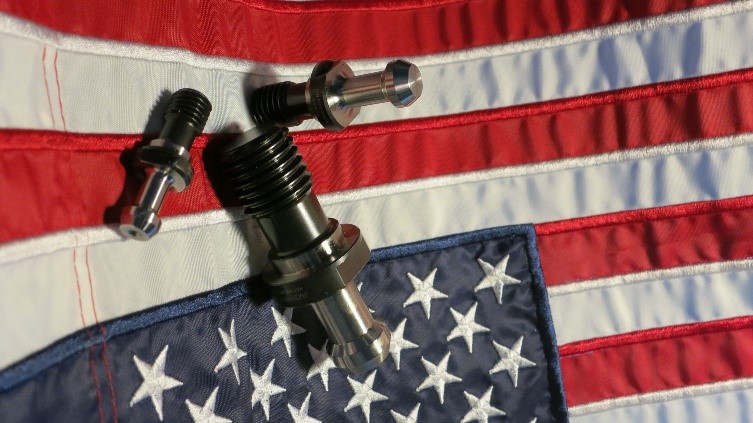
JM Performance Products and The Reshoring Initiative analyze “near-post-COVID” parameters with a trajectory focus on training, technology, supply chain, production, and reshoring.
The COVID-19 pandemic has spurred a national push to strengthen the domestic supply chain, especially of essential products, which are driving reshoring numbers higher.
The following Q&A is designed to share insights on how today’s companies can address, and prevent, post-pandemic supply chain disruptions, advance manufacturing productivity, and reskill workforces.
Participating in this “Post-COVID-Reshoring-OPS” Q&A are two representative entities with vested interest on the subject: John Stoneback, owner of JM Performance Products Inc. (JMPP) in Fairport Harbor, Ohio; and, Harry Moser, founder and president of the Reshoring Initiative (RI) in Kildeer, Illinois.
JMPP has manufactured CNC mill spindle optimization products since 2009. Its High Torque Retention Knobs overcome a critical design flaw inherent in CNC v-flange tooling that is responsible for costly CNC milling and boring issues.
The Reshoring Initiative, founded in early 2010, takes action to bring five million manufacturing jobs back to the US by helping manufacturers realize that local production, in some cases, reduces their total cost of ownership of purchased parts and tooling. The RI also trains suppliers how to effectively meet the needs of their local customers−giving the suppliers the tools to sell against lower-priced offshore competitors. The RI is a nonprofit organization that offers a number of free tools to advance their mission.
Aftermath effects?
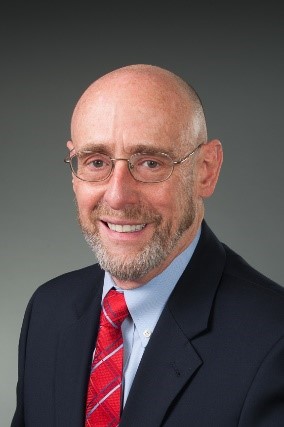
Moser: From a reshoring perspective it’s clear that government, consumers, and companies must understand that a global and fractured extended supply chain is not good. Reducing our dependence on foreign countries and corporations for critical technology and products is critical. Quite simply, we need to source more in North America, with the US getting the bulk of it. Without having to worry about geopolitics and the US/China ports (where things can go wrong), the risk comes down dramatically.
Many experts feel that China will begin to voluntarily decouple as a strategic shift, whereby they switch their focus from economic growth to economic control. China is furious because of the US resisting their efforts in the Western Pacific−particularly the protection of Hong Kong and Taiwan. If they are convinced that we’re trying to cut them off from their maritime supply chain, China may announce at some time that no Chinese company will ship to the US.
They could also mandate their populace to just buy China-based products. This is made more plausible as 40% of Chinese income is saved by their populace vs. 3-5% for the US−making it easier for them to replace their dependency on us.
