have introduced new ways to build parts faster and more economically.
According to one expert, just over 13,000 industrial 3D printing systems (those priced above $5,000) were sold worldwide in 2016, more machines than were produced that same year by a popular US machine tool builder.
A recent article in Forbes magazine suggests that 90-percent of all companies using 3D printing consider it a competitive advantage, and IDC (International Data Corporation) forecast a 20-percent growth rate through 2021, potentially making additive a $25B industry.
Does that spell the death of machining and fabricating? Hardly. Conventional machine tool builders, oblivious to their looming demise, continue to make their products faster and more capable than ever before. We’ve seen the introduction in recent years of multitasking turn-mill centers, punch-laser combo machines, five-axis machining centers, Swiss-style lathes with more axis letters than a spelling bee—ironically, some machinery builders are even incorporating additive manufacturing capabilities in their subtractive manufacturing equipment.
In fact, there’s so much more cool stuff on the shop floor now compared to that day forty years ago, when I stood in front of a Wiedemann turret punch press for the first time and wondered why so many of the old guys there were missing a finger or two, that I’m quite envious of those young people now entering the trades. If only life offered do-overs.
Cool or not, do-over notwithstanding, we probably won’t settle the argument anytime soon. My friend and I will be collecting Social Security before industrial 3D printers become as commonplace as CNC lathes, machining centers, and EDM. And we’ll both be pushing up daisies before additive manufacturing of any kind approaches the accuracy and predictability of their far more mature subtractive counterparts. Until then, it’s an awesome time to be in manufacturing, no matter what kind of machine you stand in front of (or write about) each day. That’s something we can both agree on.
Related Glossary Terms
- centers
centers
Cone-shaped pins that support a workpiece by one or two ends during machining. The centers fit into holes drilled in the workpiece ends. Centers that turn with the workpiece are called “live” centers; those that do not are called “dead” centers.
- computer numerical control ( CNC)
computer numerical control ( CNC)
Microprocessor-based controller dedicated to a machine tool that permits the creation or modification of parts. Programmed numerical control activates the machine’s servos and spindle drives and controls the various machining operations. See DNC, direct numerical control; NC, numerical control.
- electrical-discharge machining ( EDM)
electrical-discharge machining ( EDM)
Process that vaporizes conductive materials by controlled application of pulsed electrical current that flows between a workpiece and electrode (tool) in a dielectric fluid. Permits machining shapes to tight accuracies without the internal stresses conventional machining often generates. Useful in diemaking.
- sawing machine ( saw)
sawing machine ( saw)
Machine designed to use a serrated-tooth blade to cut metal or other material. Comes in a wide variety of styles but takes one of four basic forms: hacksaw (a simple, rugged machine that uses a reciprocating motion to part metal or other material); cold or circular saw (powers a circular blade that cuts structural materials); bandsaw (runs an endless band; the two basic types are cutoff and contour band machines, which cut intricate contours and shapes); and abrasive cutoff saw (similar in appearance to the cold saw, but uses an abrasive disc that rotates at high speeds rather than a blade with serrated teeth).
- sintering
sintering
Bonding of adjacent surfaces in a mass of particles by molecular or atomic attraction on heating at high temperatures below the melting temperature of any constituent in the material. Sintering strengthens and increases the density of a powder mass and recrystallizes powder metals.