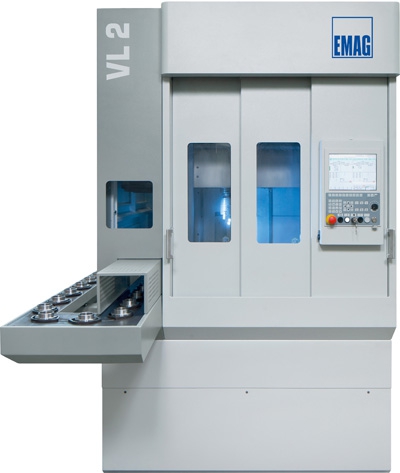
Nowadays, everywhere you turn in an industrial production environment you encounter the expression "downsizing," where the term describes infinitely more than just the scaling down of the passenger car engine and its displacement. There is also a change in the direction the production of electric motors and pumps for the energy industry and for general mechanical engineering is taking, with constituent components getting smaller and smaller. However, the trend towards downsizing increases demands for greater precision and that makes the manufacture of small components a real challenge."Shrinking" components and new smaller components present a particularly complex task for the mechanical engineering companies that manufacture them. One kind of machine used to master the task is shown by the turning specialists at EMAG with the VL 2. This vertical turning machine represents a new platform for automated, high-precision production processes and low component costs in the manufacture of small chucked components.
The EMAG VL2 machine opens up new opportunities for the machining of a wide range of small chucked components. Small gear wheels, planetary gears, sliding sleeves, pump components, synchronizer rings, chain gears or flange components, with a maximum diameter of 100mm and a length of up to 150mm, are machined on a vertical pick-up lathe with great efficiency. The machine design focuses on providing a variety of manufacturing technologies for soft and hard machining plus a complete automation system at a very favorable price-performance ratio. When developing the VL 2, EMAG had its eyes fixed firmly on the investment costs for the user and the fact that those costs should be kept as low as possible.
This comparatively small, space-saving manufacturing solution also includes a number of details and high-tech components that guarantee fast processing: The pick-up spindle ensures that the machine loads itself. It picks up the raw parts from the integral conveyor belt (which accommodates up to 24 workpieces) and later returns the finish machined component to it. The 12-station tool turret features very short indexing times. For drilling and milling operations, it can also be equipped with driven tools in all 12 stations. All service units are quickly and freely accessible. The distance between operator and turret, for instance, does not exceed 400mm. The machine base of polymer concrete MINERALIT ensures great stability and has outstanding damping qualities, a direct source for exceptional surface finishes.
"We wanted to design a machine that guaranteed the highest possible degree of productivity in the manufacture of small components and we have been very successful in that pursuit with our VL 2. Here, too, size is of great importance. The machine's compact construction ensures that the chip-to-chip times are kept low," explains Guido Hegener, Managing Director of EMAG Salach Maschinenfabrik GmbH.
Productivity levels on the VL 2 are approximately 15 percent higher than those of comparable automated horizontal turning machines, according to Hegener. When talking about component quality, one needs to consider another central and very typical EMAG design factor besides the sturdy machine base: namely, the alignment of all process-related components inside the machine. Work spindle and workpiece are both located above the tools. This guarantees the optimal flow of chips and prevents the formation of clusters, offering a maximum of consistent process integrity, also an important factor where a link-up of multiple VL 2 machines in a work center or transfer line is envisioned. The automation equipment is positioned to suit user requirements, an optimal precondition for the use of the machine in production lines.
"The VL 2 is designed for flexibility," continues Guido Hegener. "The technology, from automation to interfaces and control system, can be chosen to suit onsite conditions."
It is, for instance, possible to include an optional Y-axis or measuring probe. Where, on the basic machine, the work spindle is mounted on a compound slide that moves in X and Z, the VL 2 can also be equipped with an optional Y-axis inside the turret. This allows more efficient machining of highly complex geometries. Low component costs, stable processes, high component quality and an optimal price-performance ratio altogether. it should not come as a surprise that, with such a value proposition, the turning specialists at EMAG are predicting an exceptional market opportunity for this new machine platform.
"We are convinced that this solution will be well received and used for a number of different applications in different market places. The machine represents a complete, highly efficient manufacturing solution that is displaying its strengths both at new production facilities in the emerging Asian markets, as well as at existing production facilities in Europe and the USA. The technology allows us to pinpoint, optimize and expand the machining of small chucked components, as required. And those advantages are sure to prevail in the market place," concludes Guido Hegener.
Contact Details
Related Glossary Terms
- gang cutting ( milling)
gang cutting ( milling)
Machining with several cutters mounted on a single arbor, generally for simultaneous cutting.
- lathe
lathe
Turning machine capable of sawing, milling, grinding, gear-cutting, drilling, reaming, boring, threading, facing, chamfering, grooving, knurling, spinning, parting, necking, taper-cutting, and cam- and eccentric-cutting, as well as step- and straight-turning. Comes in a variety of forms, ranging from manual to semiautomatic to fully automatic, with major types being engine lathes, turning and contouring lathes, turret lathes and numerical-control lathes. The engine lathe consists of a headstock and spindle, tailstock, bed, carriage (complete with apron) and cross slides. Features include gear- (speed) and feed-selector levers, toolpost, compound rest, lead screw and reversing lead screw, threading dial and rapid-traverse lever. Special lathe types include through-the-spindle, camshaft and crankshaft, brake drum and rotor, spinning and gun-barrel machines. Toolroom and bench lathes are used for precision work; the former for tool-and-die work and similar tasks, the latter for small workpieces (instruments, watches), normally without a power feed. Models are typically designated according to their “swing,” or the largest-diameter workpiece that can be rotated; bed length, or the distance between centers; and horsepower generated. See turning machine.
- milling
milling
Machining operation in which metal or other material is removed by applying power to a rotating cutter. In vertical milling, the cutting tool is mounted vertically on the spindle. In horizontal milling, the cutting tool is mounted horizontally, either directly on the spindle or on an arbor. Horizontal milling is further broken down into conventional milling, where the cutter rotates opposite the direction of feed, or “up” into the workpiece; and climb milling, where the cutter rotates in the direction of feed, or “down” into the workpiece. Milling operations include plane or surface milling, endmilling, facemilling, angle milling, form milling and profiling.
- turning
turning
Workpiece is held in a chuck, mounted on a face plate or secured between centers and rotated while a cutting tool, normally a single-point tool, is fed into it along its periphery or across its end or face. Takes the form of straight turning (cutting along the periphery of the workpiece); taper turning (creating a taper); step turning (turning different-size diameters on the same work); chamfering (beveling an edge or shoulder); facing (cutting on an end); turning threads (usually external but can be internal); roughing (high-volume metal removal); and finishing (final light cuts). Performed on lathes, turning centers, chucking machines, automatic screw machines and similar machines.
- turning machine
turning machine
Any machine that rotates a workpiece while feeding a cutting tool into it. See lathe.