I believe it’s a question of degree where they may pick the 5 to 10 things that we need most (i.e.-penicillin, semiconductors, cell phones). If they tried this 20 years ago it wouldn’t have worked because they needed us more. Now, we need them more as we have nowhere else to go for some of these vital items.
Other geopolitical landscape scenarios exist as well, such as Cuba being positioned to block trade from many areas in/out of the Caribbean. The question is, will Cuba, a target for China, help them financially/militarily to block the U.S.? In many ways, the U.S. is doing the same thing in Taiwan, [and] Philippines. This is a very extreme scenario, but also very possible on a percentage level as I believe these trends will continue.
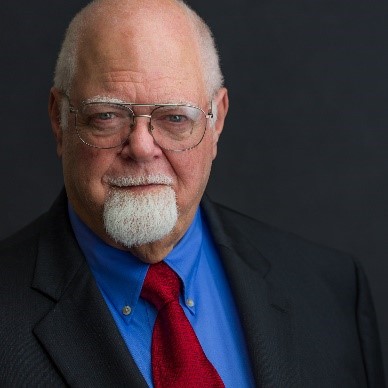
Stoneback: From a small manufacturing perspective, we all need to recognize that we are never going to experience “business as usual” pre-COVID-19. The supply chain disruption has affected every manufacturer, whether they are a small “Mom & Pop” shop or a multi-national entity. We are all being forced to examine our business practices and modify them, so that we can continue to produce our products with better efficiencies while controlling escalating costs.
Everything from buying steel to semi-conductors has been affected. Quoting has taken on a new level of difficulty because lead times are no longer predictable or dependable. Add to that the lack of skilled labor available, and the new deficit of people willing to work, and U.S. manufacturers are now playing the game with a whole different set of rules.
The current domestic “hyper-inflation” has to be taken seriously. The cost of everything from food and clothing, to fuel and housing has jumped dramatically. The unfortunate reality is that many items are still significantly less expensive if they are imported. The challenge of making every dollar stretch further opens an argument that higher costing domestically produced goods are an extravagance. Changing that mind-set is a necessary, but daunting task. Additionally, we all need to recognize that the demand for higher wages to offset the escalating costs, and devaluation of the dollar is imminent. What affect will this additional layer have on reshoring? This is a question every business owner, especially manufacturers, needs to examine.
JM Performance Products is staunch about making our products here in the USA from domestic steel, and having to justify our cost over an import is our day-to-day challenge.
The fact of the matter is, we can and do guarantee our quality and performance. If an imported part fails, what is the remedy? A failure of our products, retention knobs, can cause catastrophic damage resulting in production down-time and repairs. It is highly unlikely that a cheap import comes with any sort of guarantee or cost mitigation policy. The reality is that paying more up-front often means saving money down the road; but that is a difficult message to convey.
Biggest/most immediate challenge?
Moser: The good news is that the reshoring effort has been on a successful track in bringing back manufacturing jobs to the U.S.−6,000 in 2010, 160,000 in 2020, and 200,000 or more in 2021. This is still not enough growth needed to reduce the trade deficit and reach the goal of bringing back 500,000 jobs per year. Even if we reached that goal, we wouldn’t have the skilled (and unskilled) workers trained to handle the work at that pace.
Therefore, the biggest challenge/obstacle is the skilled workforce, and we need to establish recruiting the unskilled and skilled via aggressive apprenticeship programs for beginners and support college funding to go even further. Lower-level jobs will benefit immediately from apprentice programs as social recruitment of manufacturing careers is key−with guidance counselors leading the way.
The second biggest challenge is to get the dollar down 20%. Also, don’t raise the corporate income tax as it will dissuade companies from building new manufacturing facilities. Moving forward, we also need to adopt a value-added tax credit of 15% on every level of the supply chain (steel, etc.) for exports.
Today, if a Chinese company ships to the U.S., China gives that company a 15% value-added tax/credit. We need to do this as well, as it is a critical incentive over and above taxes, duties, and tariffs.
