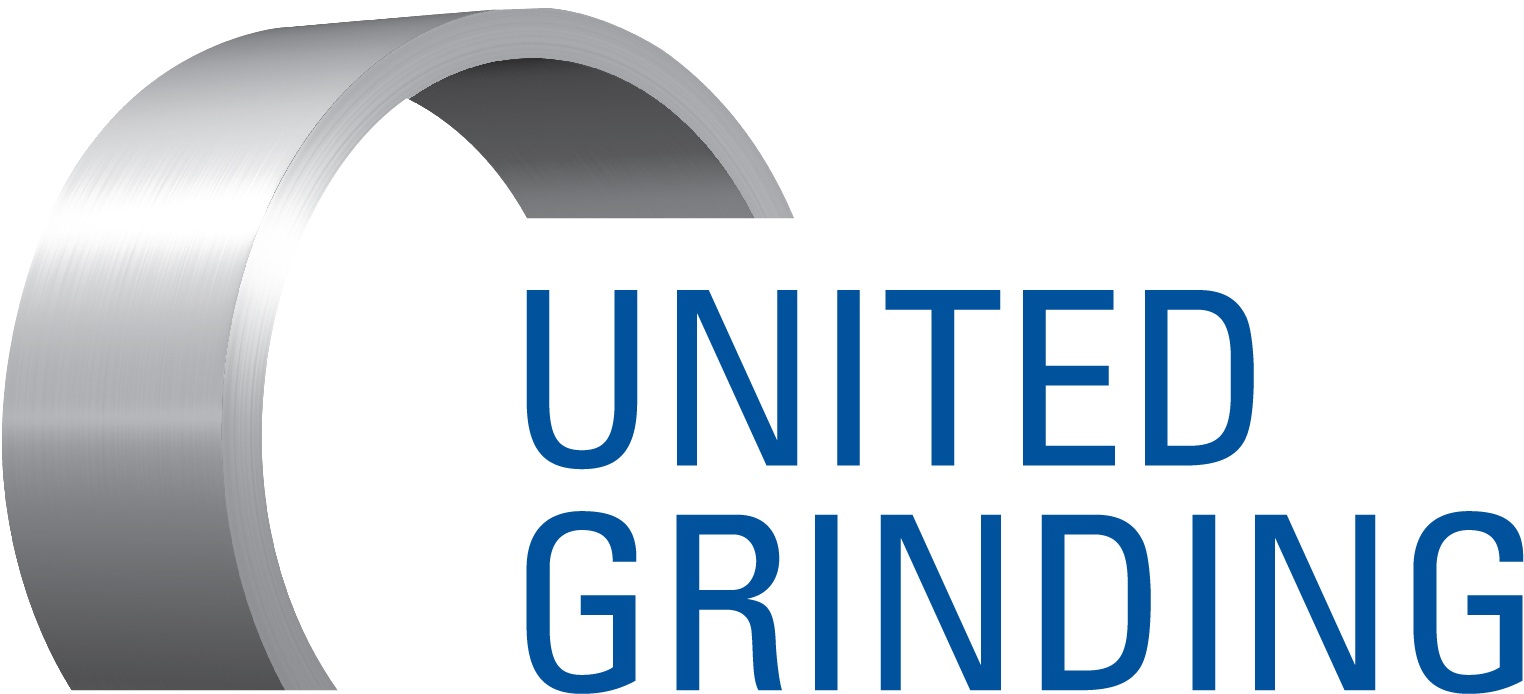
The United Grinding Group, a leading manufacturer of grinding, eroding, laser and measuring machines, is showcasing 16 grinding machines, new innovations and updates from its Customer Care team at the EMO 2023 trade show in Hannover, Germany.
The show is scheduled for Sept. 18 to 23. With its special exhibition area this year in Hall 11, Booth E34, the Group is placing a focus on Customer Care. This includes all products and services that accompany customers during the service life of their machines and support them in efficient production, all the way from start-up to retrofit.
Visitors will also get information about all of United Grinding’s digital assistance systems. These include Production Monitor, Service Monitor and Remote Service, which are grouped under the Digital Solutions offering. In addition, the latest digital solutions will be presented at EMO.
On top of this, booth visitors can look forward to several innovations and highlights among the 16 machines on display:
- Blohm, the surface and profile grinding machine specialist, is celebrating a world premiere: the Planomat XT 408 with automatic workpiece loading and unloading. An exciting new solution for the internal machining of hydraulic motor stators.
- Studer will also have a cylindrical reveal: an innovative automation solution that will be on display on the S31 universal external cylindrical grinding machine.
- Walter will present the innovative Laser Contour Check measuring system for the first time at EMO. The tool grinding feature results in highly accurate, non-contact measurement of various tool parameters on cylindrical tools, which is now also available as an option for the Helitronic Micro and Helitronic Mini Plus tool grinding machines.
The machines also allow users to experience groundbreaking C.O.R.E. technology. This proprietary operating system creates the basis for a new generation of machine tools, with simple networking, intuitive smartphone-like operation and the ability to use modern software applications directly on the machine.
Contact Details
Related Glossary Terms
- cylindrical grinding
cylindrical grinding
Grinding operation in which the workpiece is rotated around a fixed axis while the grinding wheel is fed into the outside surface in controlled relation to the axis of rotation. The workpiece is usually cylindrical, but it may be tapered or curvilinear in profile. See centerless grinding; grinding.
- grinding
grinding
Machining operation in which material is removed from the workpiece by a powered abrasive wheel, stone, belt, paste, sheet, compound, slurry, etc. Takes various forms: surface grinding (creates flat and/or squared surfaces); cylindrical grinding (for external cylindrical and tapered shapes, fillets, undercuts, etc.); centerless grinding; chamfering; thread and form grinding; tool and cutter grinding; offhand grinding; lapping and polishing (grinding with extremely fine grits to create ultrasmooth surfaces); honing; and disc grinding.
- grinding machine
grinding machine
Powers a grinding wheel or other abrasive tool for the purpose of removing metal and finishing workpieces to close tolerances. Provides smooth, square, parallel and accurate workpiece surfaces. When ultrasmooth surfaces and finishes on the order of microns are required, lapping and honing machines (precision grinders that run abrasives with extremely fine, uniform grits) are used. In its “finishing” role, the grinder is perhaps the most widely used machine tool. Various styles are available: bench and pedestal grinders for sharpening lathe bits and drills; surface grinders for producing square, parallel, smooth and accurate parts; cylindrical and centerless grinders; center-hole grinders; form grinders; facemill and endmill grinders; gear-cutting grinders; jig grinders; abrasive belt (backstand, swing-frame, belt-roll) grinders; tool and cutter grinders for sharpening and resharpening cutting tools; carbide grinders; hand-held die grinders; and abrasive cutoff saws.