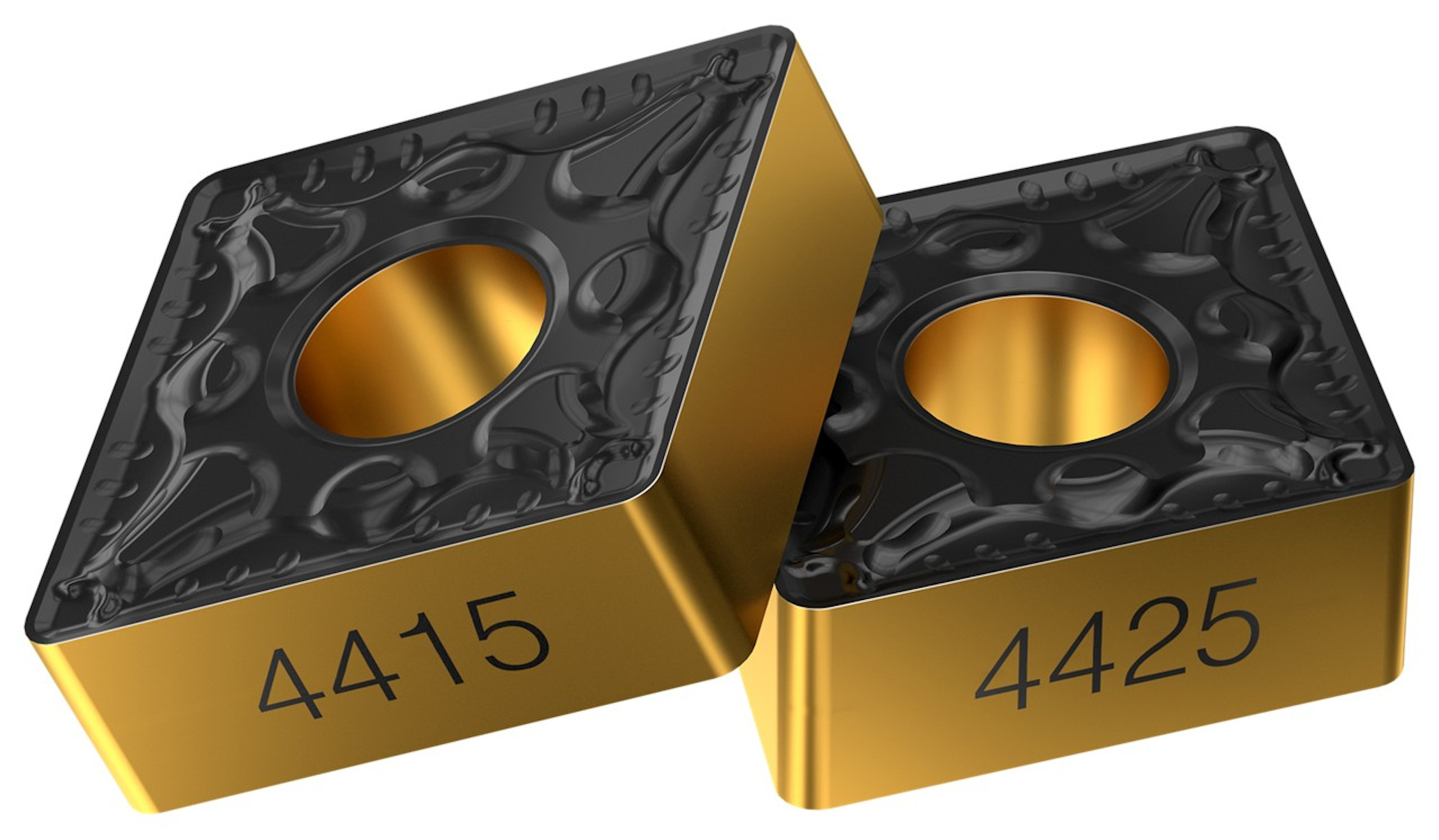
For manufacturers, stepping away from the established way of doing things — whether it’s a production process, method of communication, or a trusted machine or tool — invites risk. No wonder it tempting to fall back on the old adage of “if it ain’t broke, don’t fix it.” Could a new tool or digitalized process create more disruptions than it’s worth?