Stoneback: I agree with Harry. We need to incentivize North American manufacturers while protecting them by leveling the financial playing field. For many small manufacturers, higher corporate income tax will only dilute their efforts to grow and expand. It will also have a negative impact on their workforce.
Today's global supply chain
Moser: Delivery time is at least 50% longer to get to the U.S., as there is still a good amount of inventory of products stuck on ships and docks. Across the board, there are shortages in distribution centers and stores, and imported products are still the problem for companies waiting for materials to get here. Quite simply, if you use domestic materials and labor, you’ll have fewer issues.
Stoneback: Many manufacturers fail to recognize that the costs to use imported materials have to include the cost of added time, added transportation, and quite honestly, reduced quality in many instances. Yes, we may have to pay more at first blush, but the cost of buying domestic materials is easily calculated.
Global supply chain changes?
Moser: Ultimately, more reshoring and foreign direct investment (FDI) may benefit local firms in the host country through various kinds of spillovers to recognize total cost vs. just the price.
I recently participated in a podcast for the AME (Association for Manufacturing Excellence), which is a lean-focused organization that helps manufacturers successfully navigate the post-pandemic economy. We all agreed that JIT is a lean concept and we do need to get leaner. The problem is that JIT is a problem when you have no inventory and depend on products coming from foreign countries vs. domestic-based.
This still comes down to a sourcing problem where we need to be leaner by sourcing more locally. If we can overcome that problem−JIT will work just fine.
Stoneback: Sourcing local is key. JMPP currently manufactures and stocks over 400 different styles of retention knobs, so JIT local sourcing isn’t an issue for our customers. Additionally, we recently developed coupling bolts for live tooling on CNC lathes from Mazak Corp. in Florence, Ky., which are now available for immediate shipment–eliminating the traditional long lead times for comparable imported coupling bolts for Mazak CNC lathes.
Drought in available/willing employees
Moser: In many cases, employees have been afraid to come back to work because of COVID-19. Also, government stimulus aid has de-incentivized some from working, but I feel they’ll come back as funds run low and the pandemic continues to subside. The big challenge for manufacturers will be to get their share of those employees coming back to manufacturing.
Stoneback: Our domestic policies need to change. We have to stop paying people to not work. No one wants to cause anyone any harm, but there needs to be a limit to what an able-bodied person should receive in assistance.
The post-COVID-19 landscape
Moser: The current administration’s enhanced efforts are focused on manufacturing essential materials for precarious industries such as microchips, rare minerals, medicine, and EV batteries. We can’t be dependent on outsourcing so we must boost production at home. The problem is, for example, we can increase microchip manufacturing capacity, but our chips will be too high priced to compete. The emerging chip factories must get costs down to have a competitive US market here for all the chips, as they are 20-30% cheaper to source from overseas. Plus, overseas is also our customer.
Notably, for the second year in a row, reshoring job announcements outpaced FDI – 62% vs. 38% (historically very high but lower than last year’s rate of 70% reshoring, 30% FDI.) Exhibit 1 notes the number of companies reporting new reshoring and FDI is also set for a new annual record: 1,800+ companies
Post-COVID-9 revelations and insights
Moser: Again, a skilled workforce is the number one priority, plus automation and improving the trade balance are key. Germany is the best example of this as their trade balance is a surplus of 5% of Gross Domestic Product (GDP), whereas the US is at negative 4%. Germany also has a better skilled work force, as manufacturing is 21% of their employment and the US is at 9%. It is also essential to get the dollar down.
Stoneback: While I agree with Harry that a skilled workforce is a priority, I also believe that adopting innovative processes that augment the skill level of our work force is key. Taking a hard look at production bottle necks, and working to simplify processes so that capable, but not necessarily highly skilled workers can maintain the work flow, should always remain a consideration.
What can the Reshoring Initiative do?
Moser: The Reshoring Initiative offers the Total Cost of Ownership (TCO) Estimator. It’s a free, online software that helps companies make better sourcing decisions about offshore vs. domestic sourcing, and is also used to sell against imports. The tool asks the companies to look at what products are causing “pain” via “hidden costs.” They can use the TCO to find the products where the hidden costs are greater than the price gap.
