
Canadian manufacturers in Edmonton, Alberta, and Cambridge, Ontario, got to see the latest in automation-ready machines, artificial intelligence, and industry 4.0 technology software from Mazak Canada.
At both open house events, Mazak showcased its Done in One part production concept and advanced Industry 4.0 technology software, along with CNC controls that use Artificial Intelligence (AI).
The Done in One concept incorporates all processes from raw materials input through final machining in just one machine. The concept offers manufacturers maximum productivity, reduces production lead times, improves accuracy, and lowers operating expenses.
With combatting the skilled labor shortage in mind, Mazak showcased automation-ready multi-tasking machines.
These machines included the Integrex i-300S advanced multi-tasking machine that features second turning spindles for Done in One part processing and works to minimize fixtures, tools, handling, and non-cut time and the Integrex j-200S multi-tasking machine with an integral spindle/motor headstock for heavy-duty and high-speed cutting and two turning spindles and milling spindle-produced steel bottle openers, and the QT-Ez 12MY 2-axis machine showcased milling and Y-axis off-centerline capability.
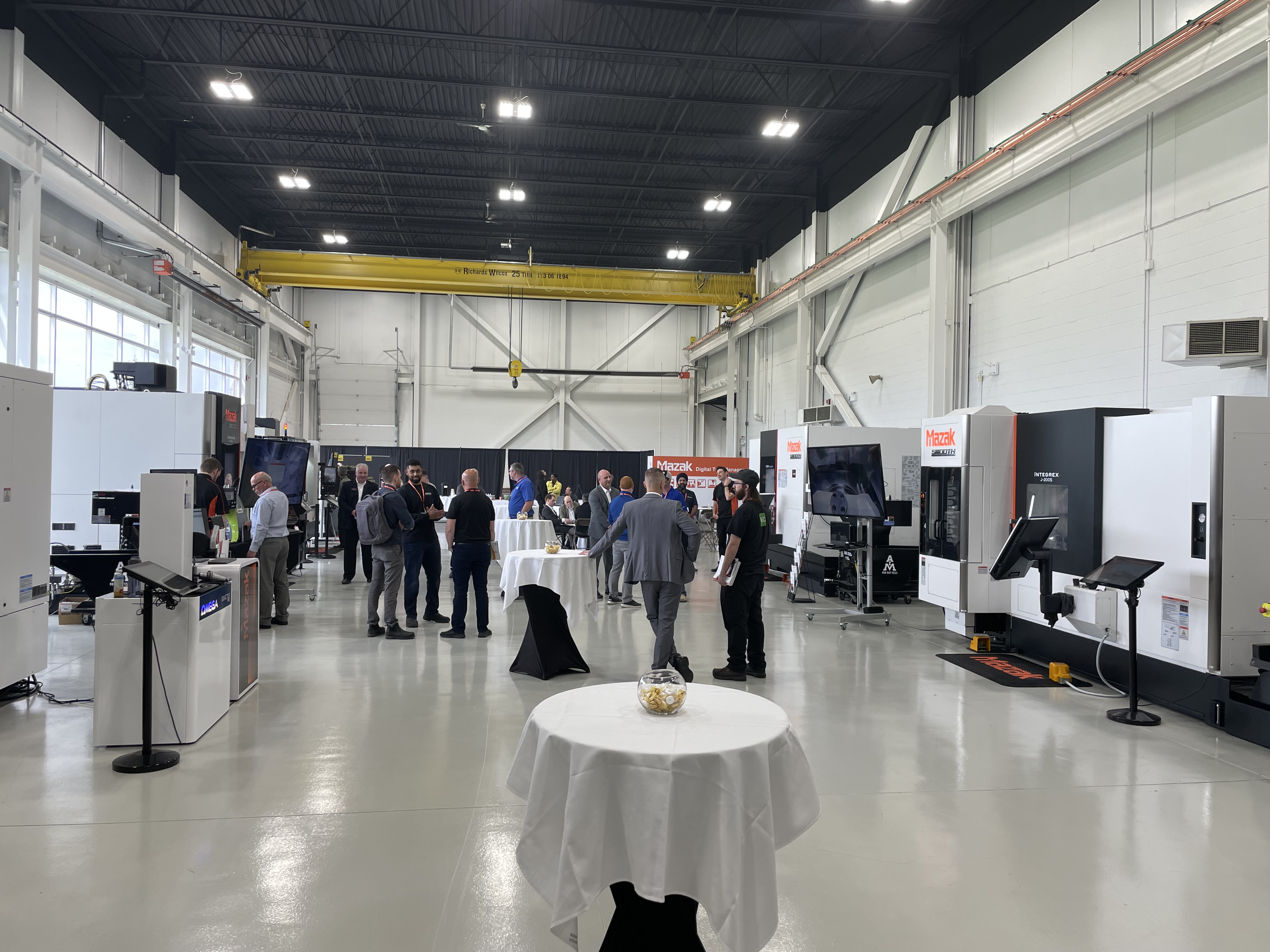
Both sites showed off turning centers, including the Quick Turn 450MY CNC turning center with multi-tasking capabilities that perform milling and turning in the same setup and was demonstrated to execute heavy roughing, drilling, boring, and threading.
