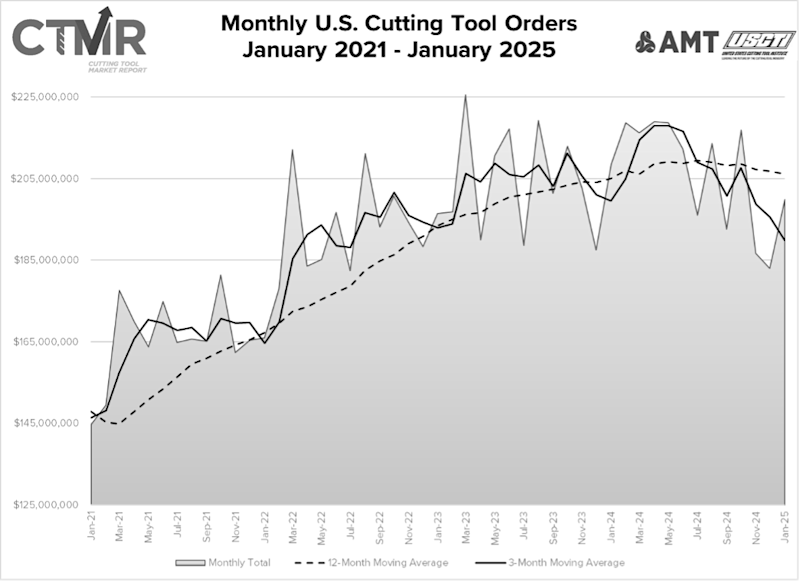
Shipments of cutting tools in January 2025 were up compared to December 2024, but fell compared to January 2024. The dive reflected a softer than normal market in January.
According to the Cutting Tool Market Report compiled in a collaboration between AMT – The Association For Manufacturing Technology and the U.S. Cutting Tool Institute (USCTI), shipments totaled $199.9 million in January 2025, which was an increase of 9.2% from December 2024 but were down 4.1% from January 2024.
“January was quite soft for most tooling companies, even more so than normal. New investments are on hold, and most shops are only buying what they need to keep spindles turning,” said Jack Burley, chairman of AMT’s Cutting Tool Product Group. “Until the political conditions settle and the uncertainty they create for manufacturing is resolved, I expect to see very little improvement in consumption, especially for small businesses. There are different opinions on the speed at which we can bring more manufacturing back to the United States, so we can only wait and see how companies respond.”
Eli Lustgarten, president at ESL Consultants, said, “Demand continues to suffer from economic uncertainty both here and abroad as well as from the changing political environment, especially with rising tariffs and the impact on supply chains and costs.
"Most major industrial end markets have become cautious: Heavy manufacturing sectors, including farm, construction, and mining equipment manufacturers, are undergoing substantial inventory liquidation in the first half of 2025. Signs point to a sluggish, if not volatile, first half of 2025. If political conditions and tariffs stabilize, end-market demand may begin to improve in the second half of the year and into 2026 as production increases and inventory liquidation ends.”
Contact Details
Related Glossary Terms
- turning
turning
Workpiece is held in a chuck, mounted on a face plate or secured between centers and rotated while a cutting tool, normally a single-point tool, is fed into it along its periphery or across its end or face. Takes the form of straight turning (cutting along the periphery of the workpiece); taper turning (creating a taper); step turning (turning different-size diameters on the same work); chamfering (beveling an edge or shoulder); facing (cutting on an end); turning threads (usually external but can be internal); roughing (high-volume metal removal); and finishing (final light cuts). Performed on lathes, turning centers, chucking machines, automatic screw machines and similar machines.