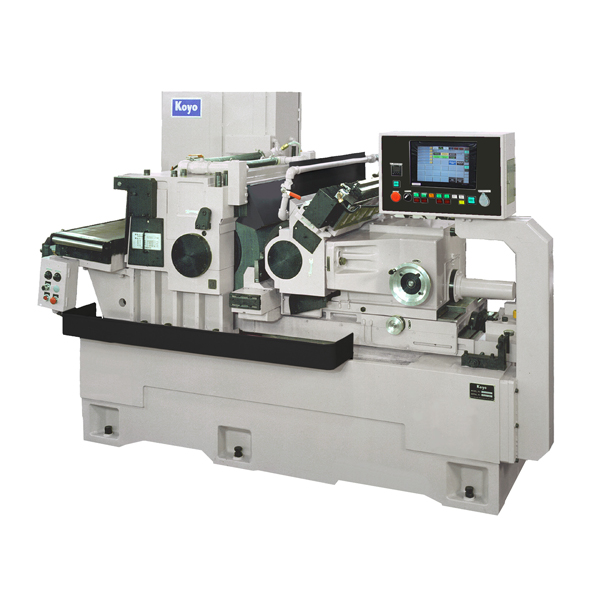
Koyo Machinery USA, a provider of precision grinding machines and systems for production applications, has been integrated into JTEKT Machinery’s range of products, services, and customer support operations.
The merger is an extension of JTEKT Corporation’s global brand "unification initiative" launched in 2021 that is designed to strategically reshape the company for increased efficiency and greater synergy between group companies, said Michael Defer, president and CEO, JTEKT Machinery Americas Corporation. “This is a positive change that will provide higher value and benefits to our customers,” according to the company.
With the JTEKT affiliation dating back to 2006, this merger now formally integrates KOYO into JTEKT Machinery’s operational infrastructure, which means the capacity for customer service and support is significantly expanded.
Expanded capabilities include service responsiveness, a larger spare parts and support organization, strengthened engineering resources, and a vastly improved machine and component rebuild division.
Koyo remains in Michigan
Additionally, Koyo Machinery’s operational core will remain in the Detroit area, moving to JTEKT Machinery’s Wixom, Michigan, facility.
All existing Koyo Machinery customers are encouraged to direct service and parts inquiries to JTEKT Machinery’s primary support lines, while the existing contact Koyo information will remain active for the foreseeable future. Koyo had been headquartered in Plymouth, Michigan.
Leading grinding machine manufacturers around the world have relied on technology for high-volume precision grinding. Each machine is designed and built to provide reliable long-term performance.
Koyo machines include centerless, surface and special-purpose grinders, such as silicon disc grinders. The company recently demonstrated a new double-disc horizontal grinder that simultaneously grinds both sides of silicon wafers to ±1 micron from as-sliced condition.
According to the company, the DXSG320 performance represents a massive improvement in accuracy and productivity over the single-spindle vertical grinders common in the chip industry today that the company says grinds to 3-4 microns, according to the company.
“Our primary lines—Koyo grinders and JTEKT machining centers and grinders—combine with our additional turning and large bridge machines, to create synergistic strengths for supporting manufacturing in diverse industries with metal cutting machines including horizontal and vertical machining centers, bridge mills, boring mills, and grinding machines,” said Defer. “We can add to that our automation, application engineering, controls and rebuild services to provide our customers end-to-end lifetime support of their manufacturing from a single, trusted source.”
Contact Details
Related Glossary Terms
- boring
boring
Enlarging a hole that already has been drilled or cored. Generally, it is an operation of truing the previously drilled hole with a single-point, lathe-type tool. Boring is essentially internal turning, in that usually a single-point cutting tool forms the internal shape. Some tools are available with two cutting edges to balance cutting forces.
- centers
centers
Cone-shaped pins that support a workpiece by one or two ends during machining. The centers fit into holes drilled in the workpiece ends. Centers that turn with the workpiece are called “live” centers; those that do not are called “dead” centers.
- grinding
grinding
Machining operation in which material is removed from the workpiece by a powered abrasive wheel, stone, belt, paste, sheet, compound, slurry, etc. Takes various forms: surface grinding (creates flat and/or squared surfaces); cylindrical grinding (for external cylindrical and tapered shapes, fillets, undercuts, etc.); centerless grinding; chamfering; thread and form grinding; tool and cutter grinding; offhand grinding; lapping and polishing (grinding with extremely fine grits to create ultrasmooth surfaces); honing; and disc grinding.
- grinding machine
grinding machine
Powers a grinding wheel or other abrasive tool for the purpose of removing metal and finishing workpieces to close tolerances. Provides smooth, square, parallel and accurate workpiece surfaces. When ultrasmooth surfaces and finishes on the order of microns are required, lapping and honing machines (precision grinders that run abrasives with extremely fine, uniform grits) are used. In its “finishing” role, the grinder is perhaps the most widely used machine tool. Various styles are available: bench and pedestal grinders for sharpening lathe bits and drills; surface grinders for producing square, parallel, smooth and accurate parts; cylindrical and centerless grinders; center-hole grinders; form grinders; facemill and endmill grinders; gear-cutting grinders; jig grinders; abrasive belt (backstand, swing-frame, belt-roll) grinders; tool and cutter grinders for sharpening and resharpening cutting tools; carbide grinders; hand-held die grinders; and abrasive cutoff saws.
- micron
micron
Measure of length that is equal to one-millionth of a meter.
- turning
turning
Workpiece is held in a chuck, mounted on a face plate or secured between centers and rotated while a cutting tool, normally a single-point tool, is fed into it along its periphery or across its end or face. Takes the form of straight turning (cutting along the periphery of the workpiece); taper turning (creating a taper); step turning (turning different-size diameters on the same work); chamfering (beveling an edge or shoulder); facing (cutting on an end); turning threads (usually external but can be internal); roughing (high-volume metal removal); and finishing (final light cuts). Performed on lathes, turning centers, chucking machines, automatic screw machines and similar machines.