In Cambridge, Mazak featured its HQR-200MSY twin-spindle, twin-turret turning center with two high-performance spindles along with upper and lower turrets that facilitate untended complete Done-In-One part processing as it cut aluminum trophies.
Also showcased in Edmonton and Cambridge was the Variaxis C-600 vertical machining center, which is considered a “first step” into 5-axis machining for some shops, the user-friendly and compact with a tilt table. The company also presented its VC-Ez 20 3-axis VMC, featuring Mazak’s Mazatrol SmoothEz CNC that provides dual 800 MHz processors, 512 MB of RAM, and a 15" capacitive touch screen that includes a full keyboard and displays up to 60 lines of code.
Mazak spotlighted AI and Smart monitoring analysis with its Smooth Monitor AX and Smooth CAM AI. Smooth Monitoring AX monitors, connects, and analyzes the performance of not only Mazak machines, but all machines in the factory for higher productivity and efficiency. The data can then be sent directly to the factory floor for fast machine setups and optimization.
Smooth CAM AI allows users to create multiple virtual machines, simulate performance, and analyze data from an office desktop. The data can then be sent directly to the factory floor for fast machine setups and optimization.
Visitors also learned how to reduce inspection setups from 15 minutes to 20 seconds using Mazak’s Smooth Set & Inspect software solution that integrates Renishaw inspection probes with Mazak’s CNC platform. Smooth Set & Inspect makes part setup, inspection, and tool setting as simple as answering a few questions and hitting a machine’s “cycle start” button.
Contact Details
Related Glossary Terms
- boring
boring
Enlarging a hole that already has been drilled or cored. Generally, it is an operation of truing the previously drilled hole with a single-point, lathe-type tool. Boring is essentially internal turning, in that usually a single-point cutting tool forms the internal shape. Some tools are available with two cutting edges to balance cutting forces.
- centers
centers
Cone-shaped pins that support a workpiece by one or two ends during machining. The centers fit into holes drilled in the workpiece ends. Centers that turn with the workpiece are called “live” centers; those that do not are called “dead” centers.
- computer numerical control ( CNC)
computer numerical control ( CNC)
Microprocessor-based controller dedicated to a machine tool that permits the creation or modification of parts. Programmed numerical control activates the machine’s servos and spindle drives and controls the various machining operations. See DNC, direct numerical control; NC, numerical control.
- computer-aided manufacturing ( CAM)
computer-aided manufacturing ( CAM)
Use of computers to control machining and manufacturing processes.
- gang cutting ( milling)
gang cutting ( milling)
Machining with several cutters mounted on a single arbor, generally for simultaneous cutting.
- machining center
machining center
CNC machine tool capable of drilling, reaming, tapping, milling and boring. Normally comes with an automatic toolchanger. See automatic toolchanger.
- milling
milling
Machining operation in which metal or other material is removed by applying power to a rotating cutter. In vertical milling, the cutting tool is mounted vertically on the spindle. In horizontal milling, the cutting tool is mounted horizontally, either directly on the spindle or on an arbor. Horizontal milling is further broken down into conventional milling, where the cutter rotates opposite the direction of feed, or “up” into the workpiece; and climb milling, where the cutter rotates in the direction of feed, or “down” into the workpiece. Milling operations include plane or surface milling, endmilling, facemilling, angle milling, form milling and profiling.
- threading
threading
Process of both external (e.g., thread milling) and internal (e.g., tapping, thread milling) cutting, turning and rolling of threads into particular material. Standardized specifications are available to determine the desired results of the threading process. Numerous thread-series designations are written for specific applications. Threading often is performed on a lathe. Specifications such as thread height are critical in determining the strength of the threads. The material used is taken into consideration in determining the expected results of any particular application for that threaded piece. In external threading, a calculated depth is required as well as a particular angle to the cut. To perform internal threading, the exact diameter to bore the hole is critical before threading. The threads are distinguished from one another by the amount of tolerance and/or allowance that is specified. See turning.
- turning
turning
Workpiece is held in a chuck, mounted on a face plate or secured between centers and rotated while a cutting tool, normally a single-point tool, is fed into it along its periphery or across its end or face. Takes the form of straight turning (cutting along the periphery of the workpiece); taper turning (creating a taper); step turning (turning different-size diameters on the same work); chamfering (beveling an edge or shoulder); facing (cutting on an end); turning threads (usually external but can be internal); roughing (high-volume metal removal); and finishing (final light cuts). Performed on lathes, turning centers, chucking machines, automatic screw machines and similar machines.