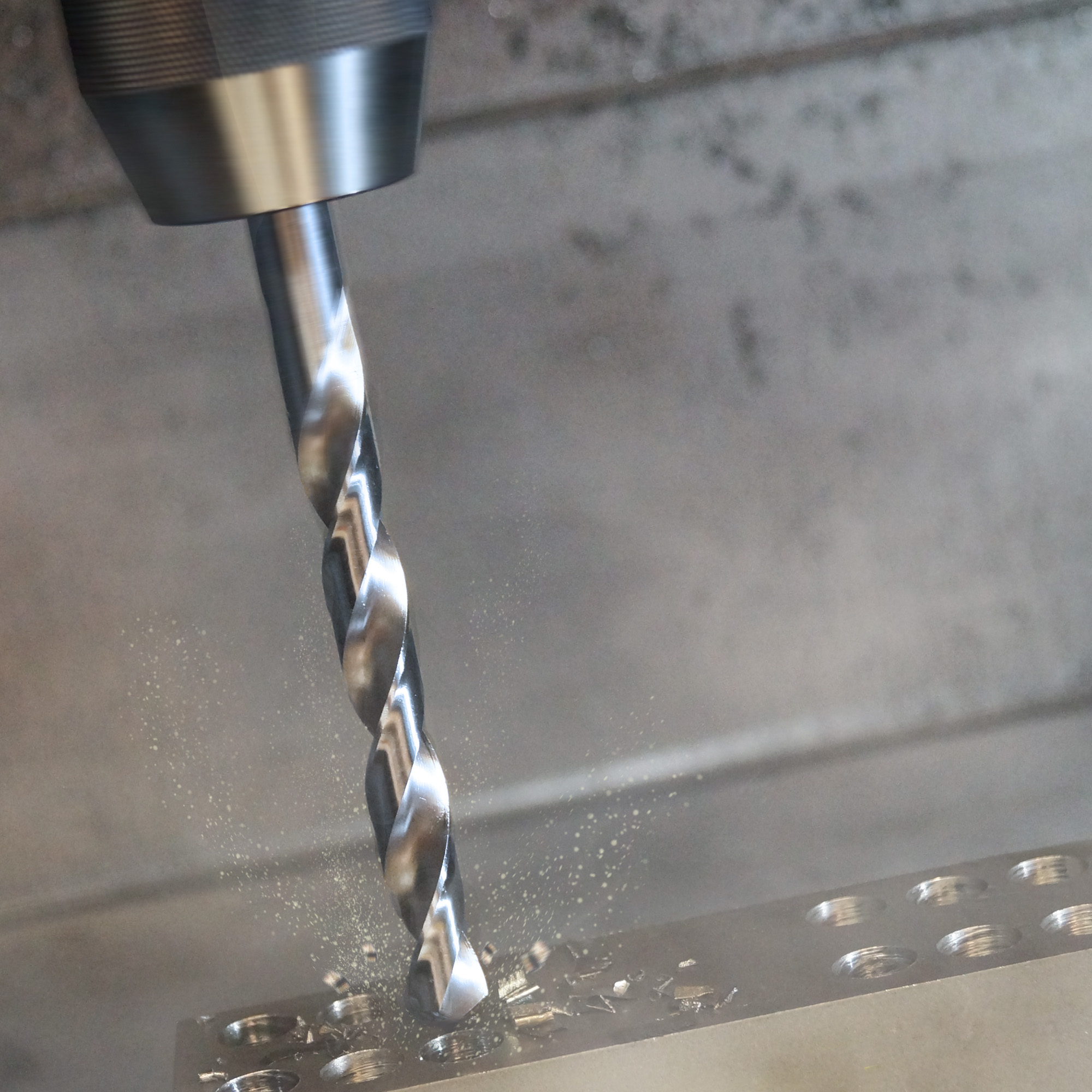
While looking through back issues of Carbide Engineering from the late 1950s, I came across an article about HSS cutting tools that reminded me of an article we published in this year’s August issue of Cutting Tool Engineering. (Editor’s note: Carbide Engineering combined with Cutting Tool Engineering starting with the January 1961 issue and dropped Carbide Engineering starting in April of that year. The publication began in 1948 as a small pamphlet called Carbide Tips, but I’m not aware of any existing copies of any issues.)
The March 1959 article was titled “High Speed Steel Ain’t Dead Yet!” by John F. McAuliffe, supervisor of cutting tool research at Pratt & Whitney Co. Inc., West Hartford, Connecticut. He covered the ability of HSS to retain a high percentage of its hardness at elevated temperatures and how HSS is much “tougher” than carbide, which means that it can withstand greater impact loads. This toughness enables HSS tools to excel when interrupted cutting.
The August 2018 article, titled “Traditional HSS Tools Meet Needs of Today,” covers the same territory. It was written by Gary Kirchoff and Jesus Nava, product managers at Dormer Pramet Inc., Elgin, Illinois. For example, they stated, “HSS continues to be popular due to its high hardness and wear resistance at an affordable price. But its best feature is its toughness.”
In addition, “HSS performs very well with intermittent cutting applications,” they wrote.
Even the concluding sentences of both articles strike a similar chord. McAuliffe wrote, “With an ever widening choice of high speed steels from which to choose, it is doubtful if this type of material will be replaced as the backbone of tool materials in the foreseeable future.” And Kirchoff and Nava stated, “HSS remains a key component that offers customers what has always been essential: choice.”
Like CTE, HSS also had a different name when it premiered, which was around 1900. It was known as “Taylor-White” steel. I wonder if any remnants remain.
Related Glossary Terms
- hardness
hardness
Hardness is a measure of the resistance of a material to surface indentation or abrasion. There is no absolute scale for hardness. In order to express hardness quantitatively, each type of test has its own scale, which defines hardness. Indentation hardness obtained through static methods is measured by Brinell, Rockwell, Vickers and Knoop tests. Hardness without indentation is measured by a dynamic method, known as the Scleroscope test.
- high-speed steels ( HSS)
high-speed steels ( HSS)
Available in two major types: tungsten high-speed steels (designated by letter T having tungsten as the principal alloying element) and molybdenum high-speed steels (designated by letter M having molybdenum as the principal alloying element). The type T high-speed steels containing cobalt have higher wear resistance and greater red (hot) hardness, withstanding cutting temperature up to 1,100º F (590º C). The type T steels are used to fabricate metalcutting tools (milling cutters, drills, reamers and taps), woodworking tools, various types of punches and dies, ball and roller bearings. The type M steels are used for cutting tools and various types of dies.
- wear resistance
wear resistance
Ability of the tool to withstand stresses that cause it to wear during cutting; an attribute linked to alloy composition, base material, thermal conditions, type of tooling and operation and other variables.