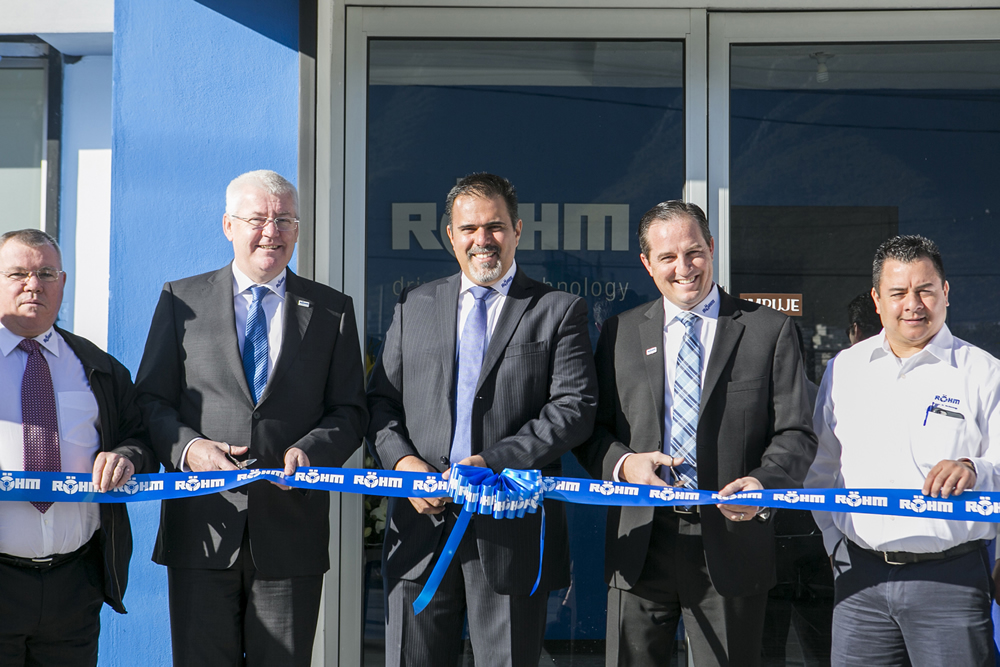
Röhm Products Mexico S. de R.L. de C.V., a subsidiary of Röhm GmbH, recently opened a new office in Monterrey, Mexico, in an effort to expand the company's sales, service and support capabilities to meet increasing demand for high-quality clamping and gripping technology throughout Mexico and Central America, the company reported in a Feb. 22 news release.
At a ribbon-cutting ceremonty held Feb. 11, machine tool and industrial dealers learned how the new office will enable them to better serve their diverse customers in a wide range of industries such as aerospace, automotive, energy and oil and gas. Röhm also provided general sales training on how to engage and influence existing customers, as well as acquire new ones.
"This new office positions us to grow our team that serves customers in Mexico and Central America and to more efficiently help local customers get the maximum return on their Röhm purchases," explained Rodolfo Espeleta, managing director of Röhm Products Mexico. He added that Monterrey is an ideal location for Röhm’s new office because of its close proximity to the U.S. border and airport.
Röhm Products Mexico, which began operation in 2014, provides a comprehensive array of more than 15,000 products that includes chucks, centers, vices, tool clamping and automation systems as well as customized solutions for turning, milling, drilling and grinding.
Contact Details
Related Glossary Terms
- centers
centers
Cone-shaped pins that support a workpiece by one or two ends during machining. The centers fit into holes drilled in the workpiece ends. Centers that turn with the workpiece are called “live” centers; those that do not are called “dead” centers.
- gang cutting ( milling)
gang cutting ( milling)
Machining with several cutters mounted on a single arbor, generally for simultaneous cutting.
- grinding
grinding
Machining operation in which material is removed from the workpiece by a powered abrasive wheel, stone, belt, paste, sheet, compound, slurry, etc. Takes various forms: surface grinding (creates flat and/or squared surfaces); cylindrical grinding (for external cylindrical and tapered shapes, fillets, undercuts, etc.); centerless grinding; chamfering; thread and form grinding; tool and cutter grinding; offhand grinding; lapping and polishing (grinding with extremely fine grits to create ultrasmooth surfaces); honing; and disc grinding.
- milling
milling
Machining operation in which metal or other material is removed by applying power to a rotating cutter. In vertical milling, the cutting tool is mounted vertically on the spindle. In horizontal milling, the cutting tool is mounted horizontally, either directly on the spindle or on an arbor. Horizontal milling is further broken down into conventional milling, where the cutter rotates opposite the direction of feed, or “up” into the workpiece; and climb milling, where the cutter rotates in the direction of feed, or “down” into the workpiece. Milling operations include plane or surface milling, endmilling, facemilling, angle milling, form milling and profiling.
- turning
turning
Workpiece is held in a chuck, mounted on a face plate or secured between centers and rotated while a cutting tool, normally a single-point tool, is fed into it along its periphery or across its end or face. Takes the form of straight turning (cutting along the periphery of the workpiece); taper turning (creating a taper); step turning (turning different-size diameters on the same work); chamfering (beveling an edge or shoulder); facing (cutting on an end); turning threads (usually external but can be internal); roughing (high-volume metal removal); and finishing (final light cuts). Performed on lathes, turning centers, chucking machines, automatic screw machines and similar machines.