Yet, there is more onus than ever on manufacturers to change with the times — whether they are dealing with mass or batch production scenarios. Research by Pinsent Masons, the German law firm, has identified three main drivers for change.
A Sandvik Coromant survey of 100 German manufacturers and German students found that disruptive Industry 4.0 technologies, like artificial intelligence (AI) and intelligent automation, are “sparking a fresh industrial revolution”. Second, the green agenda is driving manufacturers more quickly towards low carbon business models. Third, Pinsent Masons found “that macroeconomic pressures such as Brexit, and now COVID-19, will cause global supply chains to fragment.”
How can manufacturers overcome this trio of obstacles without losing sight of the two main challenges: increasing output and reducing costs? And, how can they do so while machining one of most common and complex ISO P (steel) work piece materials? The answer lies in the next generation of tools — even if the last generation of tools ain’t broke.
The right stuff
Let’s look at the two ultimate goals for manufacturers to achieve profitable steel turning, increasing output and reducing costs. Manufacturers should drive down the appropriate production costs for their specific situation. The situation will depend on whether they are dealing with mass or batch production, and is more unpredictable in the COVID-19 era where manufacturers are facing changeable high- or low-demand scenarios, and must adapt accordingly.
Manufacturers must always strive towards maximizing their machining output that, according to Sandvik Coromant’s findings, can reduce the overall cost per component by 15%. To properly maintain a higher machine output, it’s also necessary to increase metal removal rates, and reducing scrap and component rejections to manufacture more steel components in a shorter time.
Central to all of this is the manufacturer’s choice of tool, specifically their choice of insert. That’s why Sandvik Coromant recommends choosing steel turning insert grades that can deliver most predictable and consistent performance.
Stay in shape
Sandvik Coromant added two high performing carbide insert grades to its existing range, GC4415 and GC4425. The inserts’ designations refer to P15 and P25, the demands that different working conditions impose on machining parameters — cutting data, surface finish, depth of cut, machined or rough surfaces, continuous or interrupted cuts.
The two new carbide inserts from Sandvik Coromant can meet these parameters. While GC4425 delivers improved wear resistance, heat resistance and toughness, GC4415 is designed to complement GC4425 where enhanced performance and better heat resistance is needed.
Both contain the second generation Inveio coating technology. What makes Inveio unique can be examined at the microscopic level: the material’s surface has a uni-directional crystal orientation. Each crystal lines-up towards the cutting edge, creating a strong barrier that improves crater and flank wear resistance. Heat is also lead away from the cutting zone more quickly, which keeps the cutting edge in shape for longer time in cut.
So, GC4415 and GC4425 can machine a larger number of pieces within a mass and batch production set-up. Each insert contributes towards extended tool life, eliminating sudden breakages and reducing reworking and scrap.
With the ability to machine more components one set-up, the new insert grades can reduce the production interruptions caused due to frequent insert changes and time spent in finding the right insert for each application or material — both factors are considered to be the biggest time killers in modern production.
Coolant can further improve the insert performance, deliver even better performance in all aspects and play a crucial role in reducing overall production cost. Under coolant controls the heat in the cutting zone, which leads to improved tool life and predictable machining. This makes it possible for operators to increase the cutting speed or feed, which allows for a greater productivity increase and maximized output.
In addition, precision coolant with pre-directed nozzles focused directly at the cutting zone, which is a good way to achieve chip control. That is why, if correctly applied, coolant will maximize output, increase process security and improve cutting tool performance and component quality. These are all important cornerstones in successful machining.
We’ve examined how factors like choice of tool and the use of coolant can yield tangible machining benefits — but what could manufacturing gain by applying a new methodology to their steel turning operations?
Sandvik Coromant’s specialists asked themselves this question, and the result was a new ethos that we call PrimeTurning, designed as a good choice for mass production or components needing frequent set-ups and tool changes.
In particular, if turning is a bottleneck operation, then companies suffer a restriction on the number of components produced per run. Therefore, manufacturers need to reconsider their turning process in order to get maximum output from their modern machine tools, which are currently being underutilized.