We also offer the Import Substitution Program (ISP), where companies can identify the right products to make and it qualifies the biggest importers of their product. The ISP was created to convince and facilitate importing companies to produce or source more domestically. Customized versions of ISP are available for U.S. manufacturing companies, technology suppliers, and trade associations.
These are unique tools that can become an important part of any sales, marketing, or economic development effort to make smarter sales decisions. Ultimately, lots of jobs are coming back (~20%) so this could increase US manufacturing by 30%. If 2H2021 progresses at the same rate as 1H2021, reshoring and FDI job announcements for 2021 are projected to be over 220,000, which is 38% above 2020 and, by far, the highest yearly number recorded to date.
Given these statistics, and using these tools to do the math and figure it out, manufacturers should have confidence moving forward that it can be done so we can then actively hire, train, and build more factories.
Conclusion
With an effective vaccine in place, and the COVID-19 crisis nearly over (apart from the new Omicron variant threat), the negative effects have still permeated the US manufacturing community at every turn and will continue to do so for the foreseeable future–and beyond. Actively addressing the challenges at the forefront as a result of this pandemic can ultimately create opportunities that pave the way for a stronger, more sustainable US foundation for the future–with advanced manufacturing, training, and reshoring as the essential bedrock.
For more detailed information, click here.
Contact Details
Related Glossary Terms
- boring
boring
Enlarging a hole that already has been drilled or cored. Generally, it is an operation of truing the previously drilled hole with a single-point, lathe-type tool. Boring is essentially internal turning, in that usually a single-point cutting tool forms the internal shape. Some tools are available with two cutting edges to balance cutting forces.
- centers
centers
Cone-shaped pins that support a workpiece by one or two ends during machining. The centers fit into holes drilled in the workpiece ends. Centers that turn with the workpiece are called “live” centers; those that do not are called “dead” centers.
- computer numerical control ( CNC)
computer numerical control ( CNC)
Microprocessor-based controller dedicated to a machine tool that permits the creation or modification of parts. Programmed numerical control activates the machine’s servos and spindle drives and controls the various machining operations. See DNC, direct numerical control; NC, numerical control.
- gang cutting ( milling)
gang cutting ( milling)
Machining with several cutters mounted on a single arbor, generally for simultaneous cutting.
- just-in-time ( JIT)
just-in-time ( JIT)
Philosophy based on identifying, then removing, impediments to productivity. Applies to machining processes, inventory control, rejects, changeover time and other elements affecting production.
- milling
milling
Machining operation in which metal or other material is removed by applying power to a rotating cutter. In vertical milling, the cutting tool is mounted vertically on the spindle. In horizontal milling, the cutting tool is mounted horizontally, either directly on the spindle or on an arbor. Horizontal milling is further broken down into conventional milling, where the cutter rotates opposite the direction of feed, or “up” into the workpiece; and climb milling, where the cutter rotates in the direction of feed, or “down” into the workpiece. Milling operations include plane or surface milling, endmilling, facemilling, angle milling, form milling and profiling.
- milling machine ( mill)
milling machine ( mill)
Runs endmills and arbor-mounted milling cutters. Features include a head with a spindle that drives the cutters; a column, knee and table that provide motion in the three Cartesian axes; and a base that supports the components and houses the cutting-fluid pump and reservoir. The work is mounted on the table and fed into the rotating cutter or endmill to accomplish the milling steps; vertical milling machines also feed endmills into the work by means of a spindle-mounted quill. Models range from small manual machines to big bed-type and duplex mills. All take one of three basic forms: vertical, horizontal or convertible horizontal/vertical. Vertical machines may be knee-type (the table is mounted on a knee that can be elevated) or bed-type (the table is securely supported and only moves horizontally). In general, horizontal machines are bigger and more powerful, while vertical machines are lighter but more versatile and easier to set up and operate.