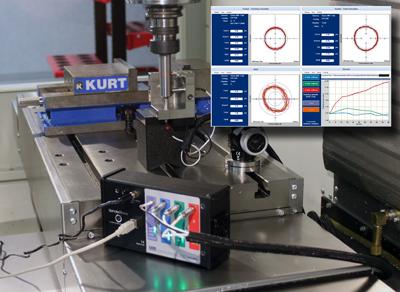
A precision machine shop ordered a new $1M machine. Before taking delivery, they measured the machine's capability including a "spindlecheck" of the rotating spindle. Measurements were not within specification and delivery was refused. The shop avoided a $1M investment in a machine that would not produce parts with the accuracy they required.
Another precision machine shop was going to replace a $15K spindle as a last-ditch effort to solve a surface finish problem. Fortunately, they decided to measure the spindle first. The spindle was fine. They discovered and remedied a much less expensive problem.
"SpindleChecking" is possible for a much larger segment of machine tool users thanks to the introduction of the SpindleCheck spindle qualification system from Lion Precision. SpindleCheck empowers maintenance departments and machine operators to know how a machine is performing before making parts. It is designed to make spindle measurement of rotational and thermal errors fast and easy. While measurements like those in the true stories above have been possible for years, SpindleCheck has reduced the cost and complexity of the measurement.
Because operators and maintenance personnel haven't had access to dynamic spindle measurement equipment, spindle performance had been a neglected measurement in machine tool maintenance; yet it provides critical data for preventive maintenance, problem analysis, and cost savings. Multiple money-saving scenarios promise to significantly affect a shop's bottom line via SpindleCheck: qualify a new machine before delivery; faster installation verification; prevent unnecessary spindle rebuilds; troubleshoot form errors in parts; preventive and predictive maintenance; planned downtime rather than unexpected production stoppages and missed delivery dates.
Thermal drift is the biggest contributor to machining and part errors. SpindleCheck measures changes in the point of machining as the spindle warms up, as chillers run, as the environment changes etc. Precise warm-up times can be determined for each machine and sources of thermal drift can be identified. This is the only method that tests thermal effects at the point of machining.
SpindleCheck is a system of software, noncontact capacitive sensors, and precision target pins. The target pins are placed in a tool holder in the spindle. The sensors are installed in a "nest" and mounted to the machine table. The target is moved into position in front of the probes. The spindle is rotated at full operational speeds while the sensors and software capture, analyze, and display the error motions in X, Y, and Z axes. SpindleCheck directly measures what happens at the point of machining, where the tool contacts the workpiece. SpindleCheck tests are compliant with tests indicated in ANSI, ISO, and JIS machine tool standards.
"Machine shops can run with confidence when they know how machines are behaving," according to Don Martin, president of Lion Precision. "It's a great asset to know which job goes on which machine depending on the tolerances required; even better to know when error motions are increasing and a machine is in need of maintenance – before it fails."