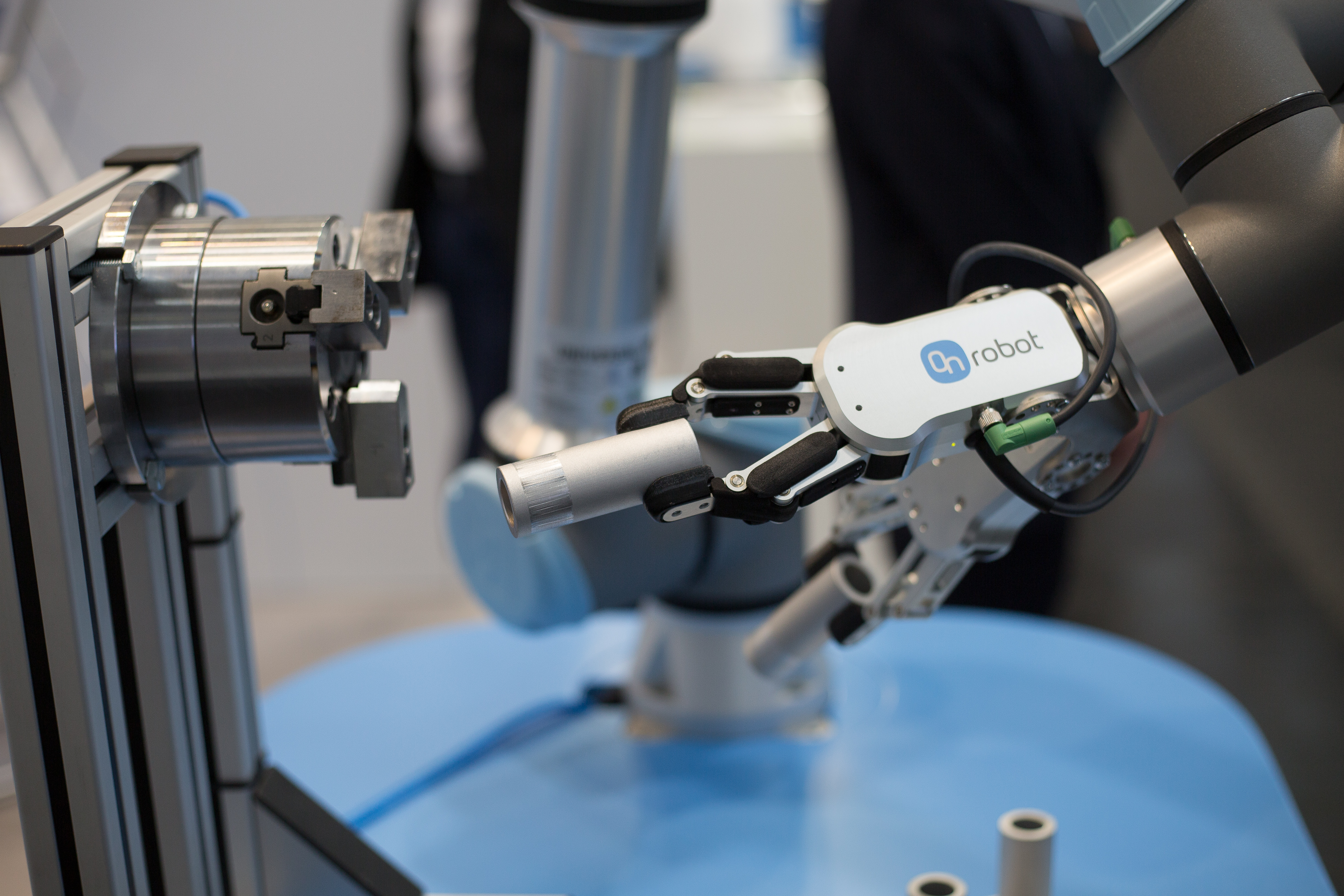
Based on the high level of traffic and activity that I saw at Automate 2019 combined with a U.S. unemployment rate of just under 4%, my hunch is that robot manufacturers will report impressive sales figures this year. This guestimate is a result of a conversation I had with Joseph Gemma, CEO of division industries – Americas for KUKA Robotics Corp., Shelby Township, Michigan. According to Gemma, as the unemployment rate decreases, robot sales increase. He emphasized that automation is changing jobs—not taking them away.
The biennial trade show for robotics, machine vision, motion control and related technologies took place April 8-11 at McCormick Place in Chicago. It will move to Detroit’s Cobo Center in 2021 and take place May 17-20.
Regarding employment opportunities, Joe Campbell, senior manager, strategic marketing and applications for Odense, Denmark-headquartered Universal Robots A/S, who is based in Bloomfield Hills, Michigan, said there are about 520,000 unfilled U.S. manufacturing jobs. The company makes collaborative robots, or cobots, and reports that they can help manufacturers beat the labor shortage while multiplying workforce productivity and increasing customer value. Universal Robots USA Inc. is based in Ann Arbor, Michigan.
On display at UR’s exhibit was its first industrial cobot, which was introduced in 2008. The company now has a 50% to 55% share of the cobot market, which is expected to experience up to a tenfold increase by 2025, according to Campbell.
UR, however, wasn’t the only exhibitor displaying UR cobots at Automate and the co-located ProMat show. The company reports that more than 30 other exhibitors kitted their stands with one or more UR cobots. One was Odense, Denmark-based OnRobot A/S, which included a display of how one of the company’s grippers can be fitted on a UR cobot to load parts into a 3-jaw chuck. OnRobot Americas is based in Irving, Texas.
Kristian Hulgard, general manager – Americas at OnRobot, said one trend he sees is electric grippers replacing pneumatic ones even though electric ones cost more because they can be controlled by software to generate needed data.
Related Glossary Terms
- arbor
arbor
Shaft used for rotary support in machining applications. In grinding, the spindle for mounting the wheel; in milling and other cutting operations, the shaft for mounting the cutter.
- chuck
chuck
Workholding device that affixes to a mill, lathe or drill-press spindle. It holds a tool or workpiece by one end, allowing it to be rotated. May also be fitted to the machine table to hold a workpiece. Two or more adjustable jaws actually hold the tool or part. May be actuated manually, pneumatically, hydraulically or electrically. See collet.
- robotics
robotics
Discipline involving self-actuating and self-operating devices. Robots frequently imitate human capabilities, including the ability to manipulate physical objects while evaluating and reacting appropriately to various stimuli. See industrial robot; robot.
- sawing machine ( saw)
sawing machine ( saw)
Machine designed to use a serrated-tooth blade to cut metal or other material. Comes in a wide variety of styles but takes one of four basic forms: hacksaw (a simple, rugged machine that uses a reciprocating motion to part metal or other material); cold or circular saw (powers a circular blade that cuts structural materials); bandsaw (runs an endless band; the two basic types are cutoff and contour band machines, which cut intricate contours and shapes); and abrasive cutoff saw (similar in appearance to the cold saw, but uses an abrasive disc that rotates at high speeds rather than a blade with serrated teeth).