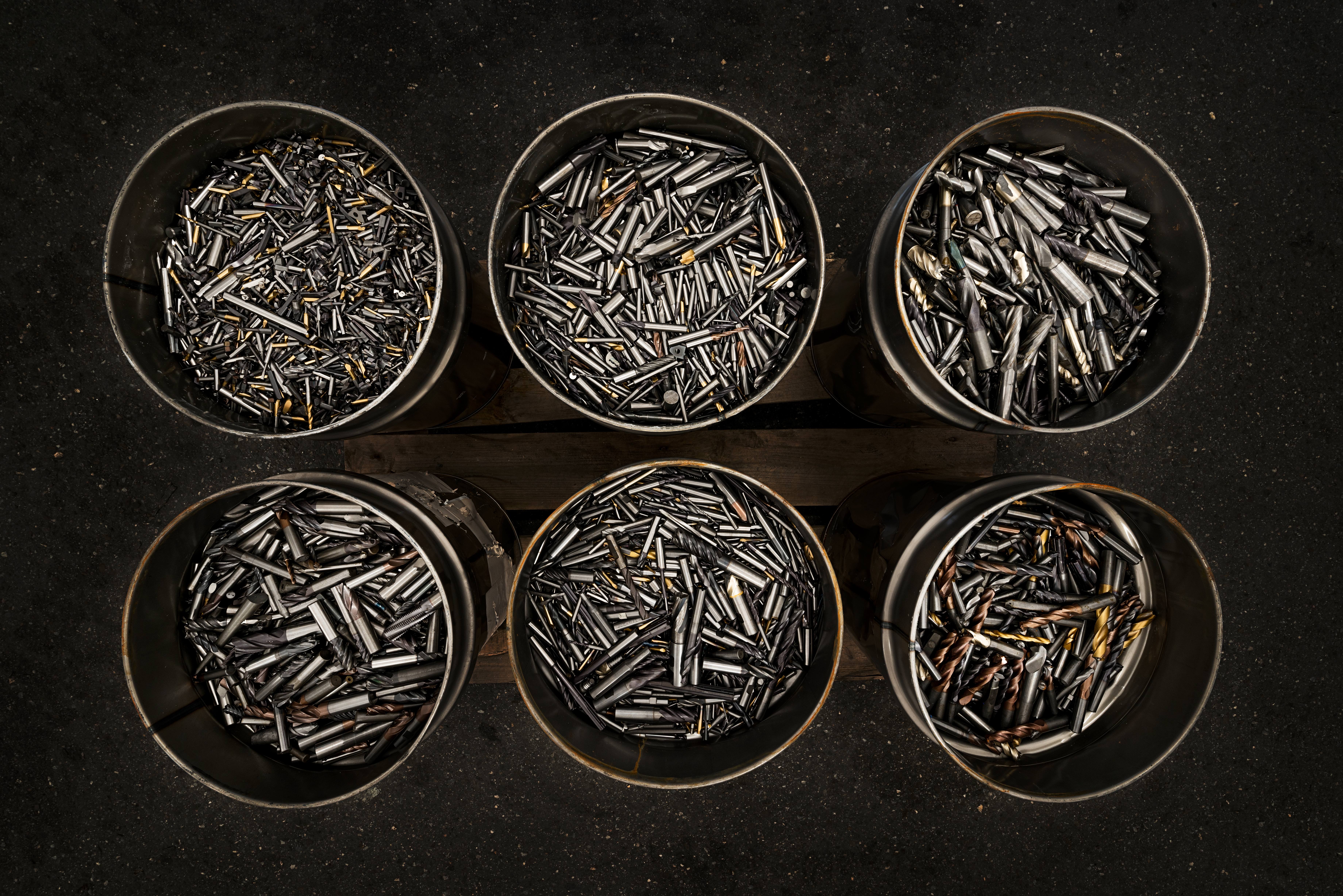
How old is your mobile phone? If you’re thinking about your current device, it’s likely that you change it every couple of years following the release of a fancy new upgrade. In reality, mobile telephones as old as the brick-like, antennae inventions of the 1980s probably remain in landfills. With many of our planet’s environmental issues linked to human consumption, it’s time to rethink our "take-make-dispose" economy.
