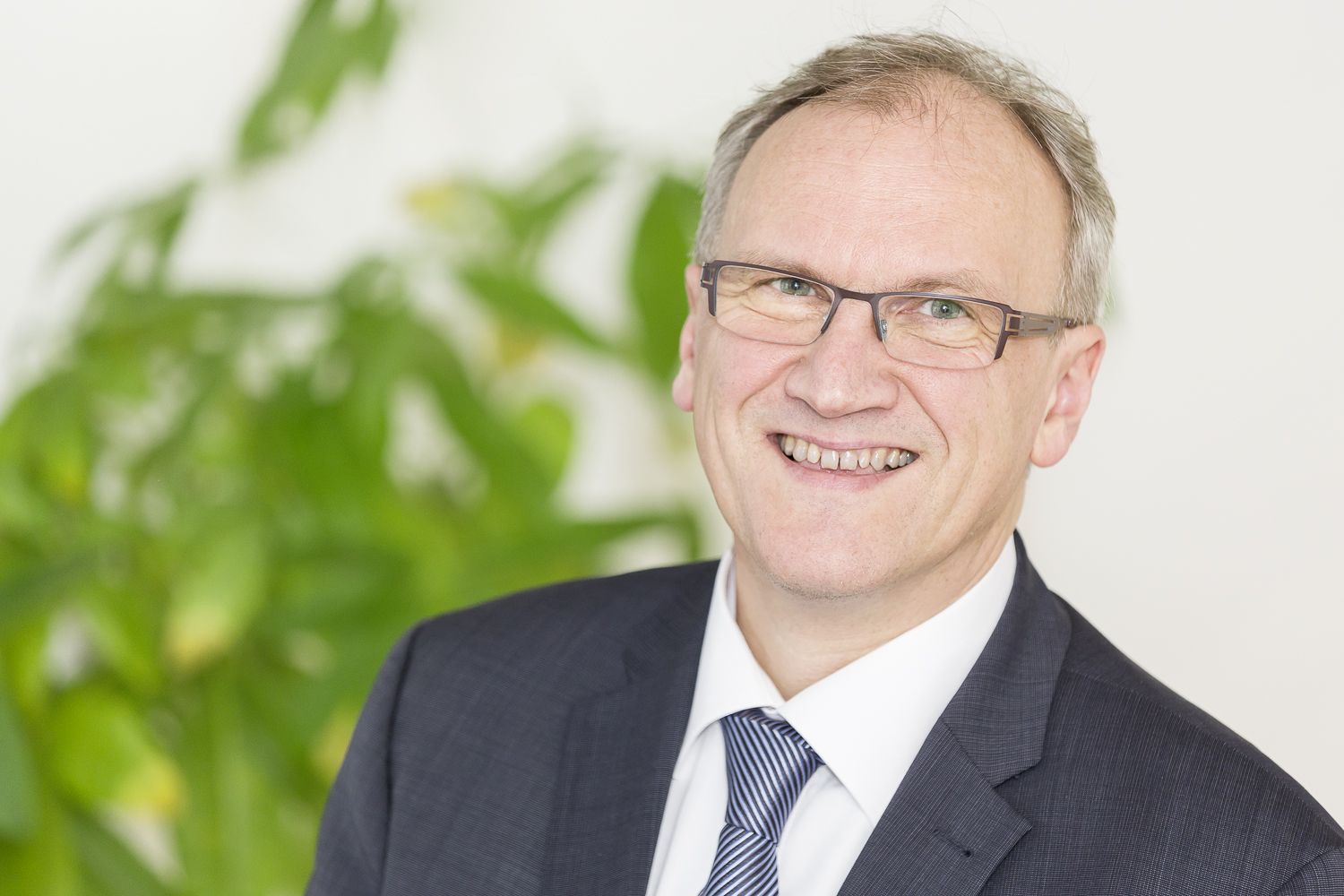
New materials require the continuous further development of tools / New processes still have to find their way into practice
It is a reminder of the race between the hare and the hedgehog: Materials are becoming stronger, tougher, more resistant. But the manufacturers of precision tools manage time and again, often in collaboration with research institutes, to also efficiently machine the most demanding materials after a relatively short time. In this interview Professor Dr.-Ing. Dirk Biermann, Director of the Institute of Machining Technology (ISF) at the Technical University of Dortmund, explains the current developments and challenges surrounding the tool.
Professor Biermann, the materials being processed are becoming more and more challenging. How much longer can the tools keep up?
Years ago when we received high-strength bainitic steels for components for high-performance engines with turbochargers and diesel injection technology, initially I was somewhat sceptical about whether we could manage the deep drilling. But together with tool partners we found solutions relatively quickly, because we now know much more about the details of the cutting edge. Today, before the coating we are able to purposefully create asymmetrical micro-geometry instead of simple rounding. Combined with a proper coating and optimally set end and face areas, one can significantly increase the performance of tools. I am therefore optimistic that we can continue to advance tooling systems in the details, mainly in the micro-geometry and in the more accurate design of the effective surface in conjunction with suitable hard layers.
The key word is coatings. What can we expect in this area?
We have to examine and optimise the connection between substrate, micro-geometry and coatings much more than in the past. Coating technologies still boast huge potential for further development and adjustment. In particular, the systems engineering for implementation by the tool manufacturers offers many possibilities here. Tool manufacturers should work intensively on this topic, in order to have potential solutions up their sleeve when the requirements of the materials further increase.
Some manufacturers are concentrating on newer concepts such as cryogenic machining or additive manufacturing. What can these concepts contribute?
Cryogenic machining also offers huge potential, but there is still some homework to be done in its implementation. Recent developments from companies such as Starrag, who prepare machines for an internal supply of CO2 cooling, and Rother, who combine CO2 cooling with minimum lubrication, have made significant progress. With these developments both problems with chip breaking and ridges in the case of more difficult materials, and the wear effect on the tool, can be dealt with very well. However, I am only familiar with very few specific applications in practice. Additive manufacturing processes are useful when designs and moulds cannot be manufactured using conventional methods, for example the inner cooling of tools and tool bodies. I am expecting rapid development here. In addition to cooling, the dynamic behaviour of tool bodies can also be positively influenced by inner structures and the combination of different materials.
What would you recommend to toolmakers in order to remain competitive?
They should once again intensively review classic machining tasks. An example from the area of thread production is the "punch tap" helical thread-forming process from Emuge. It is phenomenal how the task of internal thread production has been completely redesigned, thus enabling massive increases in productivity. Another example is deep drilling, where we can generate pilot bore holes, even with very small diameters, for single-lip deep drills using a laser drilling system. As a result, significantly more bearings in the combustion engine can be efficiently supplied with pressure oil, which in turn helps further reduce internal friction. The Industry 4.0 concept also opens up completely new opportunities. As a tool manufacturer I would use the opportunity and provide information about what is happening in the process by presenting my tools with their wear behaviour.