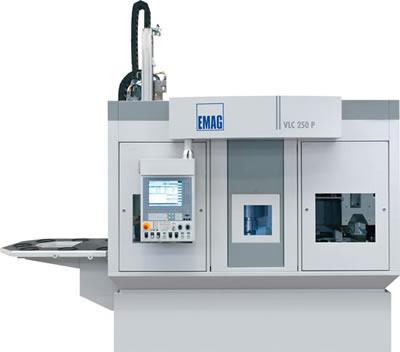
The VLC 250 P vertical turning machine from EMAG L.L.C., Farmington Hills, Mich., is said to reduce workpiece changeover time by 83 percent with the application of its pendulum technique. The time to change a chucked workpiece is 1 second compared with 6 seconds on traditional turning machines, according to EMAG.
To learn more about productivity enhancing technologies, such as the VLC 250 P, click here for a brief overview of the May 10-11 Technology Days event presented by EMAG L.L.C. |
Featuring a slide with two spindles that move in unison, the VLC 250 P is capable of holding the workpiece with one spindle while the other unloads a finished-machined component and picks up an unmachined workpiece. One spindle is always in the machining area with a workpiece being machined by X-axis turret tools. Turret indexing time is just 0.3 seconds.
The machining process is supported by a main spindle with a power rating of 28 kW and torque of up to 300 Nm. The turret, with VDI 50 tool receptors, accommodates 12 turning tools or up to 12 driven drilling or milling tools. A 250mm-dia. chuck holds workpieces of up to 200mm in diameter and 80mm in height.
With two spindles, the VLC 250 P and its compact, integral component "transfer+turning" station allow machining of both sides of the part in one machine, similar to many twin-spindle or opposed-spindle machines, but with much less idle time.
Technical Data:
- Chuck diameter: 250mm
- Swing diameter: 350mm
- Travel in X/Z: 600mm / 300mm
- Travel in X2 (turret): 230mm
- Workpiece diameter, max.: 200mm
- Workpiece height, max: 80mm
- Rapid traverse speed X/Z/X2: 60/30/30 m/min
Contact Details
Related Glossary Terms
- chuck
chuck
Workholding device that affixes to a mill, lathe or drill-press spindle. It holds a tool or workpiece by one end, allowing it to be rotated. May also be fitted to the machine table to hold a workpiece. Two or more adjustable jaws actually hold the tool or part. May be actuated manually, pneumatically, hydraulically or electrically. See collet.
- gang cutting ( milling)
gang cutting ( milling)
Machining with several cutters mounted on a single arbor, generally for simultaneous cutting.
- milling
milling
Machining operation in which metal or other material is removed by applying power to a rotating cutter. In vertical milling, the cutting tool is mounted vertically on the spindle. In horizontal milling, the cutting tool is mounted horizontally, either directly on the spindle or on an arbor. Horizontal milling is further broken down into conventional milling, where the cutter rotates opposite the direction of feed, or “up” into the workpiece; and climb milling, where the cutter rotates in the direction of feed, or “down” into the workpiece. Milling operations include plane or surface milling, endmilling, facemilling, angle milling, form milling and profiling.
- rapid traverse
rapid traverse
Movement on a CNC mill or lathe that is from point to point at full speed but, usually, without linear interpolation.
- turning
turning
Workpiece is held in a chuck, mounted on a face plate or secured between centers and rotated while a cutting tool, normally a single-point tool, is fed into it along its periphery or across its end or face. Takes the form of straight turning (cutting along the periphery of the workpiece); taper turning (creating a taper); step turning (turning different-size diameters on the same work); chamfering (beveling an edge or shoulder); facing (cutting on an end); turning threads (usually external but can be internal); roughing (high-volume metal removal); and finishing (final light cuts). Performed on lathes, turning centers, chucking machines, automatic screw machines and similar machines.
- turning machine
turning machine
Any machine that rotates a workpiece while feeding a cutting tool into it. See lathe.