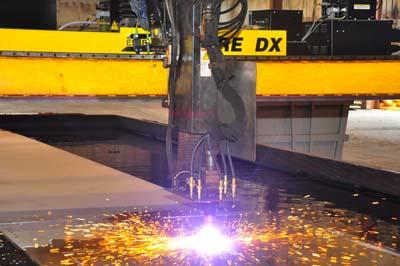
As a leading provider of stainless steel and nickel alloy plates and parts, Jacquet Metals knows that faster, cleaner cuts is the way to keep customers coming back. That is why they recently purchased upgrades to four plasma cutting machines. Jacquet provides stainless steel and nickel alloy plates and cut parts to metal distributors, fabricators in the chemical and petrochemical processing industries, the power generation industry (including nuclear and coal-fired power), and water waste treatment facilities. In these corrosive environments, customers need materials that are heat- and corrosion resistant, such as stainless steel and nickel alloy.
"We cut a lot of rings, discs, and shapes," says Ryan Hendrix, Jacquet Southeast Facility Manager. "We use the Sabre DX with an m3 plasma system featuring water injection capability from ESAB Cutting Systems because we need clean cuts with high edge quality."
Jacquet installed 5 new ESAB cutting machines from 2006 through 2008, and installed a 6th machine at its new location in Charlotte, NC in 2010. The Charlotte location was the first to use the water injection plasma system. "We were so pleased with water injection," says Terry Engle, Jacquet CEO. "We jumped on it pretty fast and ordered 4 for all of our North American facilities. We didn't order one at a time; we immediately retrofitted our cutting heads."
Water injection capability is designed to reduce the cost of cutting stainless steel and aluminum while improving edge quality and reducing dross formation. Water injection cutting offers cutting speeds up to 100 percent faster than gas-shielded systems. The ESAB m3 system allows the torch to switch automatically between standard dual-gas cutting and water-injected plasma cutting. Each of Jacquet's 6 ESAB cutting machines features a 600 Amp m3 plasma system, which gives them the capability to cut through stainless steel up to 6 inches thick. Water injection yields the best cut quality on materials up to 3 inches thick. But the system is so flexible it can easily handle precision plasma cutting all the way down to 10 gauge.
Thick plasma cutting of stainless steel and aluminum has traditionally been done using H-35 gas, a mixture of 65 percent argon and 35 percent hydrogen. Because water injection plasma uses only nitrogen gas and water, it is less expensive than plasma cutting with H-35.
"We have definitely seen a decrease in our costs," commented Hendrix. "We are impressed with the cut quality, reduced gas consumption, and tolerance of the ESAB m3 plasma system," stated Engle.
"The water injection cutting system provides a nicer finish on stainless steel plate than ordinary plasma cutting with a smaller heat affected zone (HAZ). Having less HAZ on the edges of the cuts is key to getting the clean finish customers want," continued Hendrix.
"The bulk of our production goes across those machines," stated Engle. "The ESAB machines are a critical part of our business, and we have been completely impressed with the results; that's why every Jacquet facility in North America uses ESAB. We're switching over to the water injection plasma head in every facility."
Related Glossary Terms
- numerical control ( NC)
numerical control ( NC)
Any controlled equipment that allows an operator to program its movement by entering a series of coded numbers and symbols. See CNC, computer numerical control; DNC, direct numerical control.
- tolerance
tolerance
Minimum and maximum amount a workpiece dimension is allowed to vary from a set standard and still be acceptable.