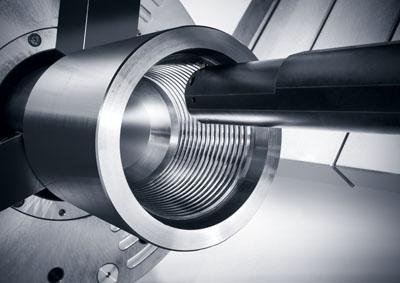
Hwacheon Machinery America has introduced a line of large turning centers specifically for machining large oil field components, called Big Bore, based on its successful Hi-Tech 550, -700, and -850 horizontal turning centers. Each turning center offers high spindle torque, permitting productive cutting in tough material up to 36" diameter and more than 216" in length.
The new Hi-TECH BB and BB+ turning centers feature through-spindle holes from 7.08" to 14.57" in diameter for large pipes. Maximum cutting diameter on the Hi-Tech 850BB is over 36". Large air chucks can be fitted at the front and back of the spindle. Specifically, the range is: HT-550BB with a 7.08" through-spindle hole; HT-700BB offers 7.08", BB+ 11.61" and HT850 has 11.61" with BB+ at 14.57". Spindle noses: ASA A2-15 to A2-20. Long bed versions of the centers are available from 84" to 216"
The 4-speed automatic transmission system allows low-speed, high-torque turning as well as high-speed machining. Ultra-precision recuperative cylindrical roller bearings and the multiple thrust angular bearing have been incorporated to enable hard turning of tough alloys. The spindle may be geared down for extra torque to process a wide range of materials. All machines feature Hwacheon's heavily ribbed torque tube design.
All BB turning centers are built with integrated bed frames of fine grain meehanite castings to minimize heat distortion. Plus, all guide ways are designed as solid box guide ways to maintain rigidity and precision even during prolonged, heavy operations. In addition, Hwacheon's advanced thermal displacement control prevents deterioration machining tolerances due to thermal displacement, according to the company. A jet of lubrication is constantly applied to the spindle bearing for lubrication and cooling, prolonging machine life and the machining precision.
Other features of the turning centers make them the ideal choice for cutting large parts. These include the best specification servo turret in its class, largest turret width (13") in its class, and a boring bar capacity to 31" In addition, the turning centers can handle multitasking machining with a Y axis head with stroke of 9" and rapid positioning speed of 10m/min.
Heavy-duty bearings in the turning center's tailstock assure a high degree of precision even after prolonged heavy-duty turning on a large, heavy workpieces. Machines also feature a 20,000 kg clamping force. Quill diameters range from 120mm to 160mm housed in a rugged built-in quill structure. The large steady rest capacity is 20" An air chuck is optional.
Each turning center is controlled by the Fanuc 0i control with Manual Guide i. Manual Guide i is a dialog-based programming system, allowing even a beginner to write an advanced program by following simple dialogs and menus. The data can easily be used to present a 3D model of the work and process, providing the operator with the preview of the actual outcome.
Contact Details
Related Glossary Terms
- alloys
alloys
Substances having metallic properties and being composed of two or more chemical elements of which at least one is a metal.
- boring
boring
Enlarging a hole that already has been drilled or cored. Generally, it is an operation of truing the previously drilled hole with a single-point, lathe-type tool. Boring is essentially internal turning, in that usually a single-point cutting tool forms the internal shape. Some tools are available with two cutting edges to balance cutting forces.
- boring bar
boring bar
Essentially a cantilever beam that holds one or more cutting tools in position during a boring operation. Can be held stationary and moved axially while the workpiece revolves around it, or revolved and moved axially while the workpiece is held stationary, or a combination of these actions. Installed on milling, drilling and boring machines, as well as lathes and machining centers.
- centers
centers
Cone-shaped pins that support a workpiece by one or two ends during machining. The centers fit into holes drilled in the workpiece ends. Centers that turn with the workpiece are called “live” centers; those that do not are called “dead” centers.
- chuck
chuck
Workholding device that affixes to a mill, lathe or drill-press spindle. It holds a tool or workpiece by one end, allowing it to be rotated. May also be fitted to the machine table to hold a workpiece. Two or more adjustable jaws actually hold the tool or part. May be actuated manually, pneumatically, hydraulically or electrically. See collet.
- hard turning
hard turning
Single-point cutting of a workpiece that has a hardness value higher than 45 HRC.
- steady rest
steady rest
Supports long, thin or flexible work being turned on a lathe. Mounts on the bed’s ways and, unlike a follower rest, remains at the point where mounted. See follower rest.
- turning
turning
Workpiece is held in a chuck, mounted on a face plate or secured between centers and rotated while a cutting tool, normally a single-point tool, is fed into it along its periphery or across its end or face. Takes the form of straight turning (cutting along the periphery of the workpiece); taper turning (creating a taper); step turning (turning different-size diameters on the same work); chamfering (beveling an edge or shoulder); facing (cutting on an end); turning threads (usually external but can be internal); roughing (high-volume metal removal); and finishing (final light cuts). Performed on lathes, turning centers, chucking machines, automatic screw machines and similar machines.