Technology moves fast — even at the time of a new product launch, the next big thing is probably already in the pipeline. As a result, we’re creating mountains of obsolete devices that can take centuries before they begin to break down. Glass alone has no measurable decomposition period, meaning it can take over a million years before it degrades. The World Economic Forum (WEF) reports that 50 million tons of electronic waste is produced each year, which if left unchecked could rise to more than double by 2050.
But it’s not just digital devices that are creating a backlog of waste. As urbanization, industrialization and population increase around the world, the amount of waste we generate continues to rise. But what if this didn’t have to be the case?
Going full circle
According to the Ellen MacArthur Foundation, a circular economy is “based on the principals of designing out waste and pollution, keeping products and materials in use and regenerating natural systems.” By employing reuse, sharing, repair, refurbishment, remanufacturing and recycling methods to create a close-loop system, circular systems minimize the use of new materials and keep products equipment and infrastructure in use for longer.
A circular economy covers a broad scope of areas, including every industry sector, resources such as metals and minerals, as well as biological resources like food and fibers. It requires a complete overhaul of product management. Instead of focusing on driving more volume, companies are rethinking products and services from the bottom up to future proof their operations across the entire supply chain.
The foundation predicts that implementing the circular economy has the potential to deliver a 48% reduction in carbon emissions by 2030 and material cost saving of as high as $700 million per year in the fast-moving consumer goods (FMCG) segment.
Since 1862, circularity has been a part of what we do at SMT — although that’s not what we called the process back then. At the time, it was more of a question of resource efficiency, as we would re-melt leftover scrap material during production. We still apply this ethos today, but the process has been fine-tuned and our products consist of 84% recycled material on average.
More than sustainability
But circularity doesn’t only benefit businesses from a sustainability perspective. With the introduction of any new process, advantages are often rendered useless if they do not also satisfy the needs of the business. A circular economy is capable of addressing both global sustainability challenges while achieving business value by taking care of an issue that no customer is ever thrilled to deal with — waste.
Overseeing the entire lifecycle of a product gives the business greater control of their assets. This control means that the company can effectively review its costs, while also improving spending for their customers who will benefit from selling used products, helping the business create better and longer lasting relationships with customers. By recognizing that a circular economy extends business value, those across the supply chain are able to understand the value of the model.
Making the shift
Circularity is nothing new for Sandvik Machining Solutions, as Lars Ederström, project lead for sustainability and governance at SMS, explains, the business model and a buy-back program has been in play since the 1990s. “In 2006, Sandvik Coromant launched a customer buy-back program that allowed customers to return their used products so that we could recycle them and reclaim key materials such as tungsten and other rare precious metals”.
The program has since increased in volume and it is now a valuable process for SMS’s customers and its operations.
“Our customers appreciate that we manage this end-of-life process for them,” Ederström said. “In addition to lightening the burden of managing used products, we are also helping our customers contribute to the circular system and make a real difference to the sustainability of our industry.”
Our goal at Sandvik Group is to become more than 90% circular by 2030. To achieve this, we’ve recognized a number of areas where we can improve our material management, including recycling steel and cemented carbide as part of a comprehensive buying back program. Achieving this goal will be tough, even for us seasoned circularity veterans, but we’re ready to evolve a process that has been part of our DNA for the past 158 years.
SMS will also be placing stricter demands on its suppliers of raw materials and packaging, requiring them to increase their use of secondary and recycled materials. This will help ensure that not only the division’s own products contribute to the circular economy, but the materials it purchases will also be based increasingly on used materials.
It’s time to make the shift. A circular economy will not only help businesses achieve sustainability goals and make a real difference to our planet’s emission levels, but switching from a linear way of working will also help achieve real business value. Making the mot of used products ultimately creates a whole new level to the supply chain and, who knows, maybe even our retro Nokia mobile phones could make their way back into the cycle.