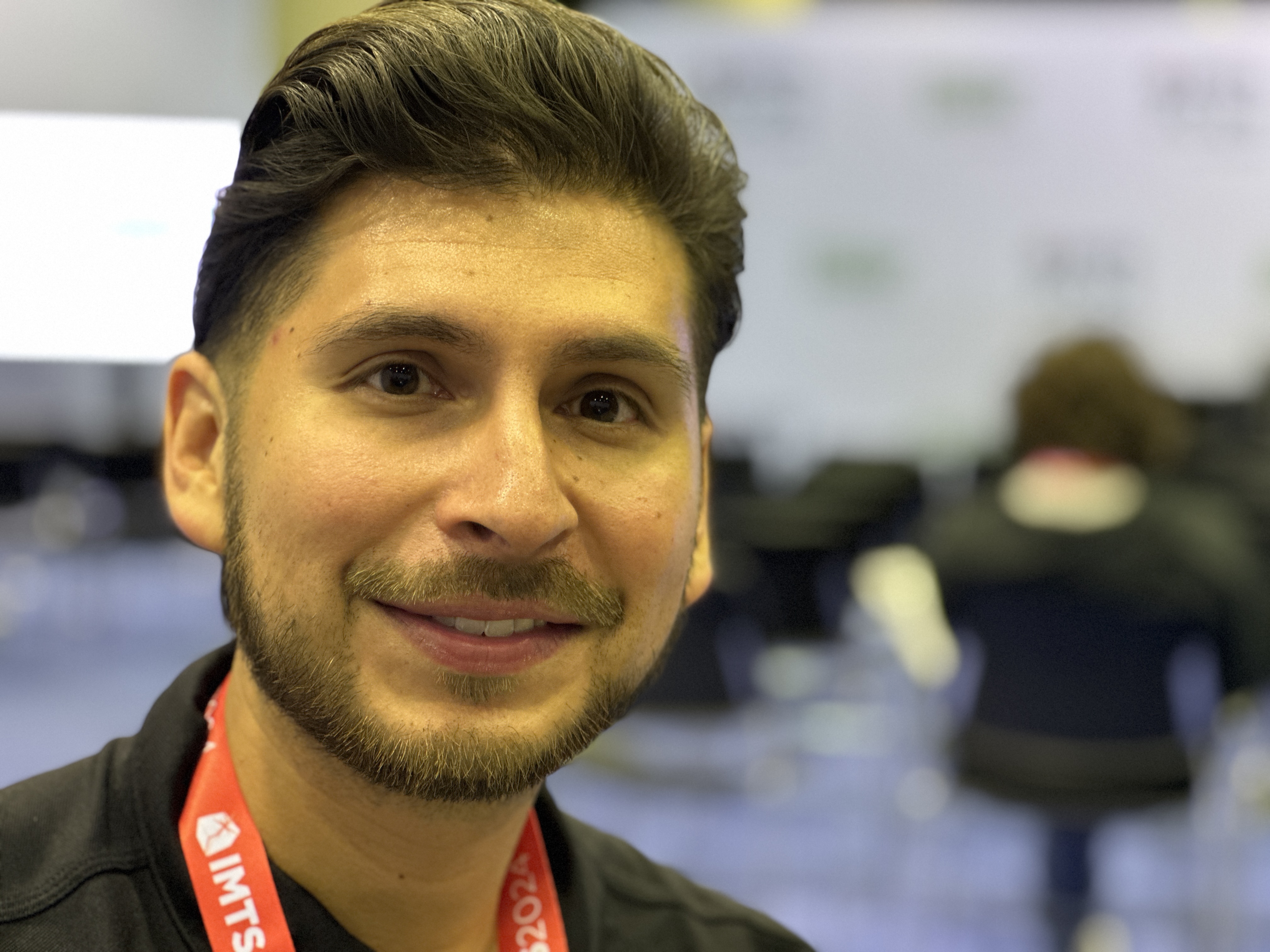
Rodrigo Perez’s journey into the world of manufacturing began during high school, but not in a classroom. While working construction for his father, Perez crossed paths with an electronics engineer who taught him about machining and manufacturing; how to use a mill and a lathe; how to put together circuit boards; how to solder surface components and wires, and build robotic computer systems.
Today, Perez serves as a senior systems integration engineer at MxD (Manufacturing Times Digital), a Department of Defense-funded research institute that is part of Manufacturing USA, a national network created to secure U.S. global leadership in advanced manufacturing through large-scale public-private collaboration on technology, supply chain, education and workforce development. But the career path that led Perez to his current role was anything but linear.
Perez, who shared that journey during the IMTS 2024 Smartforce Student Summit as part of the Manufacturing USA Modern Makers panel, sat for an interview with Cutting Tool Engineering shortly after the event. He shared the twists and turns that led him to a career in advanced manufacturing, as well as some insights into the future of digital manufacturing and the importance of involving younger generations in the field.
A Childhood of Curiosity
Perez’s interest in engineering stemmed from an early love of puzzles and an innate curiosity about how things worked. “I used to take apart bicycles and mix and match parts to make them faster,” he recalled. “I didn’t fully understand it at the time, but I knew I wanted to figure out how things worked.” That same curiosity followed him into high school, where he began taking drafting classes, solidifying his interest in pursuing a career in engineering.
He eventually attended Northern Illinois University, where he majored in mechanical engineering with a focus on mechatronics, a multidisciplinary field that integrates mechanical, electrical and computer engineering.
From Construction to Manufacturing
Perez’s first taste of engineering came through an unlikely connection. “I started off working for an electronics engineer while doing construction work with my dad,” he shared. This experience opened his eyes to the possibilities of engineering, as he learned hands-on skills like machining and operating tools such as mills and lathes.
