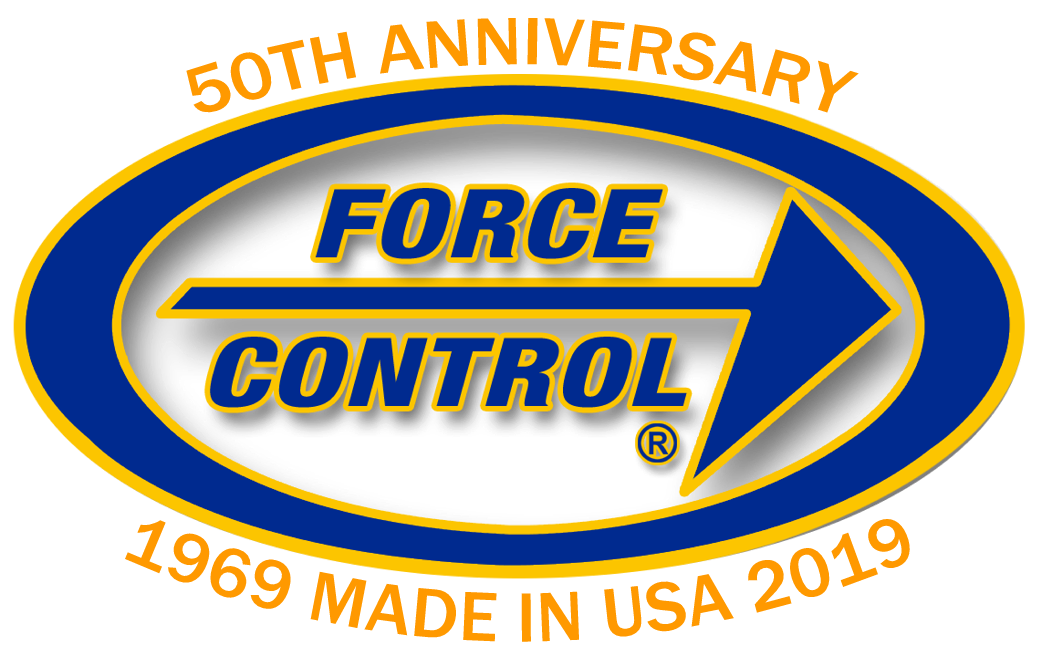
Force Control Industries celebrates 50 years of manufacturing long lasting oil shear clutches, brakes and clutch brakes. Although industries and applications have come and gone in the five decades that the company has been in business, Force Control Industries continues to develop new uses for its unique oil shear technology.
All Force Control products are manufactured in the company's Fairfield, Ohio, factory, and are supplied to a wide range of industries, including aggregate and mining, chemical and food processing, bottling plants, lumber manufacturing, concrete block manufacturing, packaging, steel mills, and general industrial/manufacturing.
“We specialize in difficult applications where traditional brakes and clutches have failed,” says President Joe Besl. “Our products usually last five to 10 times longer that whatever we’re replacing, with no adjustment or maintenance required. That’s a significant savings for our customers over the life of the product.”
Some products have been in service for much of the company’s lifetime, and the company is actively searching for the oldest continually operating product. Customers can relay the serial number to their local representative or stocking dealer.
Unlike dry brakes and clutches, oil shear technology provides a film of transmission fluid between the brake disc and the drive plate. As the fluid is compressed, the fluid molecules in shear transmit torque to the other side. This torque transmission causes the two components to reach the same relative speed. Since most of the work is done by the fluid particles in shear, wear is virtually eliminated. Elimination of wear eliminates the need for adjustments which are common for dry braking systems, especially spring set brakes.
In addition to transmitting torque, a patented fluid recirculation system helps to dissipate the heat from the friction surface to the housing where it is cooled. The inability of the dry friction units to dissipate the heat out of the friction material is a major cause of wear and friction material breakdown. Along with heat removal and torque transmission, the fluid serves to continually lubricate all components of the oil shear units, significantly increasing their service life.
Contact Details
Related Glossary Terms
- drive plate
drive plate
Attaches to a lathe spindle and has a slot or slots that engage a driving dog to turn the work. Usually used in conjunction with centers. See centers; driving dog.