This is where the PrimeTurning can support, offering flexibility to do turning in all-directions. With it, machine shops can realise a multi-fold productivity increase without compromising process security and tool life. This way of turning is found to be much more efficient and productive compared to conventional turning.
Positive change
GC4415 and GC4425 have already proven advantageous since they were launched to market last year.
In one case, a manufacturer in general engineering, pitted the GC4415 insert against a competing insert, and put to work in machining an AISI/SAE CMC 02.1 steel workpiece with a Brinell hardness of 220 HB.
As the workpiece was subjected to axial external turning and light roughing, the customer was able to run the GC4415 at a higher cutting speed (vc) of 300 m/min (984 ft/min) and feed rate (fn) of 0.33 mm/rev (0.013 inch/rev) compared with a competitor’s insert, which ran at a vc of 250 m/min (820 ft/min) and fn of 0.25 mm/rev (0.009 inch/rev). The competitor’s insert machined 200 pieces (pcs) per edge before breaking down, whereas GC4415 machined 256 pcs before only shown signs of risk of breaking down.
By switching to GC4415 and increasing the cutting data, the customer was able to achieve a productivity of 210% and reduce costs by 53%.
Contact Details
Related Glossary Terms
- Brinell hardness number ( HB)
Brinell hardness number ( HB)
Number related to the applied load (usually, 500 kgf and 3,000 kgf) and to the surface area of the permanent impression made by a 10mm ball indenter. The Brinell hardness number is a calculated value of the applied load (kgf) divided by the surface area of the indentation (mm2). Therefore, the unit of measure of a Brinell hardness number is kgf/mm2, but it is always omitted.
- coolant
coolant
Fluid that reduces temperature buildup at the tool/workpiece interface during machining. Normally takes the form of a liquid such as soluble or chemical mixtures (semisynthetic, synthetic) but can be pressurized air or other gas. Because of water’s ability to absorb great quantities of heat, it is widely used as a coolant and vehicle for various cutting compounds, with the water-to-compound ratio varying with the machining task. See cutting fluid; semisynthetic cutting fluid; soluble-oil cutting fluid; synthetic cutting fluid.
- cutting speed
cutting speed
Tangential velocity on the surface of the tool or workpiece at the cutting interface. The formula for cutting speed (sfm) is tool diameter 5 0.26 5 spindle speed (rpm). The formula for feed per tooth (fpt) is table feed (ipm)/number of flutes/spindle speed (rpm). The formula for spindle speed (rpm) is cutting speed (sfm) 5 3.82/tool diameter. The formula for table feed (ipm) is feed per tooth (ftp) 5 number of tool flutes 5 spindle speed (rpm).
- depth of cut
depth of cut
Distance between the bottom of the cut and the uncut surface of the workpiece, measured in a direction at right angles to the machined surface of the workpiece.
- feed
feed
Rate of change of position of the tool as a whole, relative to the workpiece while cutting.
- flank wear
flank wear
Reduction in clearance on the tool’s flank caused by contact with the workpiece. Ultimately causes tool failure.
- hardness
hardness
Hardness is a measure of the resistance of a material to surface indentation or abrasion. There is no absolute scale for hardness. In order to express hardness quantitatively, each type of test has its own scale, which defines hardness. Indentation hardness obtained through static methods is measured by Brinell, Rockwell, Vickers and Knoop tests. Hardness without indentation is measured by a dynamic method, known as the Scleroscope test.
- turning
turning
Workpiece is held in a chuck, mounted on a face plate or secured between centers and rotated while a cutting tool, normally a single-point tool, is fed into it along its periphery or across its end or face. Takes the form of straight turning (cutting along the periphery of the workpiece); taper turning (creating a taper); step turning (turning different-size diameters on the same work); chamfering (beveling an edge or shoulder); facing (cutting on an end); turning threads (usually external but can be internal); roughing (high-volume metal removal); and finishing (final light cuts). Performed on lathes, turning centers, chucking machines, automatic screw machines and similar machines.
- wear resistance
wear resistance
Ability of the tool to withstand stresses that cause it to wear during cutting; an attribute linked to alloy composition, base material, thermal conditions, type of tooling and operation and other variables.