His first formal role in manufacturing was an internship at the former Federal-Mogul Corp., a Skokie, Illinois-based automotive supplier acquired by Tenneco in 2018. “That’s where I first saw stamping presses in action and learned about tools and dies,” he said. “It was an eye-opening experience for me as I got to understand large-scale manufacturing.” This pivotal moment helped Perez realize that manufacturing, with its blend of hands-on work and problem-solving, was where his passion truly lay.
Finding His Way Back to Manufacturing
After graduating from NIU, Perez spent a brief time working for a mechanical, electrical and plumbing systems consulting firm. “I quickly realized I missed the action of manufacturing, so I switched paths,” he said. This switch led him to work on sensor applications for industries like aerospace that allowed him to learn how to work with thermocouples, resistive temperature devices and heater cables.
However, as the COVID-19 pandemic disrupted industries worldwide, Perez found himself once again rethinking his career. It was during this time that he began working with robotics and automation at B-O-F Corp. in Aurora, Illinois. “I liked it a lot,” Perez said of his time at B-O-F, where he worked in R&D and quality assurance. It is also where he developed a keen interest in the Internet of Things (IoT).
When he joined MxD in 2022, he noted, “I saw firsthand how data could be leveraged in manufacturing processes. That really opened my eyes to the potential of IoT in industrial settings.”
Digital Manufacturing and the Future
At MxD, Perez works on digital manufacturing projects that involve using data to optimize manufacturing processes.
“When we talk about digital manufacturing, it’s not just about making parts anymore — it’s about generating and using data to make informed decisions,” he explained. By integrating IoT into industrial settings, companies can identify inefficiencies and improve their operations based on the data their machines are generating. “We help companies understand their processes and how digital tools can enhance them,” he said.
But Perez is quick to point out that implementing technology alone isn’t enough. "There’s a misconception that technology will fix problems. You just plug it in, and it solves everything,” he noted. “But sometimes it comes down to solving the underlying issues first.
“There’s a lot of pre-planning before we start any modernization project,” Perez explained. “We do a detailed assessment to understand the company’s goals and pain points. Then we map out a strategy based on their specific needs.”
Inspiring the Next Generation
Now 32, Perez said he enjoys sharing his story to help inspire the next generation of engineers and promote manufacturing careers. As a child, Perez said he always wanted guidance but didn’t know how to find it.
“I just got lucky and crossed paths with someone who was willing to help me,” he said, noting that it would have been a game-changer for him if he had been exposed to manufacturing careers during middle school or high school. He encourages young people to get involved in engineering and manufacturing sooner rather than later. “Once I started connecting with manufacturers and engineering groups, things started to click,” he explained. “If I had started earlier, it would have made an even bigger difference.”
The Future of Manufacturing
Perez is optimistic about the future of manufacturing, particularly as digital tools continue to evolve and become more integrated into industrial processes. However, he emphasized that it’s not just about technology — it’s about the people who work together to make these advancements possible.
“Manufacturing is all around us,” he said. “It’s connected to everything we experience in life.” By helping companies harness the power of data and digital tools, Perez is playing a key role in shaping the future of the industry.
As he reflects on his own journey, from a curious kid taking apart bicycles to a systems integration engineer at MXD, Perez embodies the spirit of a “Modern Maker” — a person who not only understands the importance of technology but also recognizes the value of mentorship, collaboration and lifelong curiosity.
Related Glossary Terms
- milling machine ( mill)
milling machine ( mill)
Runs endmills and arbor-mounted milling cutters. Features include a head with a spindle that drives the cutters; a column, knee and table that provide motion in the three Cartesian axes; and a base that supports the components and houses the cutting-fluid pump and reservoir. The work is mounted on the table and fed into the rotating cutter or endmill to accomplish the milling steps; vertical milling machines also feed endmills into the work by means of a spindle-mounted quill. Models range from small manual machines to big bed-type and duplex mills. All take one of three basic forms: vertical, horizontal or convertible horizontal/vertical. Vertical machines may be knee-type (the table is mounted on a knee that can be elevated) or bed-type (the table is securely supported and only moves horizontally). In general, horizontal machines are bigger and more powerful, while vertical machines are lighter but more versatile and easier to set up and operate.
- quality assurance ( quality control)
quality assurance ( quality control)
Terms denoting a formal program for monitoring product quality. The denotations are the same, but QC typically connotes a more traditional postmachining inspection system, while QA implies a more comprehensive approach, with emphasis on “total quality,” broad quality principles, statistical process control and other statistical methods.
- robotics
robotics
Discipline involving self-actuating and self-operating devices. Robots frequently imitate human capabilities, including the ability to manipulate physical objects while evaluating and reacting appropriately to various stimuli. See industrial robot; robot.
- sawing machine ( saw)
sawing machine ( saw)
Machine designed to use a serrated-tooth blade to cut metal or other material. Comes in a wide variety of styles but takes one of four basic forms: hacksaw (a simple, rugged machine that uses a reciprocating motion to part metal or other material); cold or circular saw (powers a circular blade that cuts structural materials); bandsaw (runs an endless band; the two basic types are cutoff and contour band machines, which cut intricate contours and shapes); and abrasive cutoff saw (similar in appearance to the cold saw, but uses an abrasive disc that rotates at high speeds rather than a blade with serrated teeth).
- shaping
shaping
Using a shaper primarily to produce flat surfaces in horizontal, vertical or angular planes. It can also include the machining of curved surfaces, helixes, serrations and special work involving odd and irregular shapes. Often used for prototype or short-run manufacturing to eliminate the need for expensive special tooling or processes.