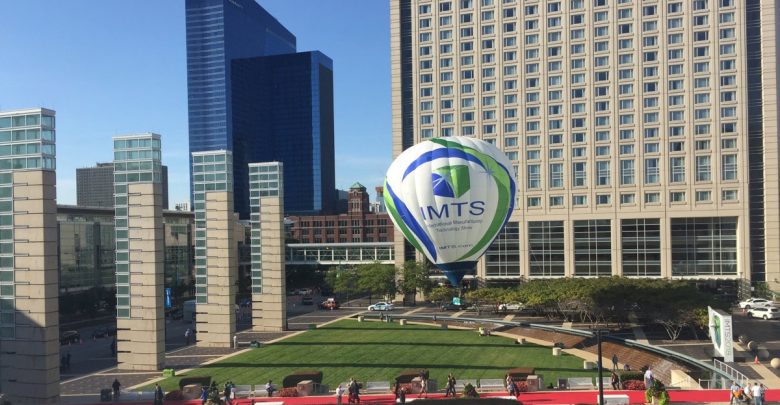
Despite my sore feet and the cold, overpriced sandwiches, I love the International Manufacturing Technology Show. The whine of the spindles, the smell of the coolant, the machine gun sound of the chips hitting the glass—these might not be the memories the exhibitors want me to carry home, but they stick with me the longest.
My first time there was in 1992. Although I haven’t been to every IMTS since, I’ve seen enough of them to observe some dramatic changes to the show, the industry and especially the technology each of us work with, peddle or, in my case, write about almost every day of the week.
In 1992, robots were used mainly by automakers. Today, robots are a common sight in shops of all sizes and becoming more so with each passing day. Additive manufacturing was a novelty; now there are 3D printers everywhere. Multitasking machines had not yet been invented. The internet of things was on dial-up. And Industry 4.0? We were still busy wrapping up the previous Industrial Revolution.
I’ve said it before, and I’ll keep saying it: If only I were 30 years younger, because now is quite simply a very cool time to be in manufacturing.
And yet IMTS in some ways makes me profoundly sad. As I watch the husband-and-wife team evaluate new equipment for their shop or the father and son drinking beer in one of the machine tool booths, arguing good-naturedly over the merits of linear servodrives or live-tooled lathes, I wonder if that could have been me and my family had my aborted attempt at shop ownership turned out differently.
It’s not simply shop ownership that I’ve lost, however. I learned what little I know about machine tool sales from Boyd Ehret, my friend and would-be mentor who was at that first IMTS with me and who I recently learned died at his desk a few years ago. I like to think he’d just wrapped up another big deal.
I think of Jerry Korinek, who once referred to the high-speed (at that time) maneuverings of our first CNC lathe as “exotic movements.” How we laughed. Jerry went in for gastric bypass surgery one day and never came home.
Similarly, chucker operator extraordinaire James “Red” Shoberg walked back to the sawing room one day to check on a job and hit the ground halfway there, dead of an embolism. I wish now that I’d kept the ’67 Chevelle I bought from him at our first job together.
There was Wayne Rude, who taught me how to ride a motorcycle and managed to keep his temper after I spilled his prized Yamaha dirt bike on the road next to his home in Elk River, Minnesota. He and his wife, Laura, worked with me at three different shops over the years, and his death from lung cancer hit me at a particularly bad time. Sorry about the scratches, buddy.
And of course there was my brother Kirby, who also worked with me at so many jobs. The garter snake in my desk drawer, the rubber vomit, the bottle rocket under the bathroom door and the subsequent chase through the shop—these were the things I thought about as I cruised the halls of McCormick Place in Chicago this month at IMTS. The ghosts of my brother, my friends and my co-workers kept me company in the crowded but sometimes lonely place.
How many others have slipped away since that first IMTS, people I worked with over the years but whose deaths I’m simply unaware of? If you’re listening, I miss you all. See you in 2020.
Related Glossary Terms
- computer numerical control ( CNC)
computer numerical control ( CNC)
Microprocessor-based controller dedicated to a machine tool that permits the creation or modification of parts. Programmed numerical control activates the machine’s servos and spindle drives and controls the various machining operations. See DNC, direct numerical control; NC, numerical control.
- coolant
coolant
Fluid that reduces temperature buildup at the tool/workpiece interface during machining. Normally takes the form of a liquid such as soluble or chemical mixtures (semisynthetic, synthetic) but can be pressurized air or other gas. Because of water’s ability to absorb great quantities of heat, it is widely used as a coolant and vehicle for various cutting compounds, with the water-to-compound ratio varying with the machining task. See cutting fluid; semisynthetic cutting fluid; soluble-oil cutting fluid; synthetic cutting fluid.
- lathe
lathe
Turning machine capable of sawing, milling, grinding, gear-cutting, drilling, reaming, boring, threading, facing, chamfering, grooving, knurling, spinning, parting, necking, taper-cutting, and cam- and eccentric-cutting, as well as step- and straight-turning. Comes in a variety of forms, ranging from manual to semiautomatic to fully automatic, with major types being engine lathes, turning and contouring lathes, turret lathes and numerical-control lathes. The engine lathe consists of a headstock and spindle, tailstock, bed, carriage (complete with apron) and cross slides. Features include gear- (speed) and feed-selector levers, toolpost, compound rest, lead screw and reversing lead screw, threading dial and rapid-traverse lever. Special lathe types include through-the-spindle, camshaft and crankshaft, brake drum and rotor, spinning and gun-barrel machines. Toolroom and bench lathes are used for precision work; the former for tool-and-die work and similar tasks, the latter for small workpieces (instruments, watches), normally without a power feed. Models are typically designated according to their “swing,” or the largest-diameter workpiece that can be rotated; bed length, or the distance between centers; and horsepower generated. See turning machine.
- multifunction machines ( multitasking machines)
multifunction machines ( multitasking machines)
Machines and machining/turning centers capable of performing a variety of tasks, including milling, drilling, grinding boring, turning and cutoff, usually in just one setup.
- sawing
sawing
Machining operation in which a powered machine, usually equipped with a blade having milled or ground teeth, is used to part material (cutoff) or give it a new shape (contour bandsawing, band machining). Four basic types of sawing operations are: hacksawing (power or manual operation in which the blade moves back and forth through the work, cutting on one of the strokes); cold or circular sawing (a rotating, circular, toothed blade parts the material much as a workshop table saw or radial-arm saw cuts wood); bandsawing (a flexible, toothed blade rides on wheels under tension and is guided through the work); and abrasive sawing (abrasive points attached to a fiber or metal backing part stock, could be considered a grinding operation).