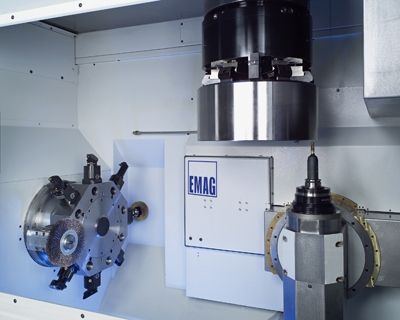
Mass production components always present challenges: planning the machine installation site, linking machines and coordinating cycle times all to achieve the perfect combination of quality and cost efficiency. The larger the workpiece the more demanding the planning process for the manufacturing set-up. However, optimizing the production of such parts, for example by reducing expensive automation components or reducing the process chain to just a few machines, can drastically cut costs. EMAG's VLC 800 vertical turning center for chucked parts up to 800mm is a production system that combines all these benefits in a single machine thanks to its integrated automation systems.
A customizable machine, as the "C" in the name indicates, the VLC 800 vertical turning center can be configured for a wide range of applications. Combining multiple modules to choose from and the time-tested EMAG modular design means that the VLC's machining area can be configured for a wide range of machining tasks. For example, the machine can be fitted with two tool turrets equipped with driven tools and, as an option, can travel on an additional X-axis. Furthermore, drilling and milling spindles with tool magazines can be mounted on a Y-B-axis unit. As a result of the machines' high strength and precision, they can also tackle grinding and hard machining. The VLC 800 can be used for almost any type of machining on large workpieces.
The sturdy main spindle with a drive rating of up to 74 kW, 4400 Nm of torque and speeds up to 500 rpm ensures that machining processes are completed quickly. The Mineralit polymer concrete machine base is made using a cold casting process for particularly good vibration damping, which in turn minimizes tool wear and delivers excellent surface quality. The spindle motor, main spindle, tool turret, electrical cabinet and machine body are liquid-cooled. A dual-circuit cooling unit readjusts the machine temperature to the ambient temperature within close tolerances. Consequently, VLC turning centers produce even large components with accuracies in the range of a hundredth of a millimeter. For optimal quality control, however, an optional probe can be installed outside the machining area to verify dimensions. Not only is the probe protected from chips, but the measurement is carried out just before the loading or unloading process, saving time.
Naturally, the VLC 800 also features the typical EMAG pick-up system consisting of an included parts storage facility and pick-up spindle. Raw parts are placed on the integrated conveyor belt for transport in and out of the machine either by hand or using additional automation components. The spindle picks up the workpiece from the conveyor and guides it to the various stations in the machining area. The short distances from the conveyor belt to the machining areas and back minimize the chip-to-chip times and ensure excellent efficiency. The integrated automation system also simplifies the structure of production lines since there is no need for complicated automation systems to load the machines. All that is required is a part transport system between the conveyor belts, easily achievable with simple automation components such as additional conveyors, pick-and-place units or changers. Using as few components as feasible also reduces possible fault sources.
Excellent accessibility to all relevant machine zones is ensured by the vertical design, as convenient access to the machining area ensures very short tooling times with perfect ergonomics for the set-up technician. All the service units are also laid out for ease of accessibility to make machine maintenance convenient and efficient.
EMAG's VLC 800 vertical turning center is designed for large workpieces and can be used for a wide range of applications due to the great flexibility of its equipment features. The VLC 800 also allows the complete machining of large chucked parts in a single clamping cycle. The integration of different processes and technologies ensures a drastic reduction in process chains and thus creates optimized production processes. One of the most flexible and productive manufacturing systems for large components on the market, the VLC 800 offers manufacturing engineers a wide range of possible uses.
Contact Details
Related Glossary Terms
- centers
centers
Cone-shaped pins that support a workpiece by one or two ends during machining. The centers fit into holes drilled in the workpiece ends. Centers that turn with the workpiece are called “live” centers; those that do not are called “dead” centers.
- gang cutting ( milling)
gang cutting ( milling)
Machining with several cutters mounted on a single arbor, generally for simultaneous cutting.
- grinding
grinding
Machining operation in which material is removed from the workpiece by a powered abrasive wheel, stone, belt, paste, sheet, compound, slurry, etc. Takes various forms: surface grinding (creates flat and/or squared surfaces); cylindrical grinding (for external cylindrical and tapered shapes, fillets, undercuts, etc.); centerless grinding; chamfering; thread and form grinding; tool and cutter grinding; offhand grinding; lapping and polishing (grinding with extremely fine grits to create ultrasmooth surfaces); honing; and disc grinding.
- milling
milling
Machining operation in which metal or other material is removed by applying power to a rotating cutter. In vertical milling, the cutting tool is mounted vertically on the spindle. In horizontal milling, the cutting tool is mounted horizontally, either directly on the spindle or on an arbor. Horizontal milling is further broken down into conventional milling, where the cutter rotates opposite the direction of feed, or “up” into the workpiece; and climb milling, where the cutter rotates in the direction of feed, or “down” into the workpiece. Milling operations include plane or surface milling, endmilling, facemilling, angle milling, form milling and profiling.
- modular design ( modular construction)
modular design ( modular construction)
Manufacturing of a product in subassemblies that permits fast and simple replacement of defective assemblies and tailoring of the product for different purposes. See interchangeable parts.
- quality assurance ( quality control)
quality assurance ( quality control)
Terms denoting a formal program for monitoring product quality. The denotations are the same, but QC typically connotes a more traditional postmachining inspection system, while QA implies a more comprehensive approach, with emphasis on “total quality,” broad quality principles, statistical process control and other statistical methods.
- turning
turning
Workpiece is held in a chuck, mounted on a face plate or secured between centers and rotated while a cutting tool, normally a single-point tool, is fed into it along its periphery or across its end or face. Takes the form of straight turning (cutting along the periphery of the workpiece); taper turning (creating a taper); step turning (turning different-size diameters on the same work); chamfering (beveling an edge or shoulder); facing (cutting on an end); turning threads (usually external but can be internal); roughing (high-volume metal removal); and finishing (final light cuts). Performed on lathes, turning centers, chucking machines, automatic screw machines and similar machines.