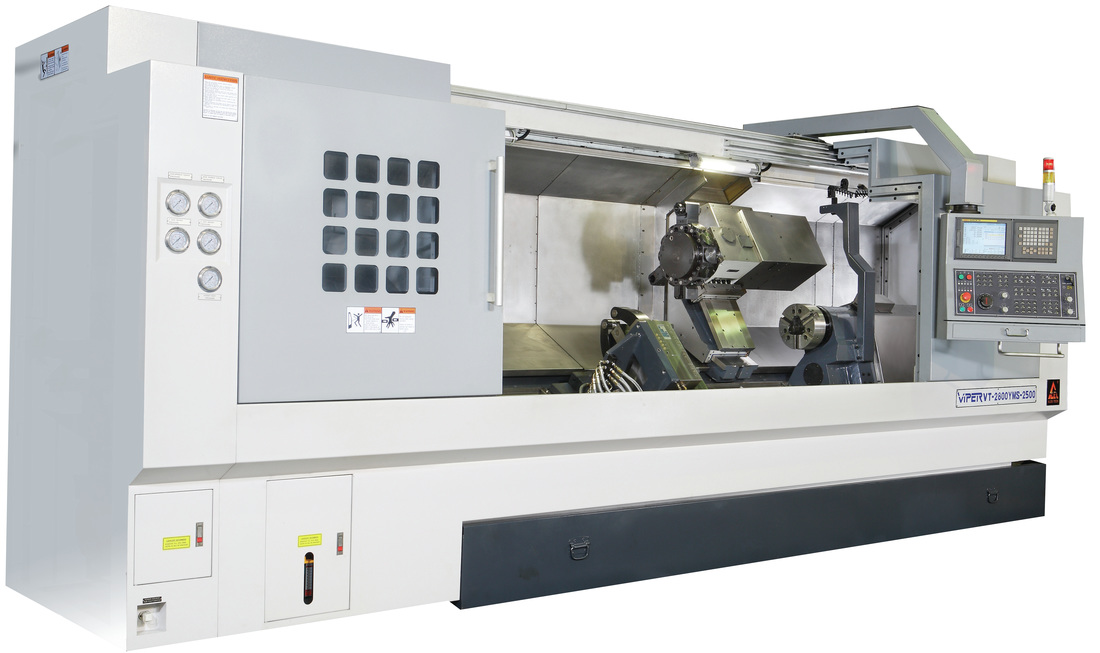
Sept. 25 marked 39 years to the day since I first stood in front of a Hardinge hand screw, scratching my head over the knobs and handles and wondering what I’d gotten myself into. To say that machine tools have improved since then is like saying this year’s computers are only slightly more powerful than those of a decade ago or that salted caramel ice cream is marginally more flavorful than vanilla. Today’s machine tools rock.
Take flexible manufacturing systems, the machining equivalent of a fast-food restaurant but one that makes far higher-quality food. There are Swiss-style lathes that turn, mill, drill and now laser-cut parts in a single operation, parts that would once have needed hand screws, Bridgeports and drill presses to complete. A similar situation exists with hybrid lathes and mills, which can add material almost as quickly as they remove it. Does this mean no more scrap?
But what really gets me are Y-axis machines. Live tooling and C-axis lathes have been around for decades, but it wasn’t until builders added that fourth axis that things got interesting. Suddenly it was super-easy to mill square pockets on round parts and drill off-center holes, operations that the turning department once relied on the milling department to perform.
As my good friend Yusuf Venjara, the former general manager of engineering for the now-defunct Hitachi Seiki, once said, roughly two-thirds of all turned parts require secondary milling operations, and a Y-axis takes care of a big chunk of them. Why wouldn’t someone want this capability?
There’s something else, however, that neither Yusuf nor the other machine tool experts anticipated when these machines were introduced: their cutoff capabilities.
As you might have guessed, I’m an old lathe guy. I’ve fought with cutoff tools since my hand screw days—we used hand-sharpened HSS blades back then—to the point that I gradually developed a love-hate relationship with cutoff tools. They’re like a hunting dog with poor eyesight—they get the job done eventually, but you wish they’d move a little faster.
Enter Y-axis parting. It’s said to be three times faster than a traditional X-axis cutoff tool. I’m not naming the manufacturer, but I’m sure that Google can find it if you’re interested. Take a look at the video. I probably watched it 10 times before I figured out just what the heck they are doing. One thing is for sure: Those Swedes are clever people, which as a Norwegian I have a hard time admitting.
