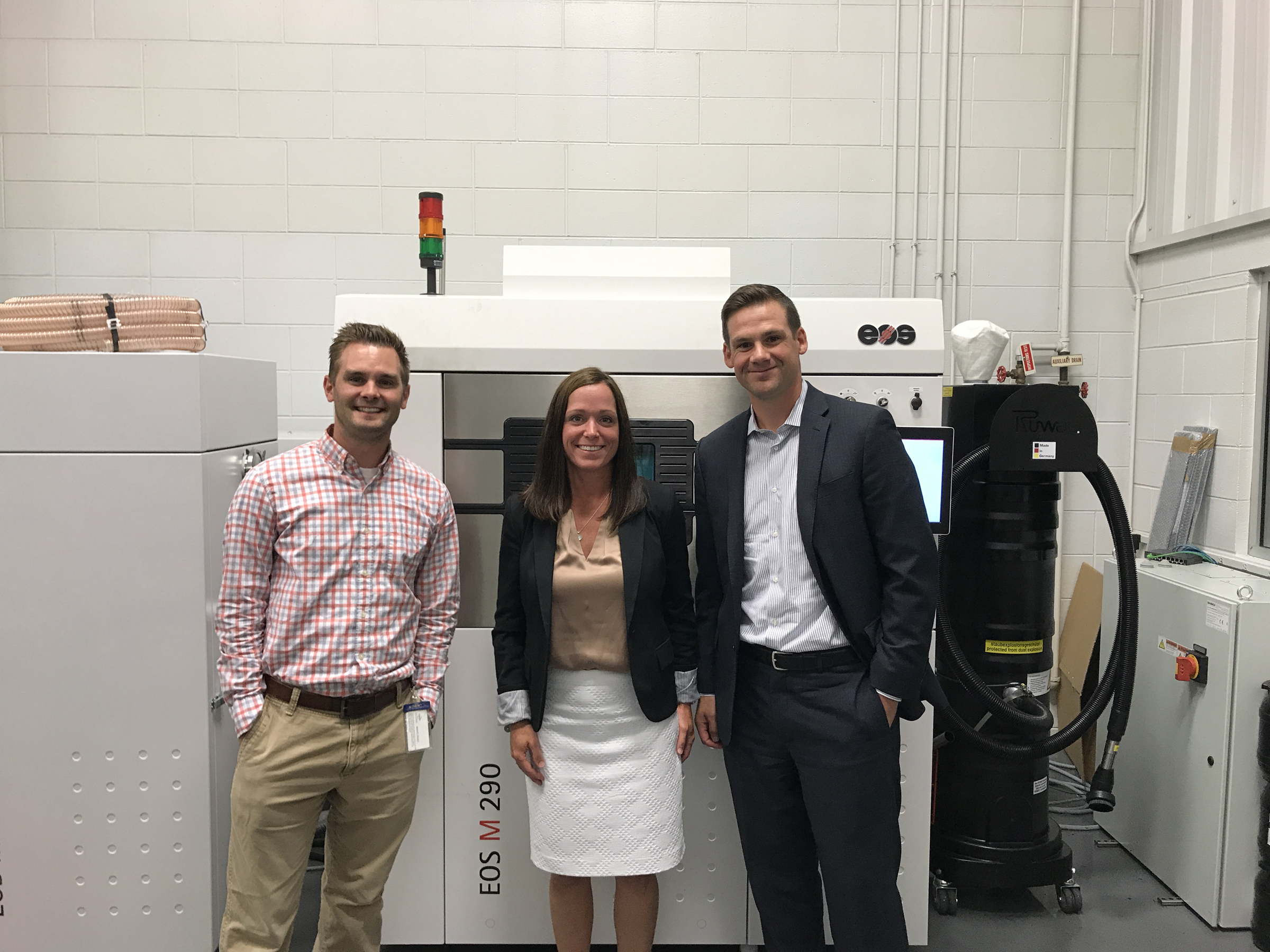
ITAMCO (Indiana Technology and Manufacturing Companies) is delivering components to the medical device industry made with their new EOS M 290 additive manufacturing printer. The EOS printer was delivered in June 2017 and ITAMCO was shipping components to a medical device supplier in August. The fast ramp up is partially due to the experience the ITAMCO team gained while contributing to the development of additive manufacturing software. They were part of a consortium of manufacturers and universities that collaborated to develop the program through a multi-million dollar manufacturing initiative called "America Makes.” The software, named “Atlas 3D,” is now marketed through a division of ITAMCO.
Another reason for ITAMCO’s efficient entry into additive manufacturing was EOS. “The EOS printer is the right tool for our complex components made with DMLS (Direct Metal Laser Sintering) and the EOS team trained our staff and got us up and running quickly,” said Joel Neidig, director of R&D for ITAMCO. “The printer works seamlessly with Atlas 3D, too.”
In addition, the technology team at ITAMCO quickly built a good working relationship with the EOS sales and support team. Jon Walker, area sales manager with EOS North America, said: “ITAMCO is an ideal partner for EOS because three generations of ITAMCO leaders have supplied traditional subtractive manufactured parts to some of the best known organizations in the world. Due to their reputation, ITAMCO’s investment in additive manufacturing validates the 3D printing market, especially in highly regulated industries where testing and validation of components or devices is critical. We’re thrilled that they have invested in an EOS M 290 3D printing platform, smartly positioning themselves to become an additive manufacturing leader in robust medical and industrial markets for the next three generations and beyond.”
The medical device industry is a relatively new market for the company that has serviced heavy-duty industries for decades. “Additive manufacturing is allowing us to do things we’ve not done before, like producing the smaller, more intricate components for the medical device industry,” Neidig said.
Given ITAMCO’s capabilities and their close proximity to numerous medical implant manufacturers in Indiana, the entry into this industry is a logical move. “We’ve hired two people from medical device companies to work for us,” Neidig said. “Of course, we will continue to expand our presence in our current markets by offering additive manufacturing and the high-quality subtractive manufacturing that made us so successful.”
ITAMCO has been on track to include additive manufacturing in their offerings since the launch of their “Strategic Technology Initiative for Additive Manufacturing” in 2015. ITAMCO is using additive manufacturing to expand their market position in a global economy and to deliver real benefits to their customers. These benefits include:
• fast turnaround
• light yet strong components
• low prices
• design freedom
• product customization
• reasonably priced small-batch production