Anyway, if you’re lucky enough to have a Y-axis lathe, I encourage you to check that out. It’s just one more example of how great it is to be in manufacturing right now and how technology enables even better technology, not unlike Moore’s law, which states that computing power doubles every 2 years. Machine tools haven’t quite kept up with this maxim, but they’re still awesome and getting a little more awesome every year.
Related Glossary Terms
- cutoff
cutoff
Step that prepares a slug, blank or other workpiece for machining or other processing by separating it from the original stock. Performed on lathes, chucking machines, automatic screw machines and other turning machines. Also performed on milling machines, machining centers with slitting saws and sawing machines with cold (circular) saws, hacksaws, bandsaws or abrasive cutoff saws. See saw, sawing machine; turning.
- gang cutting ( milling)
gang cutting ( milling)
Machining with several cutters mounted on a single arbor, generally for simultaneous cutting.
- high-speed steels ( HSS)
high-speed steels ( HSS)
Available in two major types: tungsten high-speed steels (designated by letter T having tungsten as the principal alloying element) and molybdenum high-speed steels (designated by letter M having molybdenum as the principal alloying element). The type T high-speed steels containing cobalt have higher wear resistance and greater red (hot) hardness, withstanding cutting temperature up to 1,100º F (590º C). The type T steels are used to fabricate metalcutting tools (milling cutters, drills, reamers and taps), woodworking tools, various types of punches and dies, ball and roller bearings. The type M steels are used for cutting tools and various types of dies.
- lathe
lathe
Turning machine capable of sawing, milling, grinding, gear-cutting, drilling, reaming, boring, threading, facing, chamfering, grooving, knurling, spinning, parting, necking, taper-cutting, and cam- and eccentric-cutting, as well as step- and straight-turning. Comes in a variety of forms, ranging from manual to semiautomatic to fully automatic, with major types being engine lathes, turning and contouring lathes, turret lathes and numerical-control lathes. The engine lathe consists of a headstock and spindle, tailstock, bed, carriage (complete with apron) and cross slides. Features include gear- (speed) and feed-selector levers, toolpost, compound rest, lead screw and reversing lead screw, threading dial and rapid-traverse lever. Special lathe types include through-the-spindle, camshaft and crankshaft, brake drum and rotor, spinning and gun-barrel machines. Toolroom and bench lathes are used for precision work; the former for tool-and-die work and similar tasks, the latter for small workpieces (instruments, watches), normally without a power feed. Models are typically designated according to their “swing,” or the largest-diameter workpiece that can be rotated; bed length, or the distance between centers; and horsepower generated. See turning machine.
- milling
milling
Machining operation in which metal or other material is removed by applying power to a rotating cutter. In vertical milling, the cutting tool is mounted vertically on the spindle. In horizontal milling, the cutting tool is mounted horizontally, either directly on the spindle or on an arbor. Horizontal milling is further broken down into conventional milling, where the cutter rotates opposite the direction of feed, or “up” into the workpiece; and climb milling, where the cutter rotates in the direction of feed, or “down” into the workpiece. Milling operations include plane or surface milling, endmilling, facemilling, angle milling, form milling and profiling.
- milling machine ( mill)
milling machine ( mill)
Runs endmills and arbor-mounted milling cutters. Features include a head with a spindle that drives the cutters; a column, knee and table that provide motion in the three Cartesian axes; and a base that supports the components and houses the cutting-fluid pump and reservoir. The work is mounted on the table and fed into the rotating cutter or endmill to accomplish the milling steps; vertical milling machines also feed endmills into the work by means of a spindle-mounted quill. Models range from small manual machines to big bed-type and duplex mills. All take one of three basic forms: vertical, horizontal or convertible horizontal/vertical. Vertical machines may be knee-type (the table is mounted on a knee that can be elevated) or bed-type (the table is securely supported and only moves horizontally). In general, horizontal machines are bigger and more powerful, while vertical machines are lighter but more versatile and easier to set up and operate.
- parting
parting
When used in lathe or screw-machine operations, this process separates a completed part from chuck-held or collet-fed stock by means of a very narrow, flat-end cutting, or parting, tool.
- turning
turning
Workpiece is held in a chuck, mounted on a face plate or secured between centers and rotated while a cutting tool, normally a single-point tool, is fed into it along its periphery or across its end or face. Takes the form of straight turning (cutting along the periphery of the workpiece); taper turning (creating a taper); step turning (turning different-size diameters on the same work); chamfering (beveling an edge or shoulder); facing (cutting on an end); turning threads (usually external but can be internal); roughing (high-volume metal removal); and finishing (final light cuts). Performed on lathes, turning centers, chucking machines, automatic screw machines and similar machines.